After picking up a HPFP for a friends Golf R from AKS yesterday Alex suggested I get my thread up on here

Well here we go! I've copied and pasted it from another forum I'm on but hopefully it makes sense.
Built In A Barn: 4motion 450bhp Mk2 GTI
With a few of my close friends telling me I should put some sort of build thread together for my little project here goes! What started off as simply having my Mk4 GTI remapped and a few little bits here and there quickly lead to the following.
After deciding I’d quickly get bored of the 220 ish horse power on offer from the simple remap I decided to look at moving to a “big turbo” conversion. This would have meant replacing at least the conrods to cope with the additional power that would be available.
One thing lead to another and the motor quickly ended up being more than just rods. The intention was to always drop the motor into my FWD Mk4 but I have always wanted a MK2 for as long as I’ve been into cars. A new job earlier in the year has/will hopefully give me the funds and time to now build what I have always wanted!
With the sort of power I’m looking at I started to look at a 4 wheel drive conversion. Synco parts are now going for crazy money and my fear of breaking a syncro part and the car being off the road for months whilst I located a replacement drive shaft in the UK for example didn’t sound that appealing.
My only feasible option was to look at using the 4motion/Quattro running gear from the TT/S3/R32 etc….
I will try and update this as often as I can,
If anyone’s on Instagram just search
@sa_engineering as I update that quite a regularly.
So this is where I’m up to!
Chassis: (Working on)
1989 Small Bumper mk2 Golf GTi
Audi TT mk1 Quattro Subframes And Associated Parts
Audi TT 312mm Front Brakes (For now)
Audi TT Rear Brakes (For now)
Suspension TT Front shocks, Mk2 Rear shocks/springs.
Wheels Round ones
Engine Spec: Now Complete (Estimated 430-450hp then can start playing with some water meth.
1.8T Block Bored To 82mm (1825cc)
AGU Crank And Pegged Pulley
Integrated Engineering 20mm Rifle Drilled Conrods
Wossner Forged Pistons 1mm Oversize
AGU Big Port Head, Ported
SuperTech Single Collet Valves, Springs, Titanium Retainers.
Piper Cams
All New OEM Oil Pump, Water Pump, Tensioners, Cam Chain, Etc
Integrated Engineering Manual Cambelt Tensioner
Gates Kevlar Cam Belt
02M Gearbox
GTX3071 .63 Tial Hotside (Owen Developments Built)
Part 1: From the beginning
I located a crash damaged 20v Audi A3 for less than £200. The engine was removed, the rest sold on/scrapped.
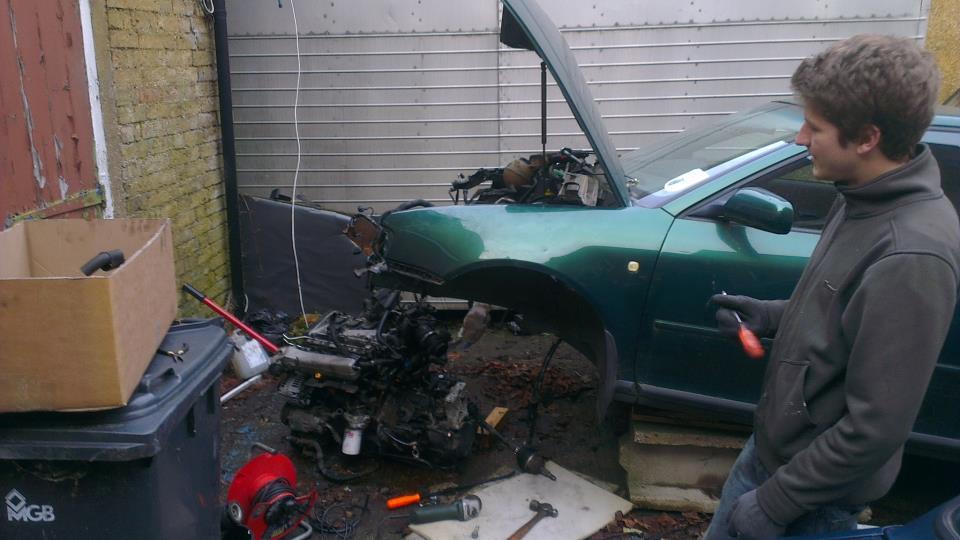
The car had done just over 145k before it had a car slide into it in the snow a couple of years ago. The owner began to strip off the bent and broken parts with the intention of repairing it himself. He quickly lost interest and it found its way into my hands for effectively scrap value.
I quickly set to work with a friend of mine pulling the motor apart. It was in fantastic condition considering the mileage on it. It didn’t really matter what we found as 95% of it was going to be replaced.
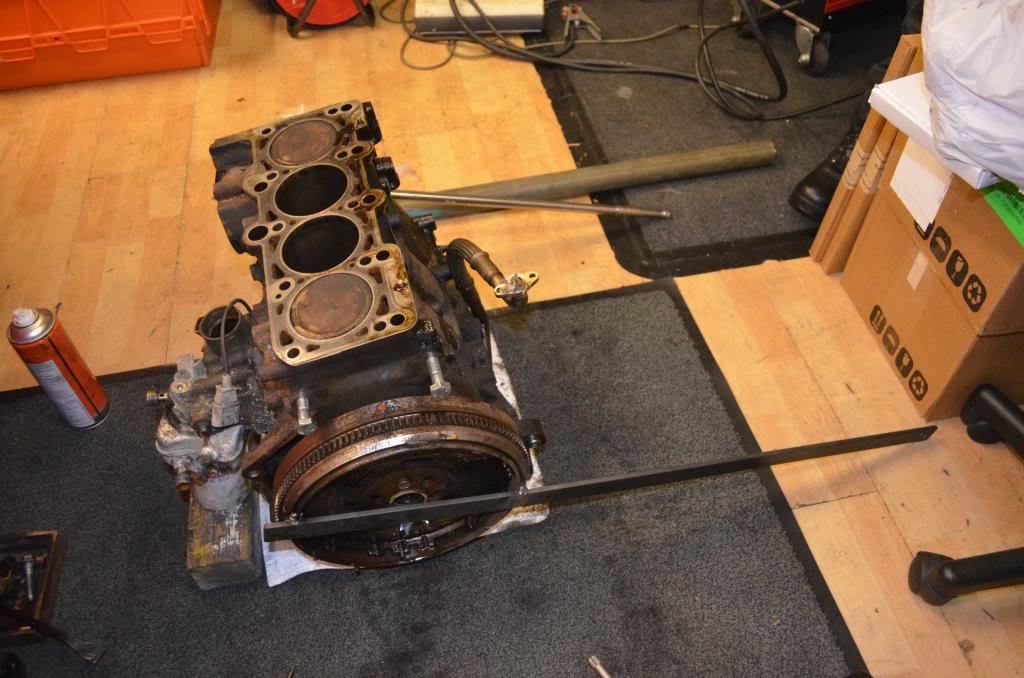
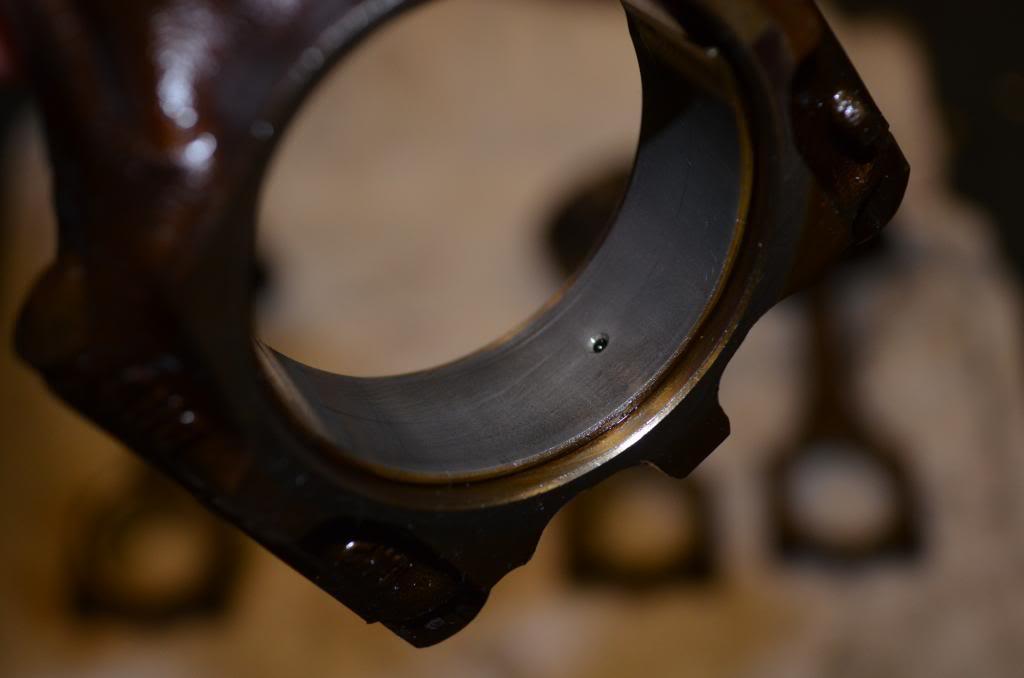
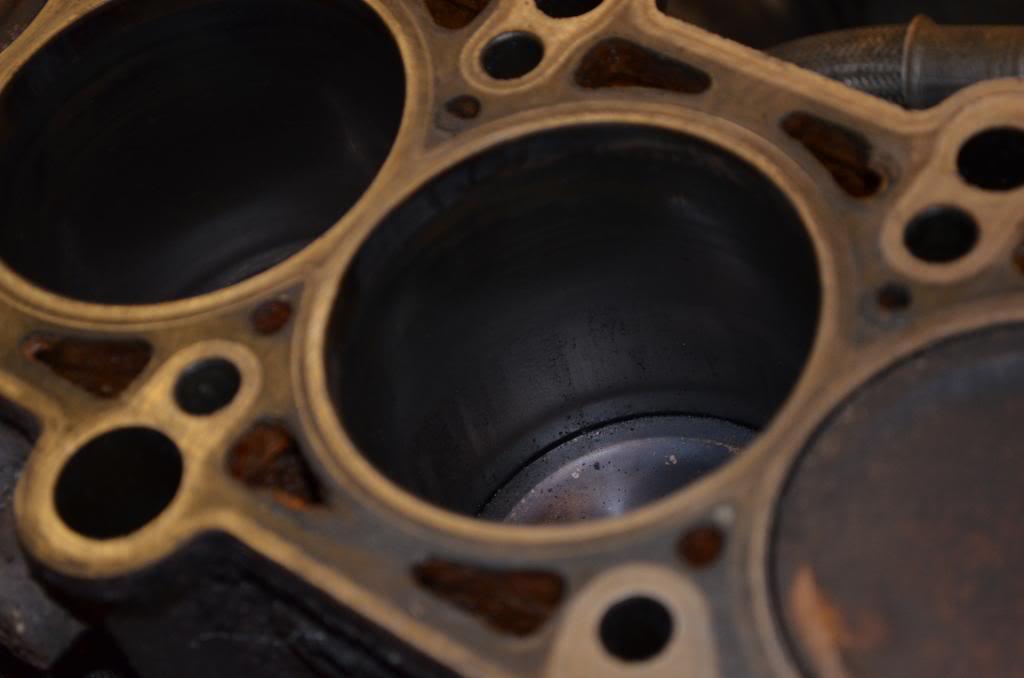
Bare Block:
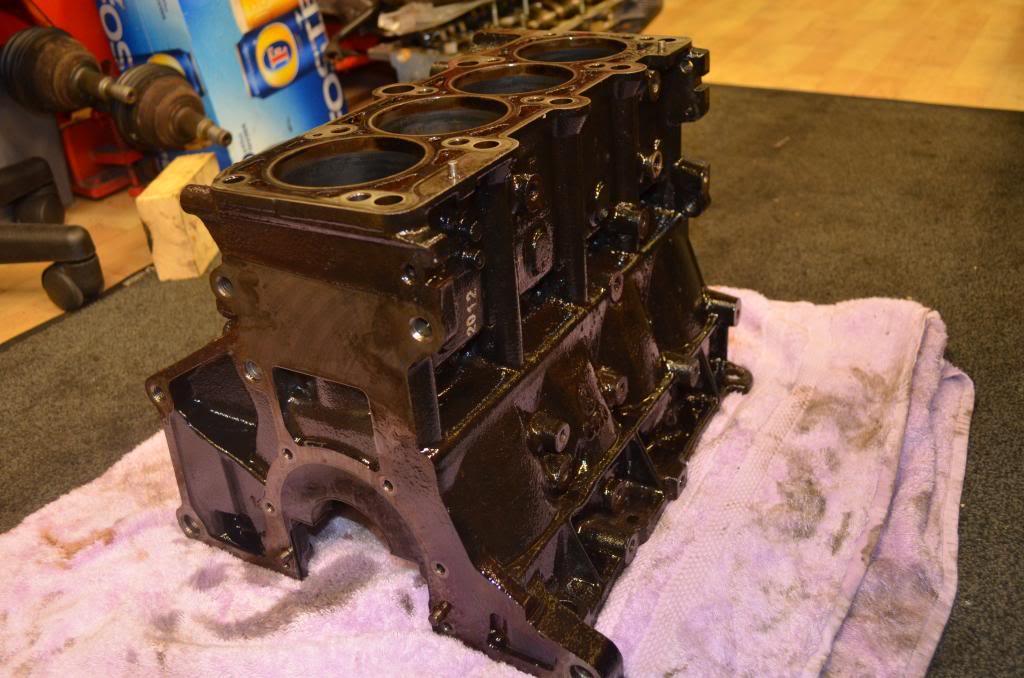
The head was the main deciding factor as it was the large port AGU version, ideal for what I wanted to build.
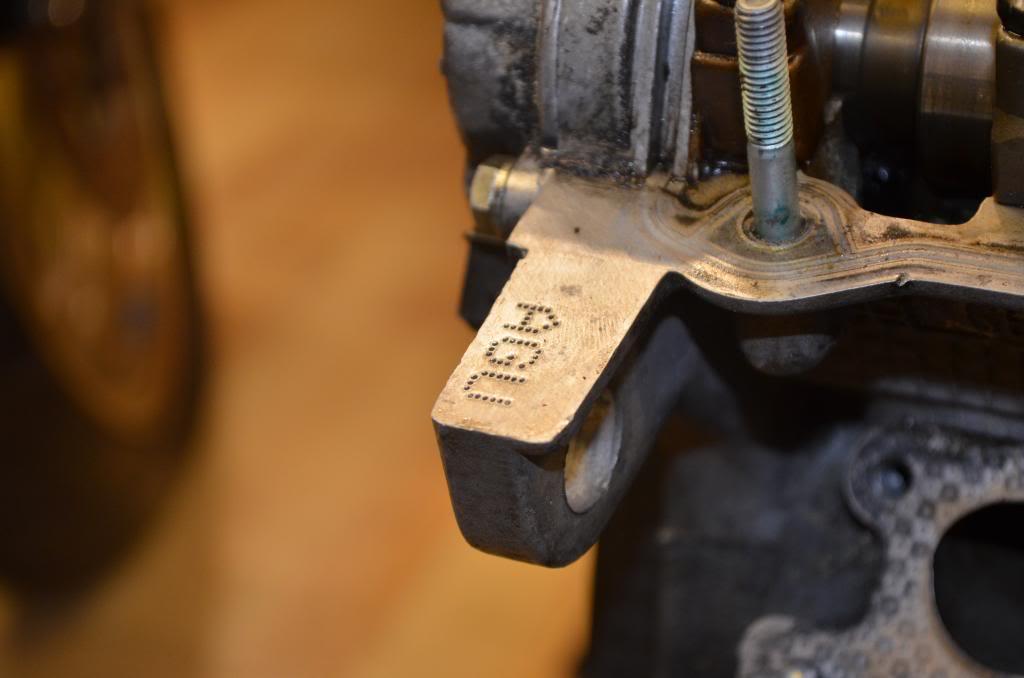
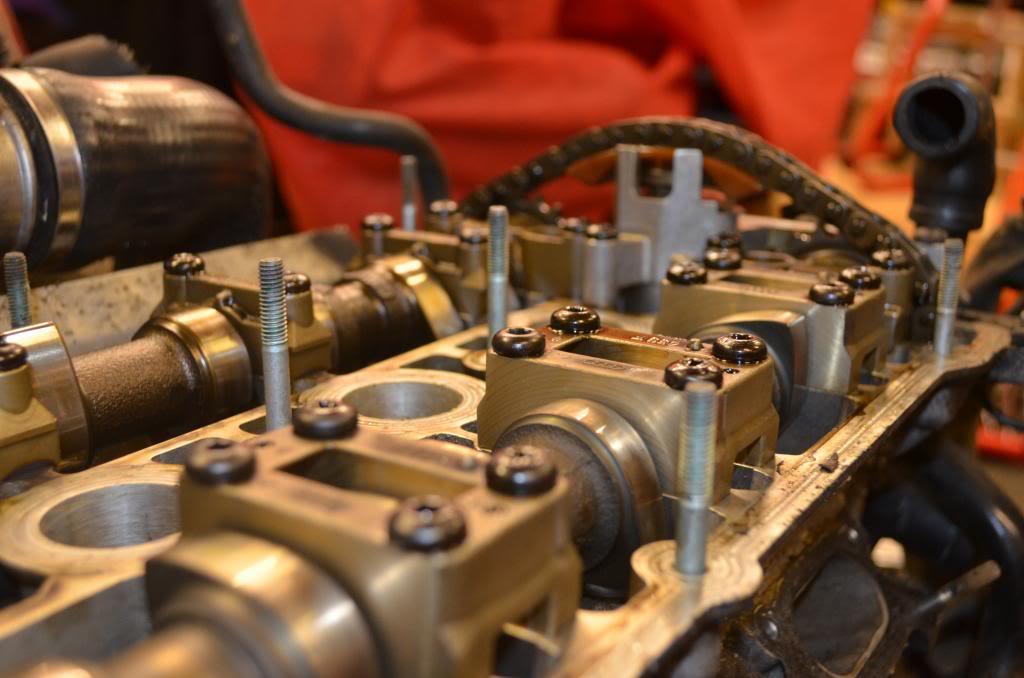
Head Fully Stripped:
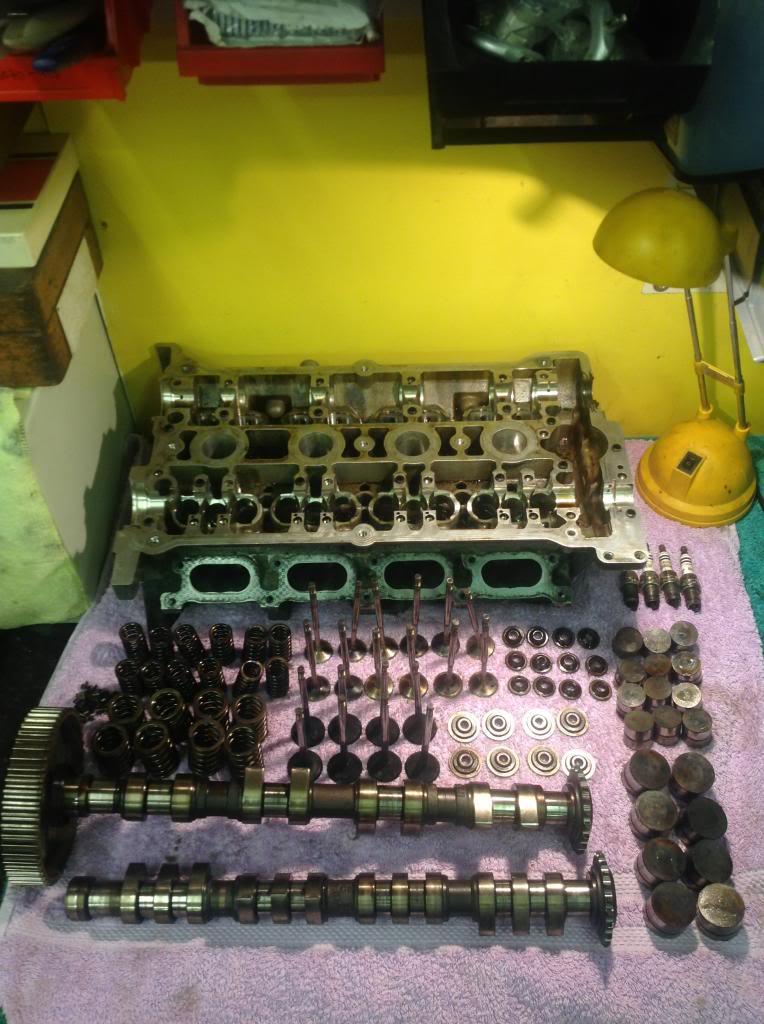
Part 2: Rebuilding Bottom End
With the block back from being re-bored to 82mm I spent a few hours cleaning up what was left of the old paint and surface rust prior to painting.
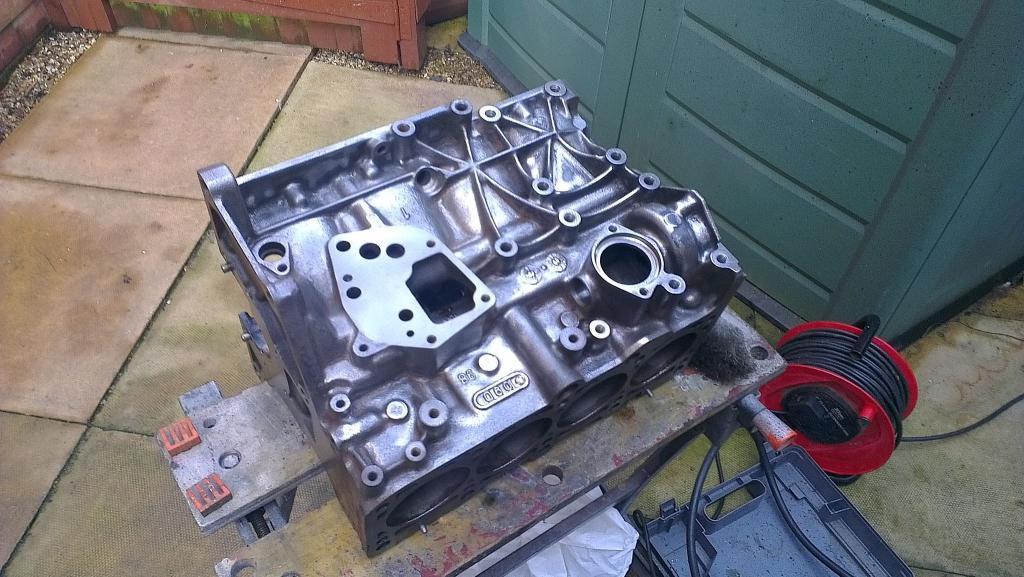
A nice delivery of parts showed up at work
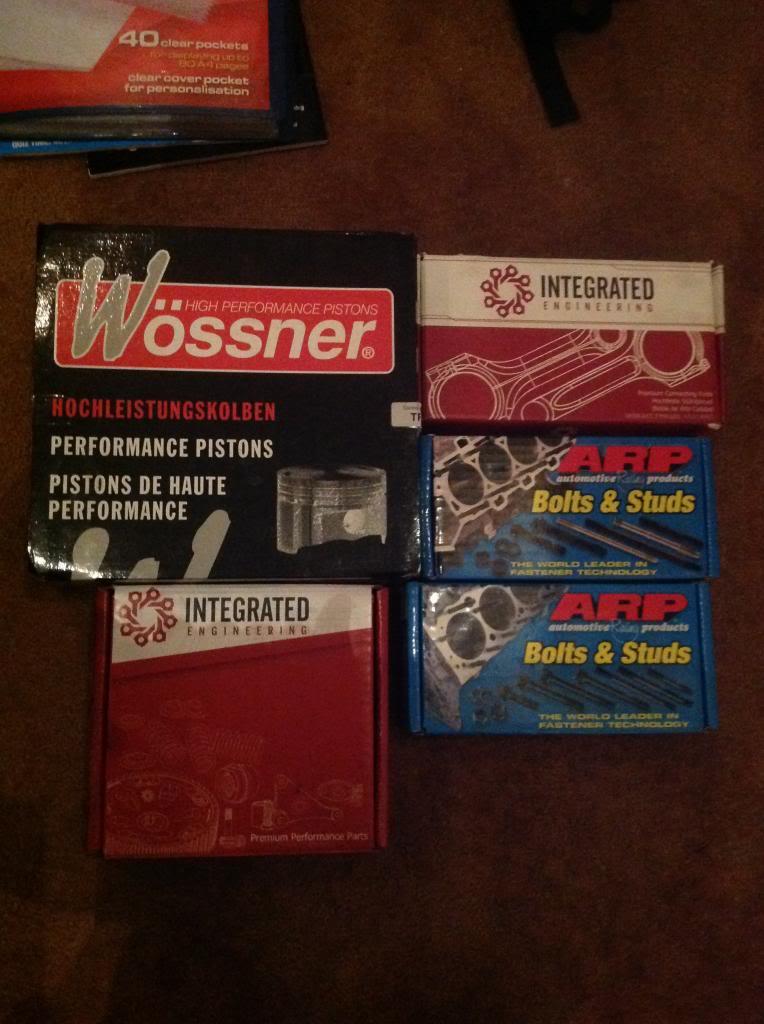
Rings being gapped and measured
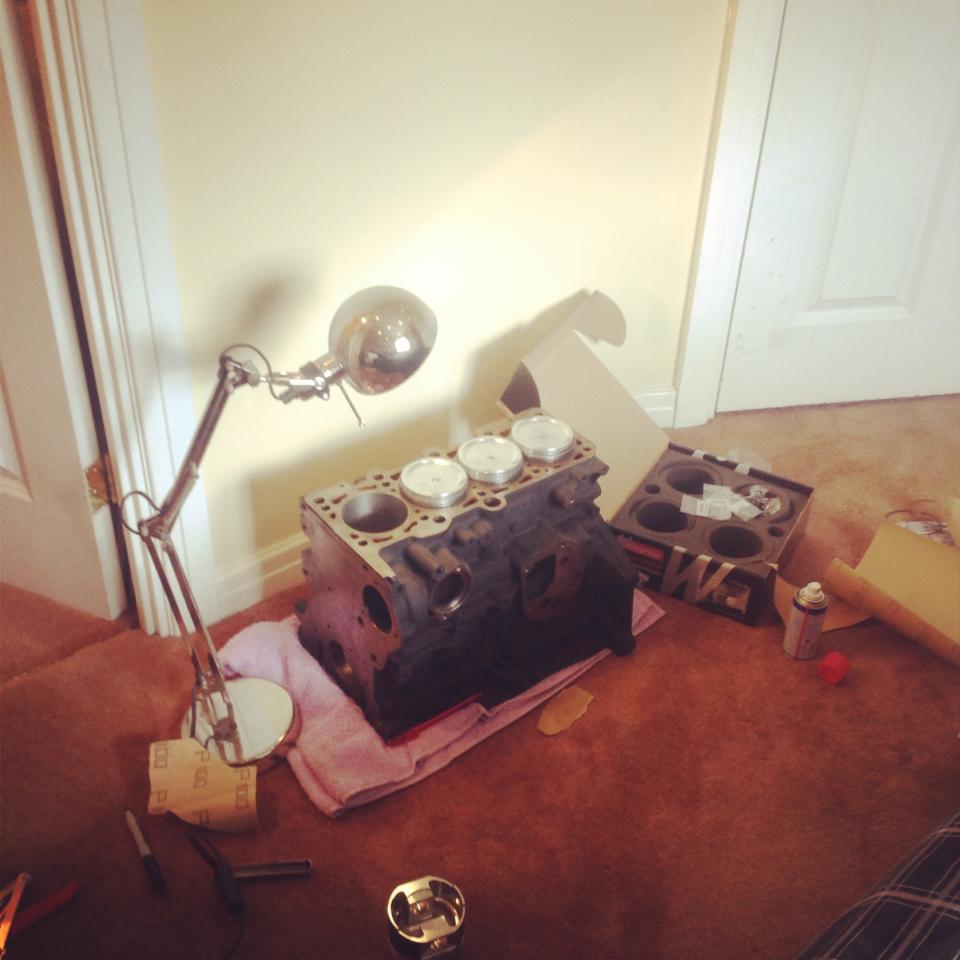
Ready for new mains
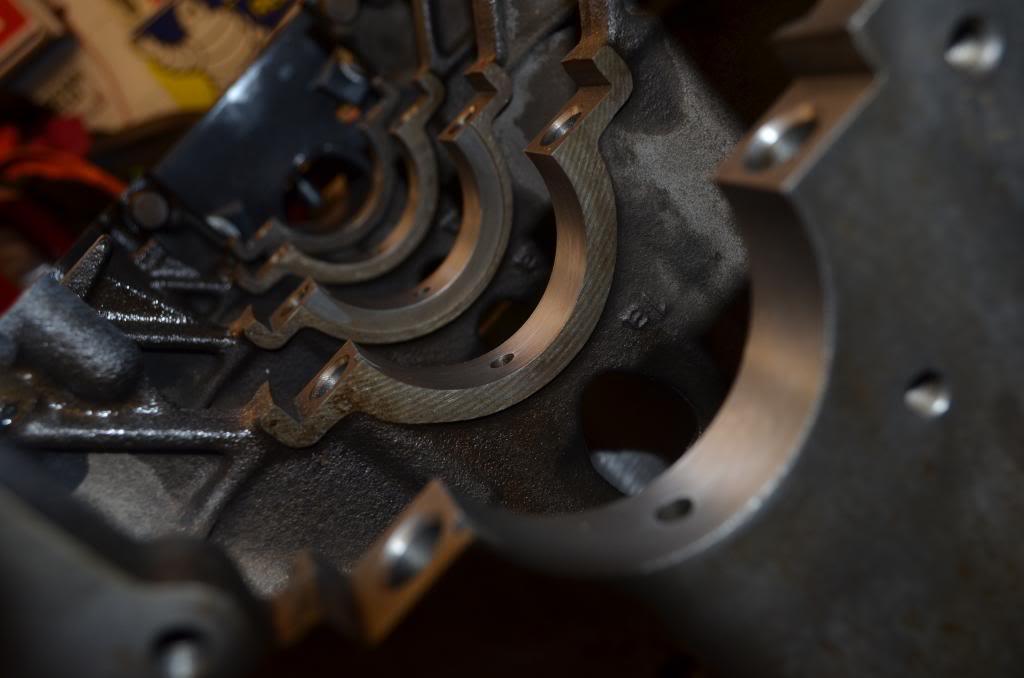
Bearing clearances being checked
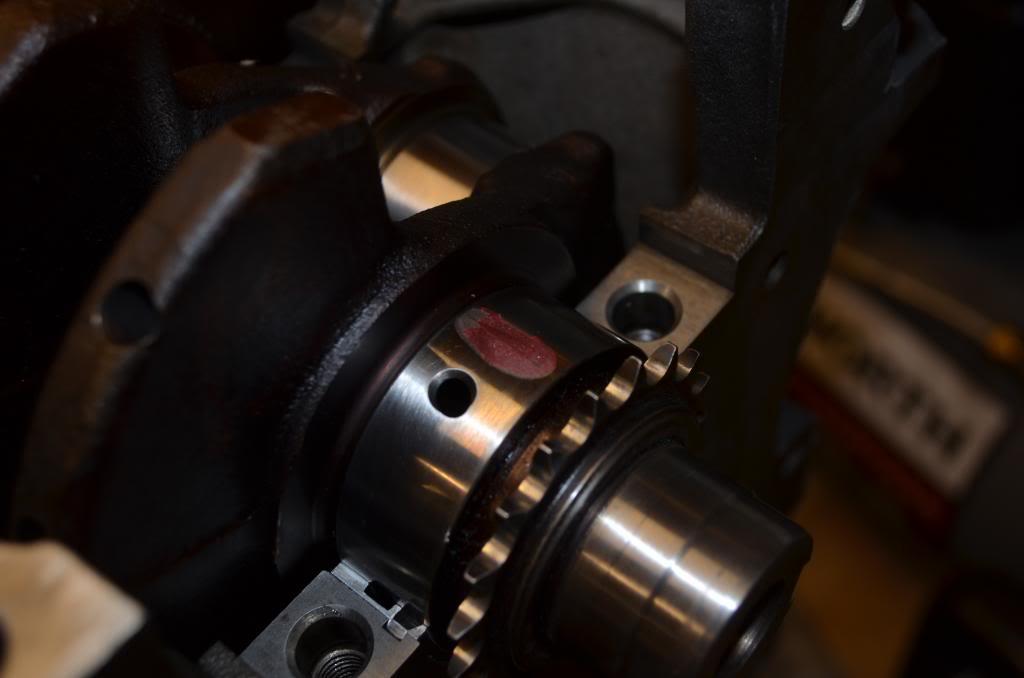
Crank end float checked
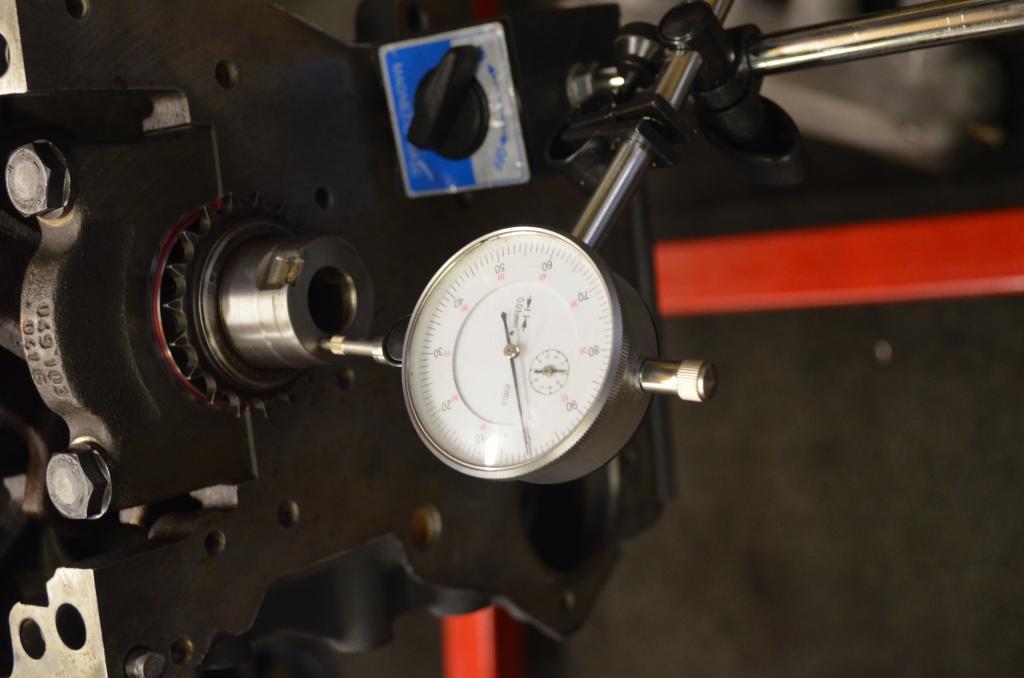
Ready to go in
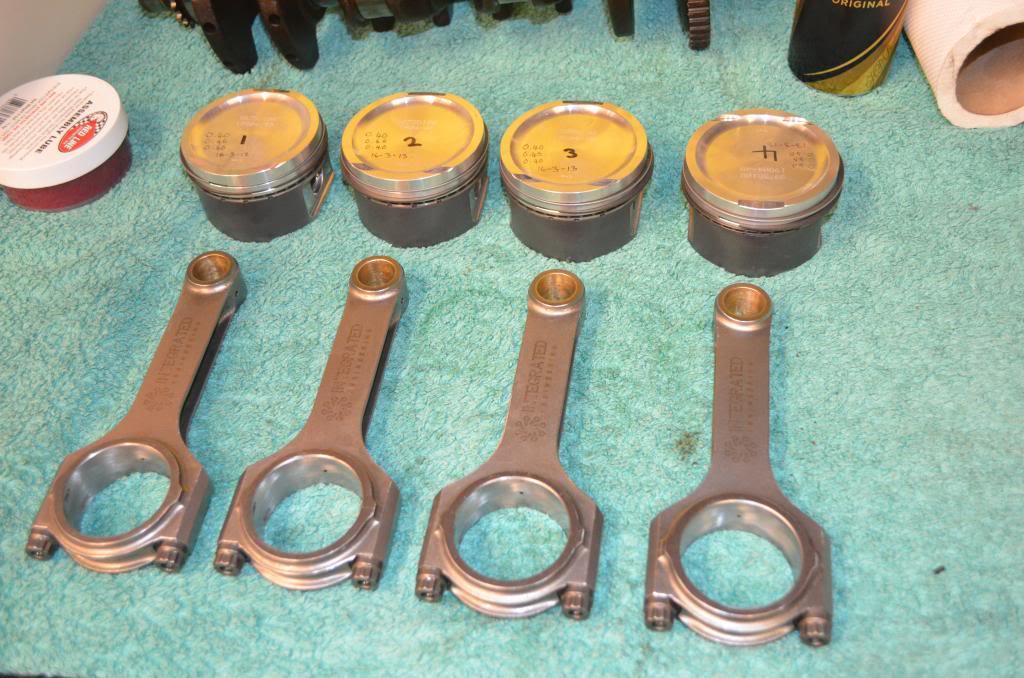
Block painted

And in they go
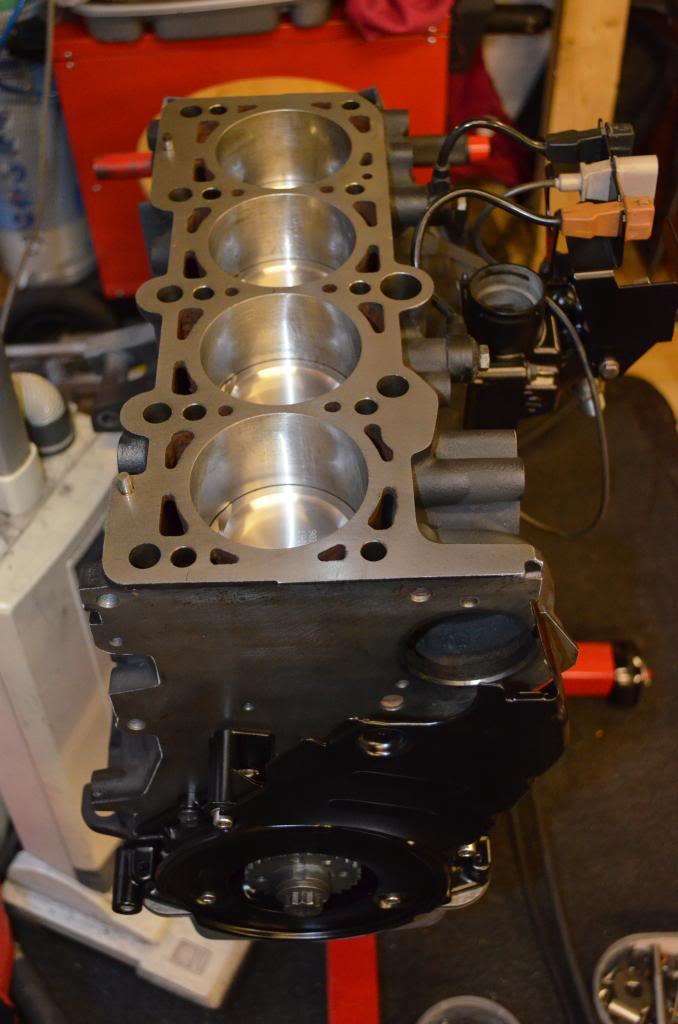
Part 3: Bottom Pulley Peg
With the upgrade valve train going in and the horror stories I’ve seen and heard of the keyway shearing off I decided to peg the bottom pulley to the crank with 2nr 3mm high tensile steel dowels.
2.9mm drill bit, 3mm reamer and dowels
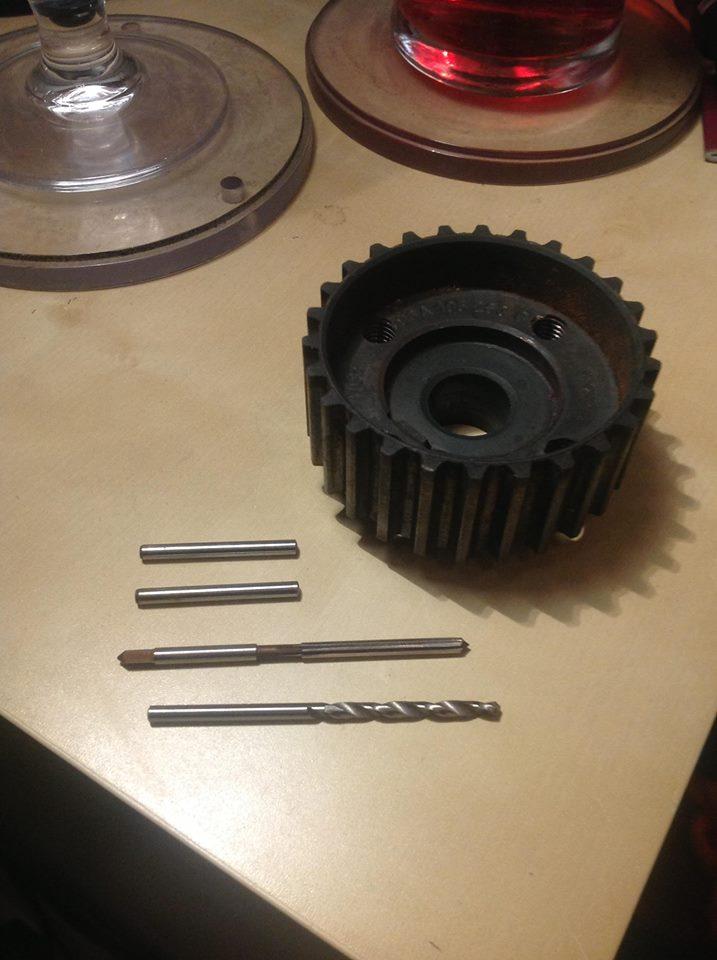
Preparing the pulley
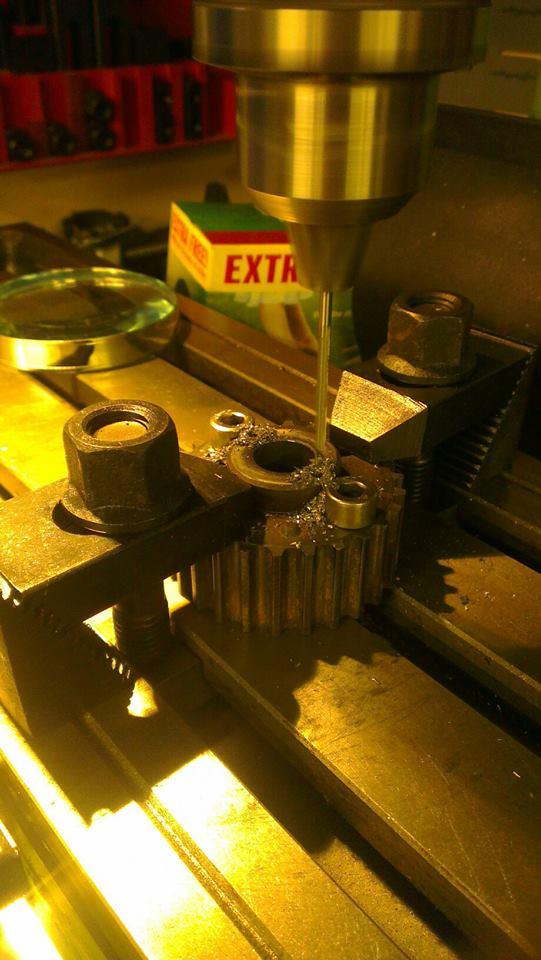
Dowels into crank
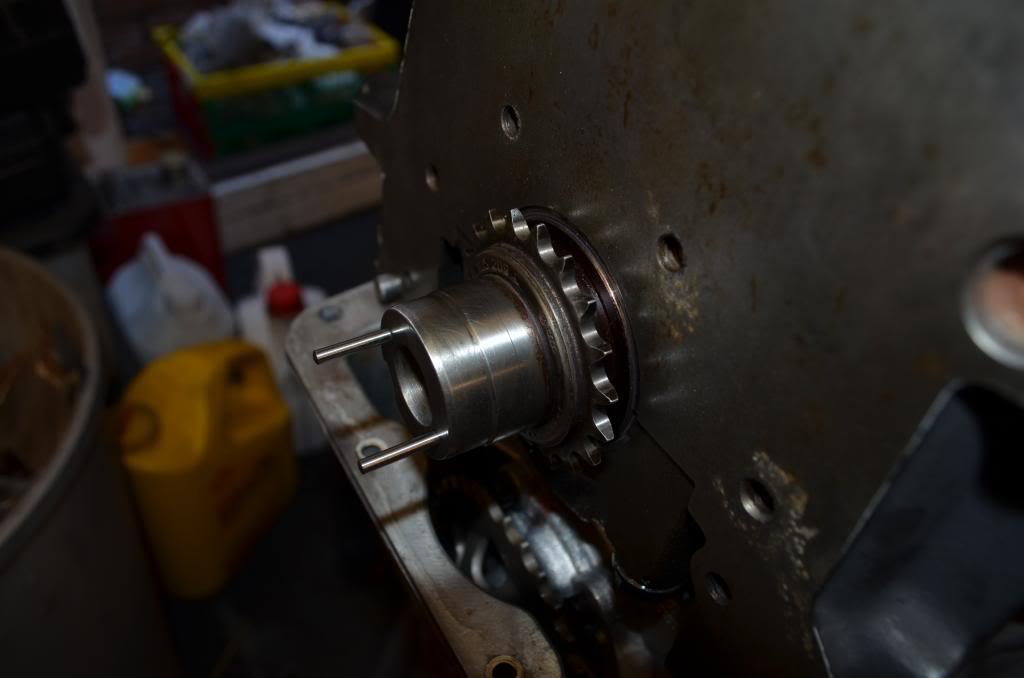
Finished up with the new OEM stretch bolt
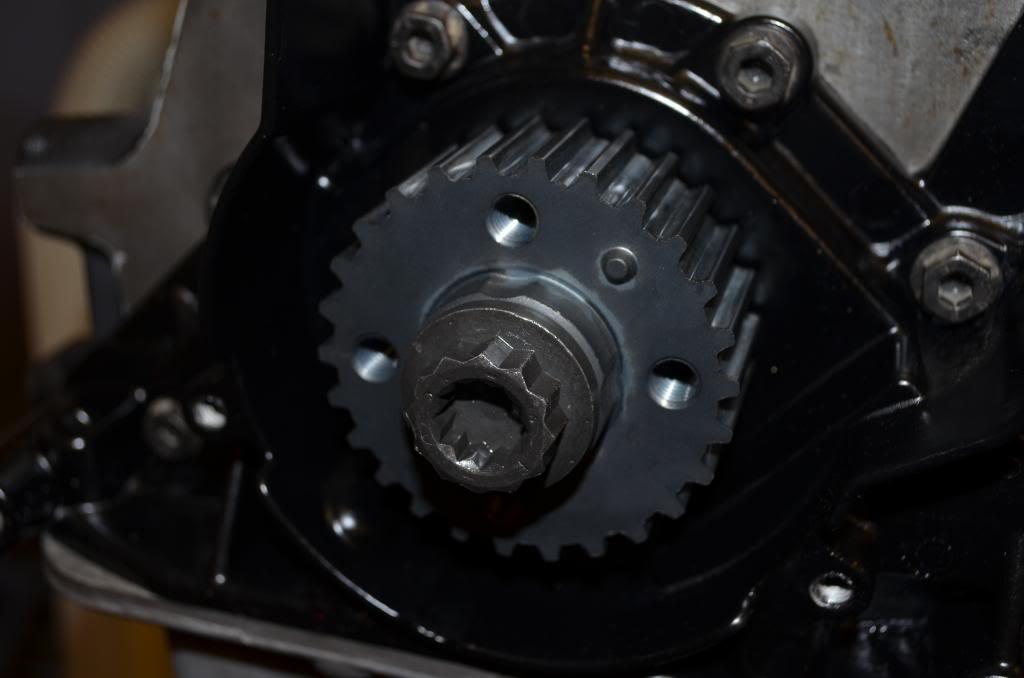
Pulley and new OEM oil pump, chain and tensioner fitted.
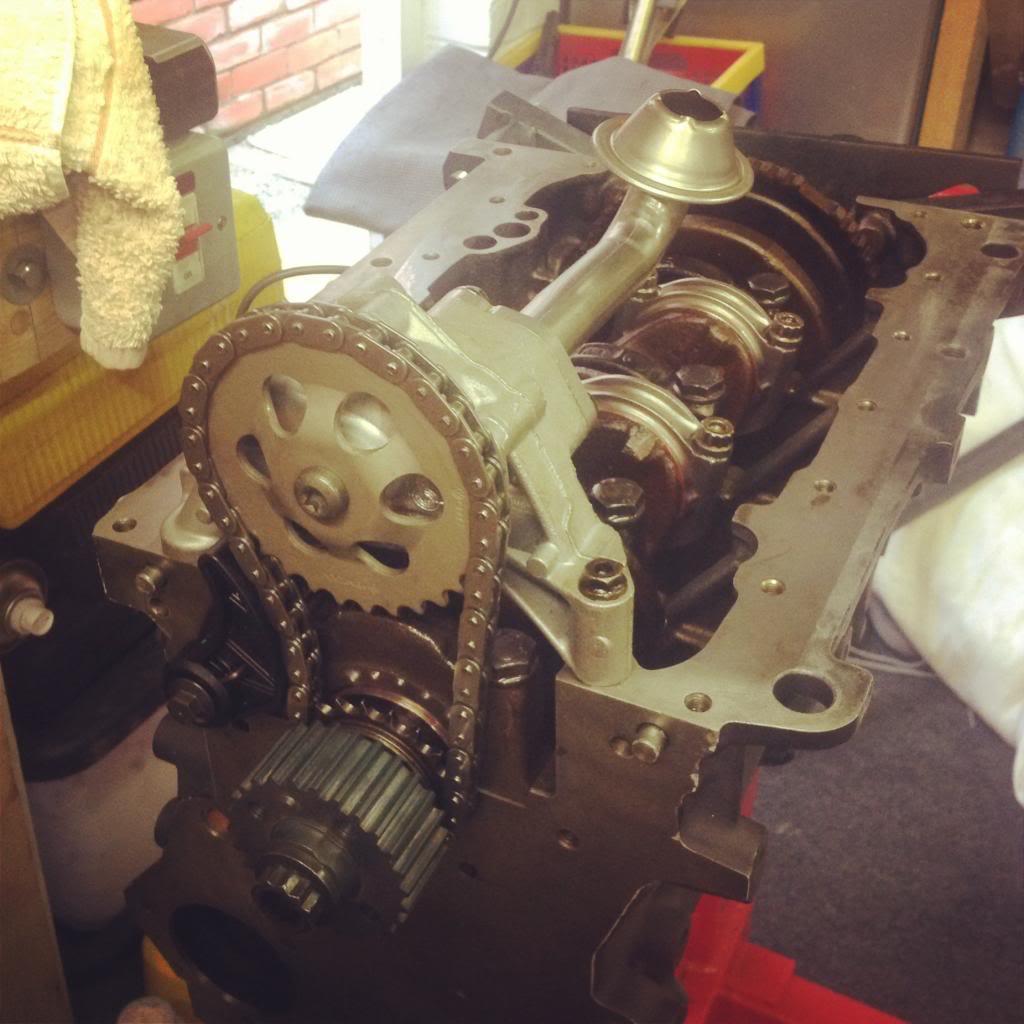
Part 4: Cylinder Head Porting & Rebuild
With the head fully stripped I decided that I would give porting it a go. Having built, tuned and raced 2 stroke bikes in the past some of the techniques and principles were transferable. If it turns out to be no good it’s not the end of the world but without trial and error there will be no further development!
Before setting to work I decided to quickly knock up a stand to allow me to work on the head easier.
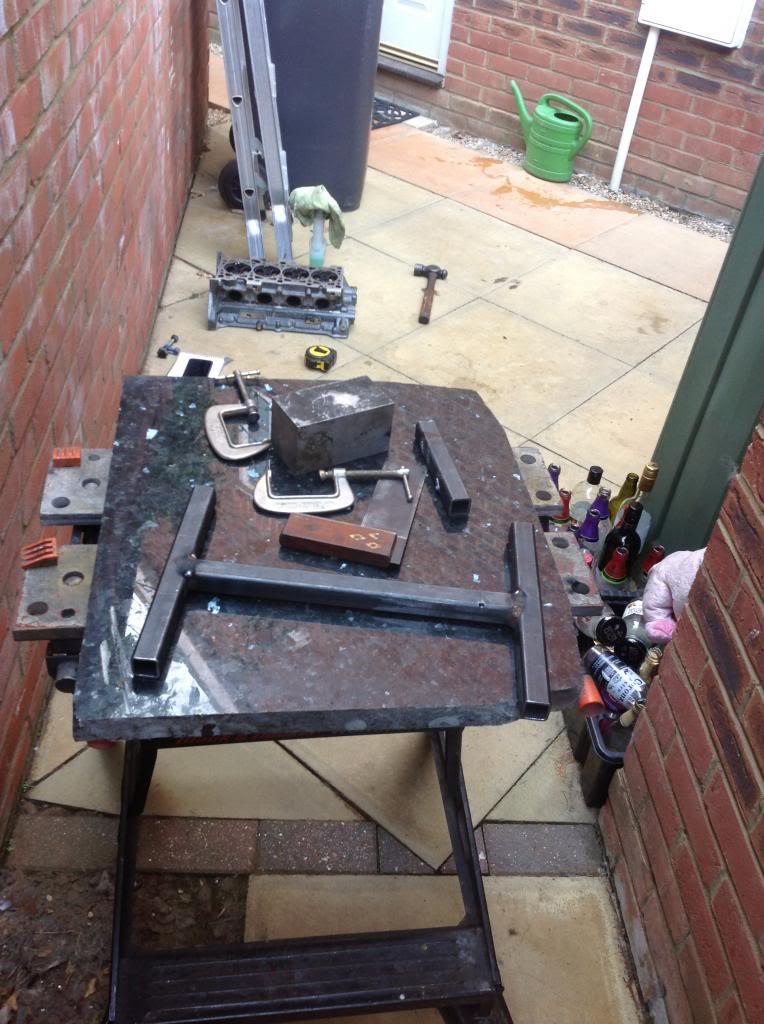
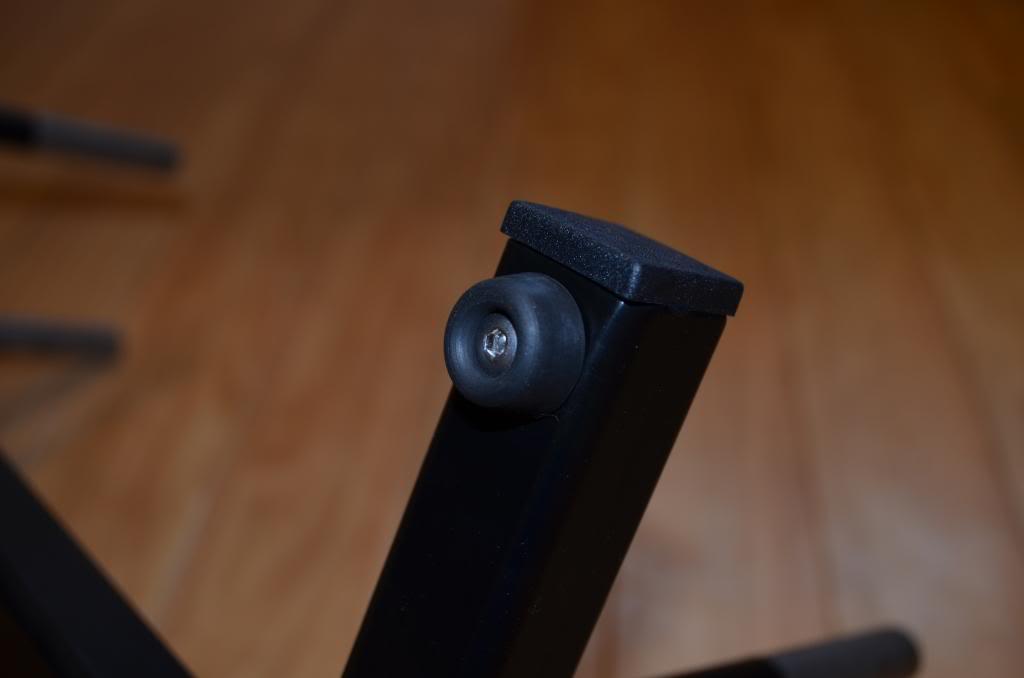
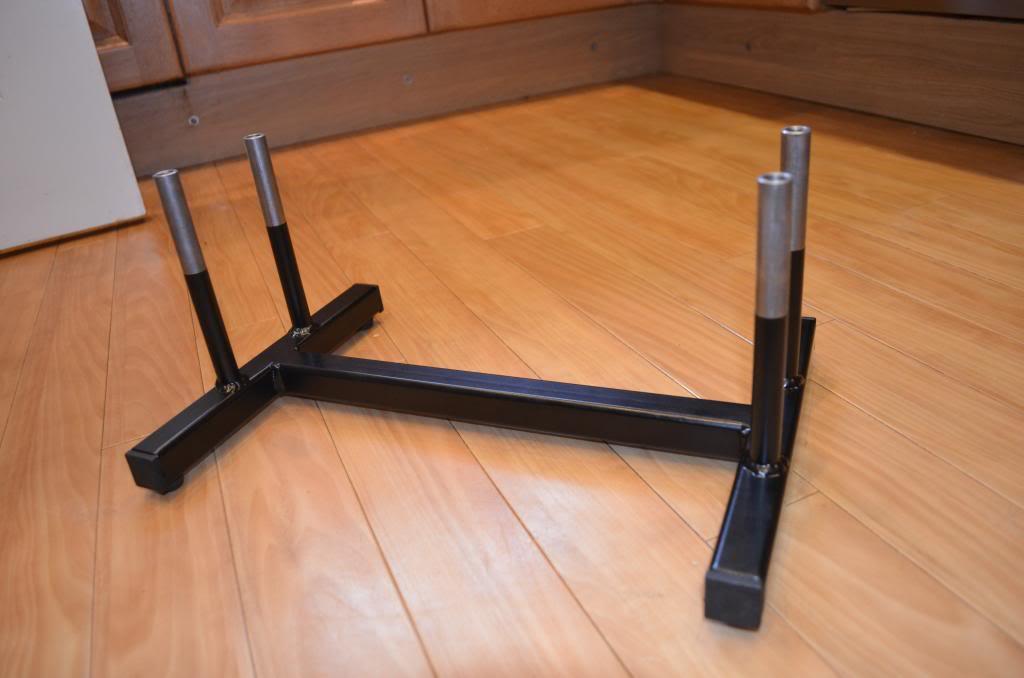
Exhaust port, before and after
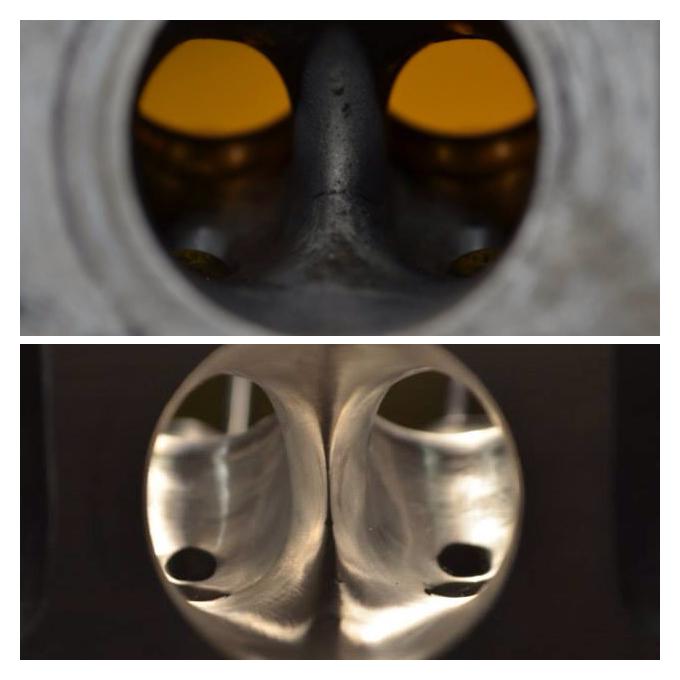
Inlets again before and after

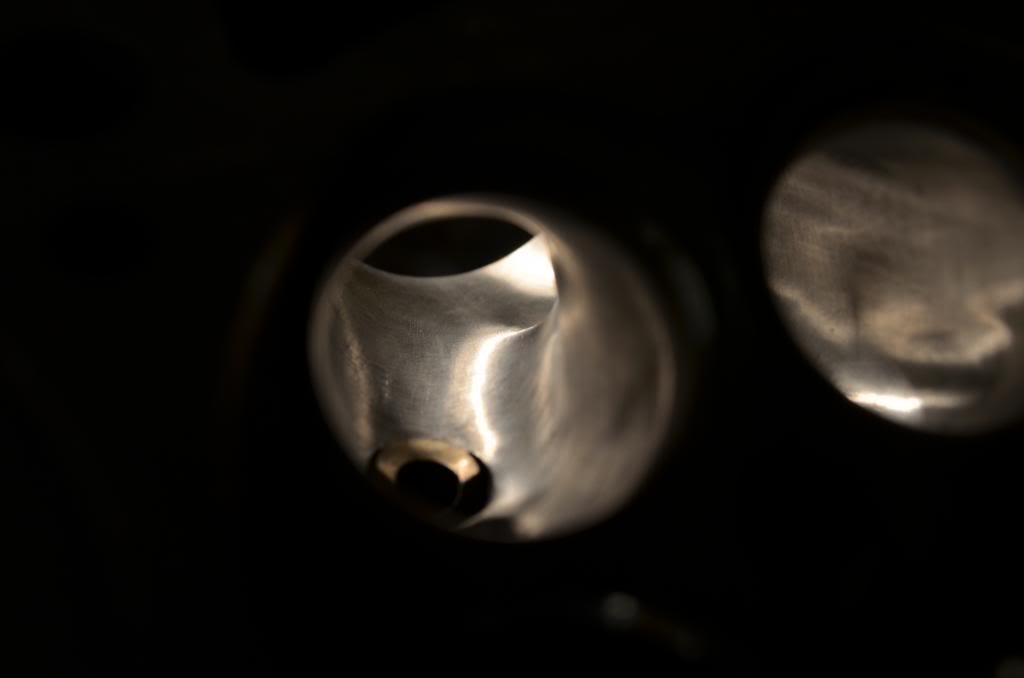
Made a quick and easy valve stand to keep them in their corresponding positions
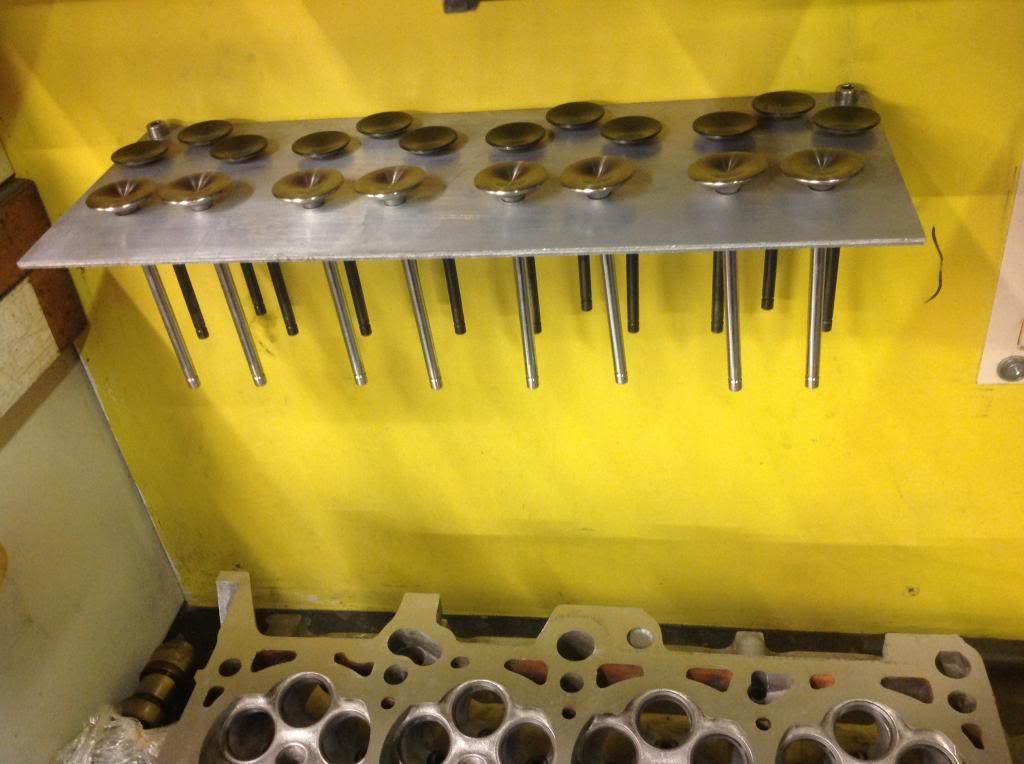
And turned up a tool to help with the installation of the stem seals
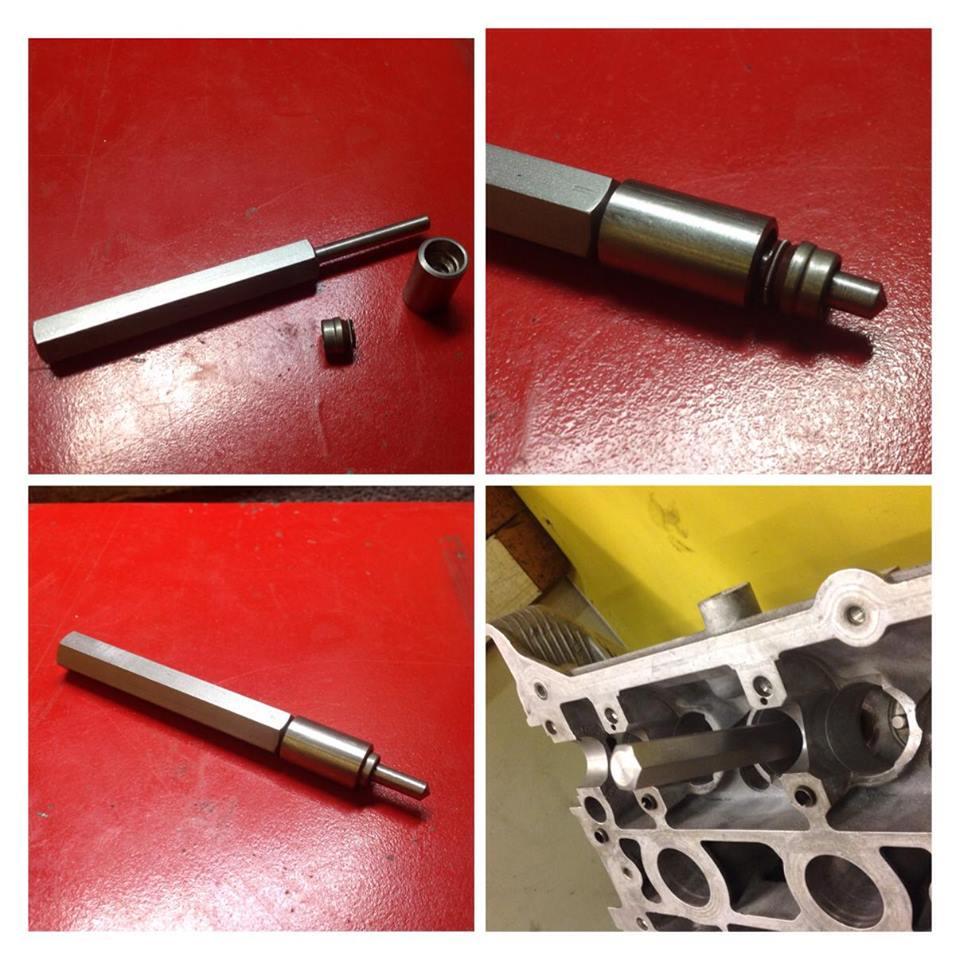
Ready to go!
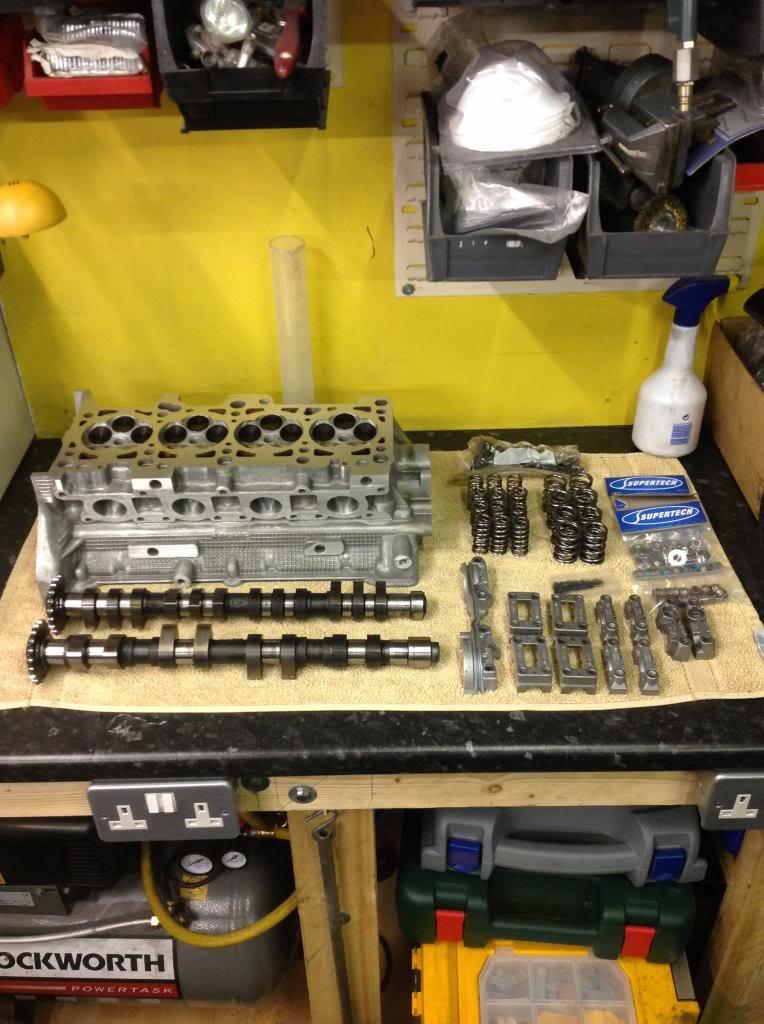
All finished
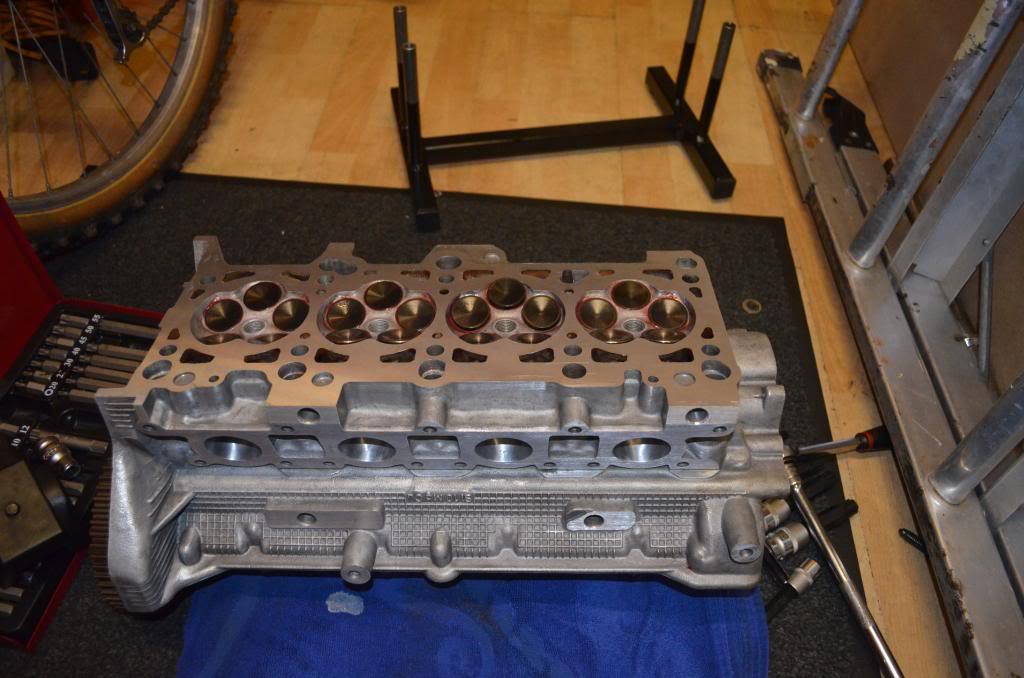
Part 5: Engine Assembly
Fully built
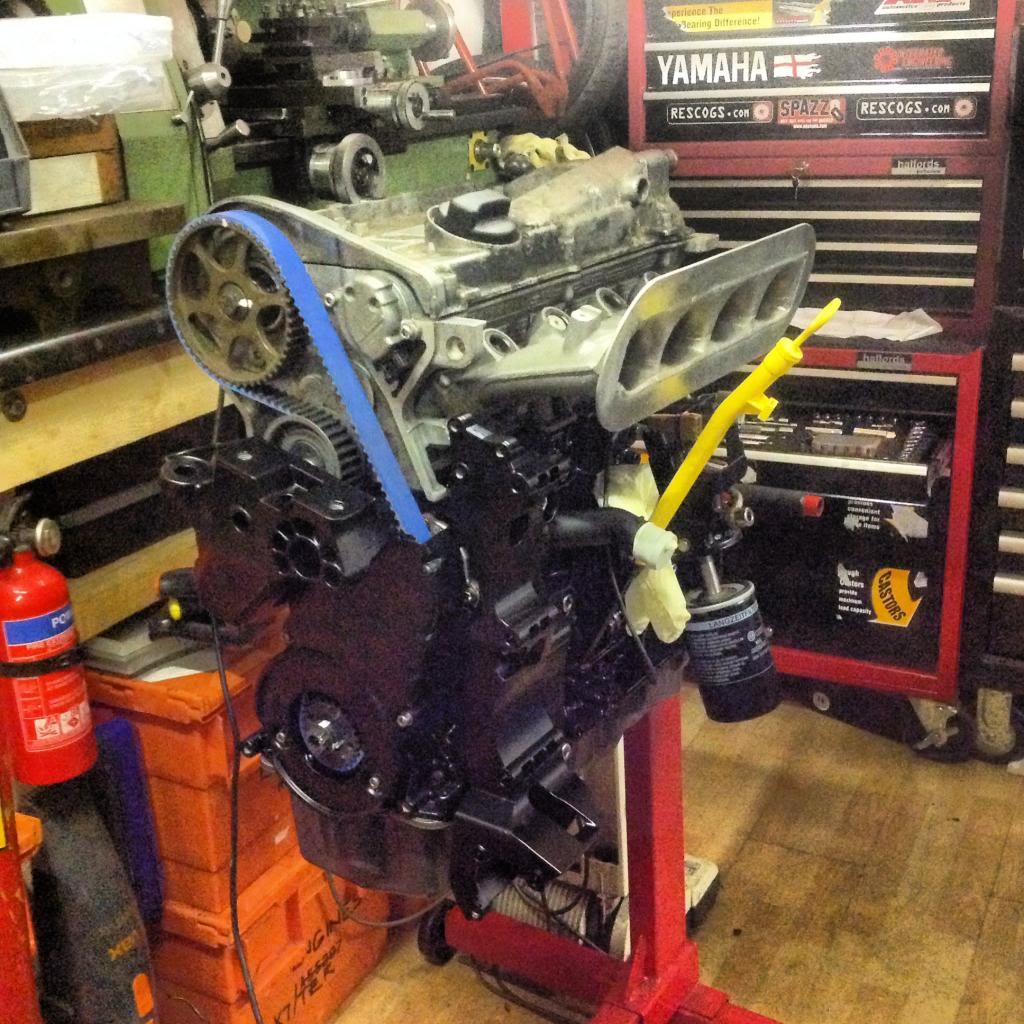
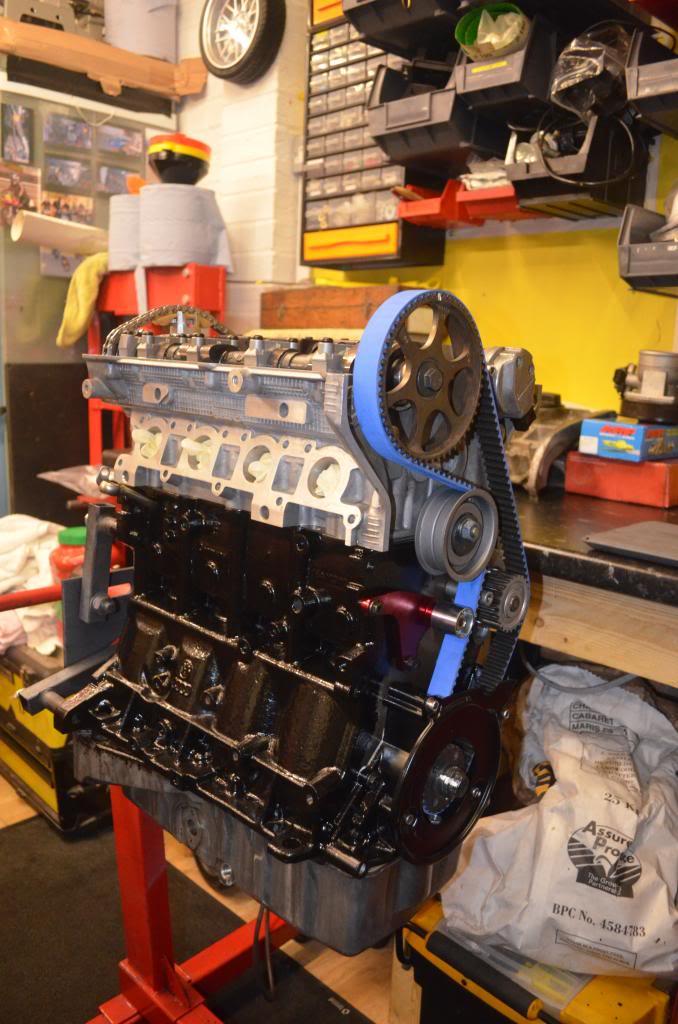
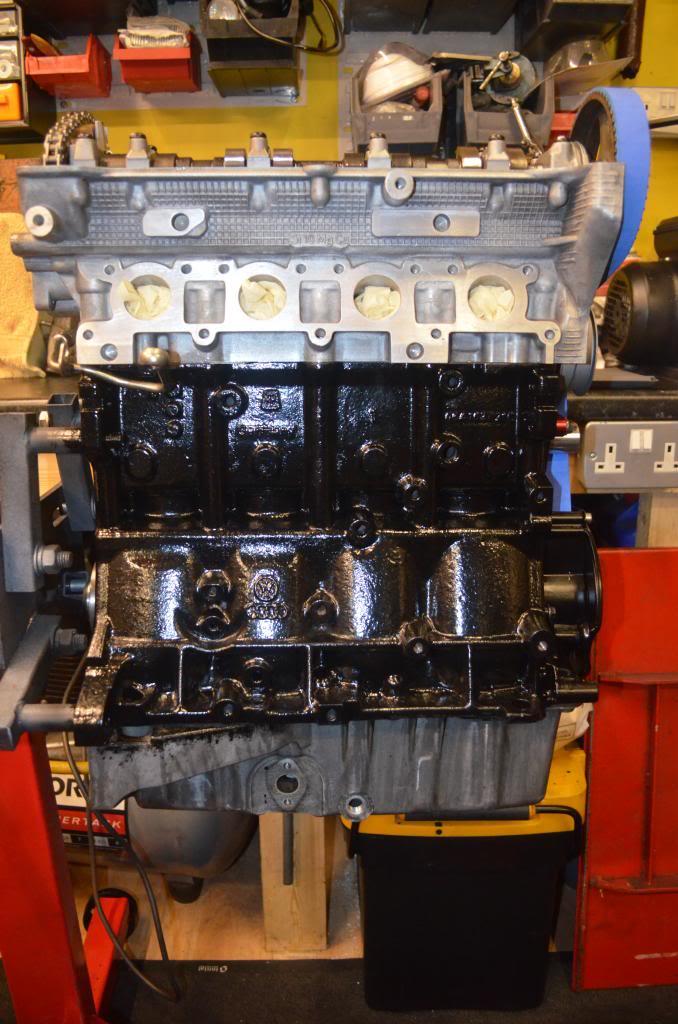
Part 6: Fuel Rail
Had a spare few hours one evening and some left over stock from a previous project so knocked up a new fuel rail.
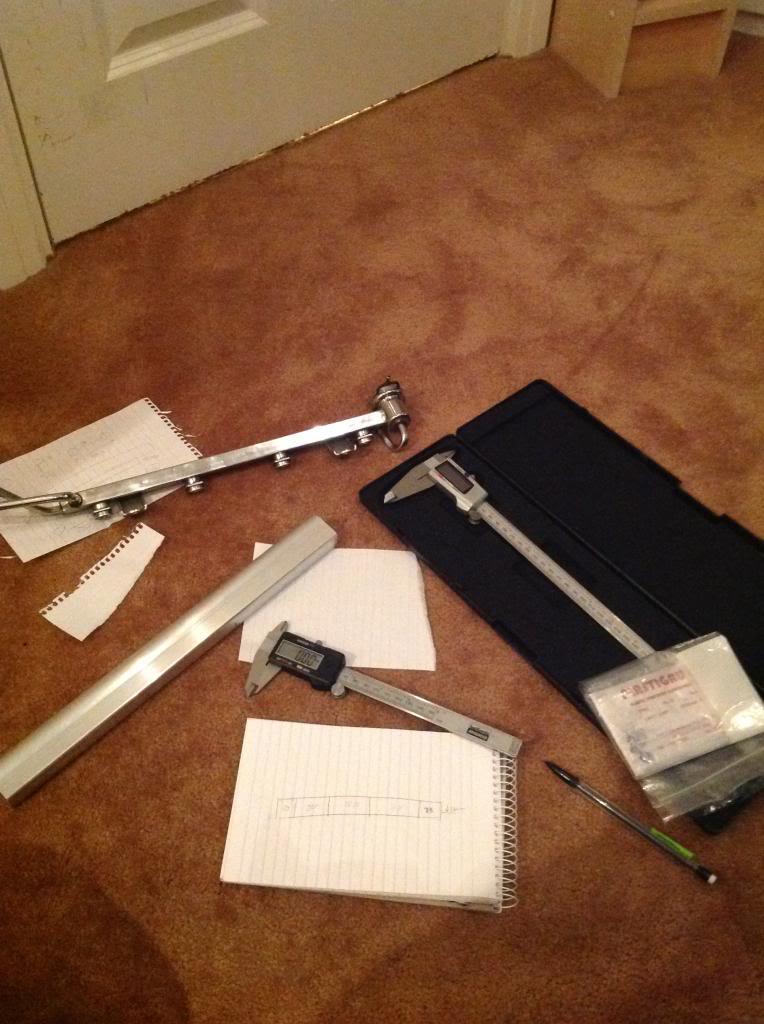
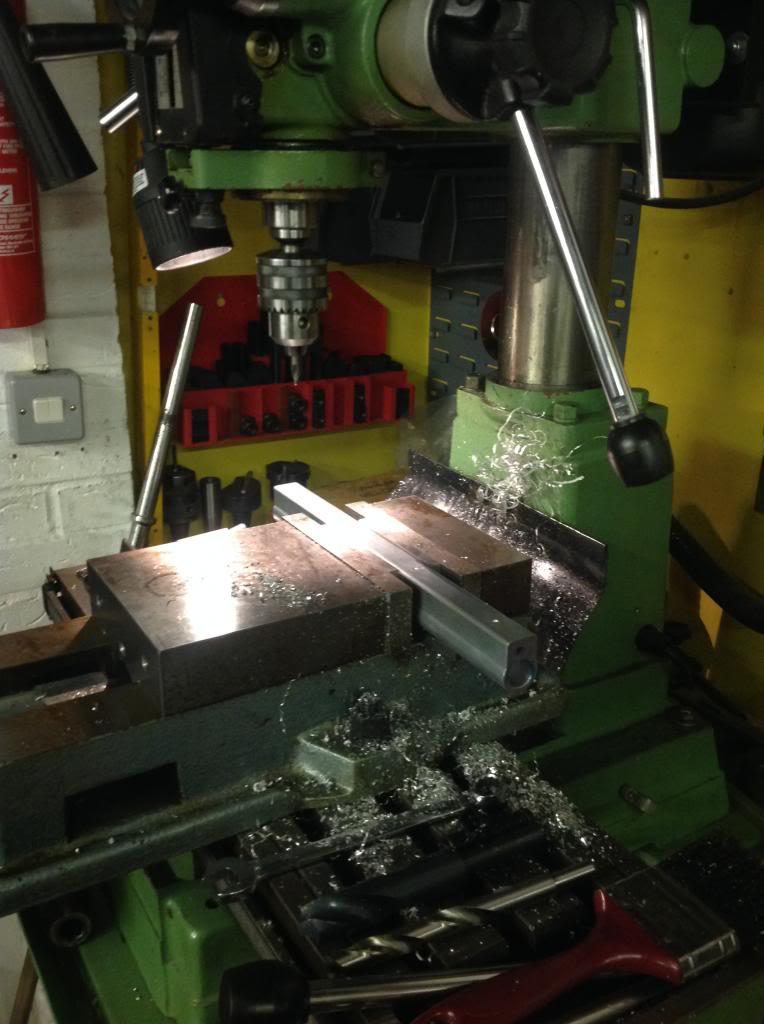
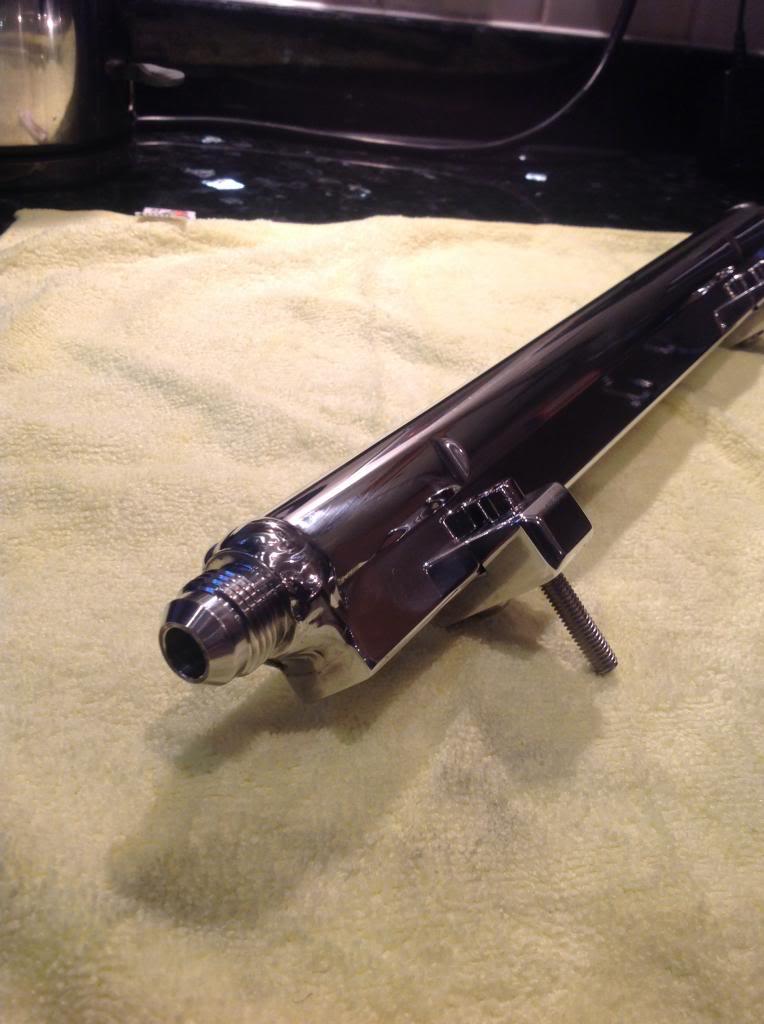
Made a start on a new intake plenum, still trying to work out exactly what I want to do with this so I’ve shelved it for the time being. A friend of a friend done the welding so I cant take any credit for that work. He’s done a brilliant job considering the materials involved.
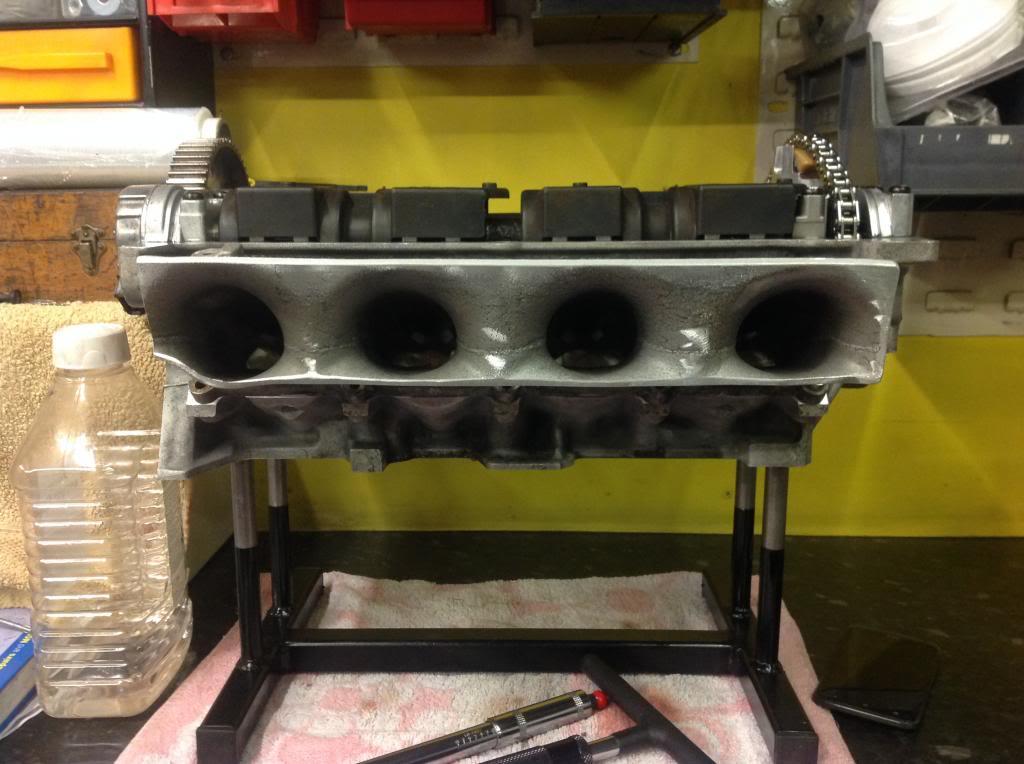
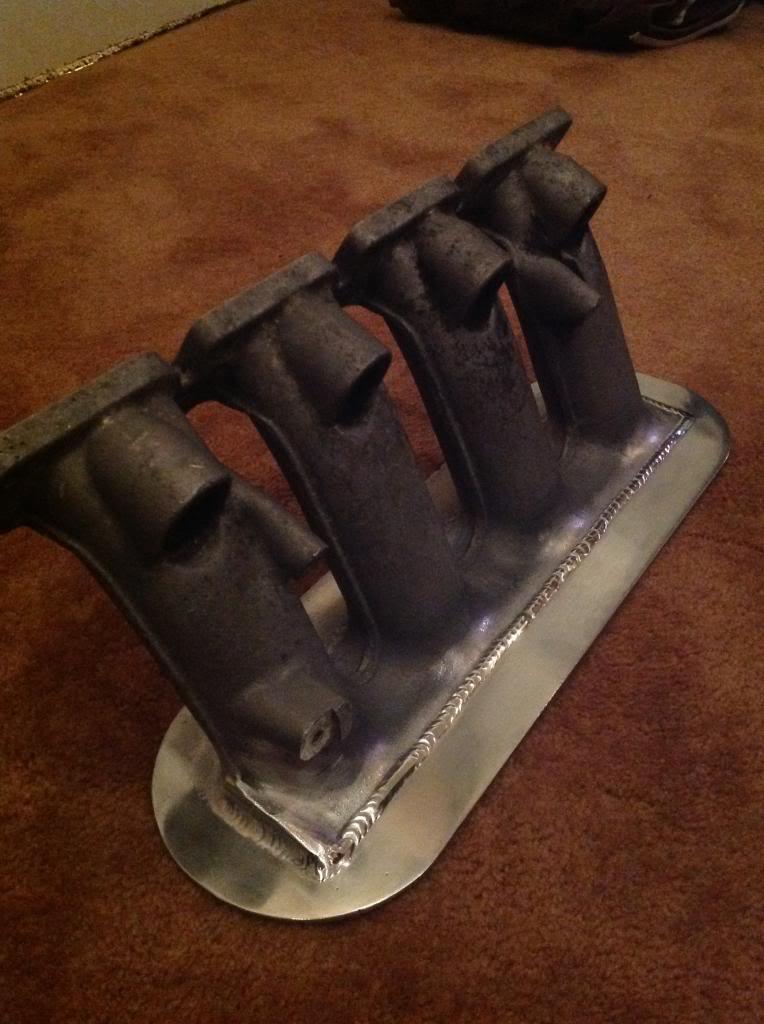
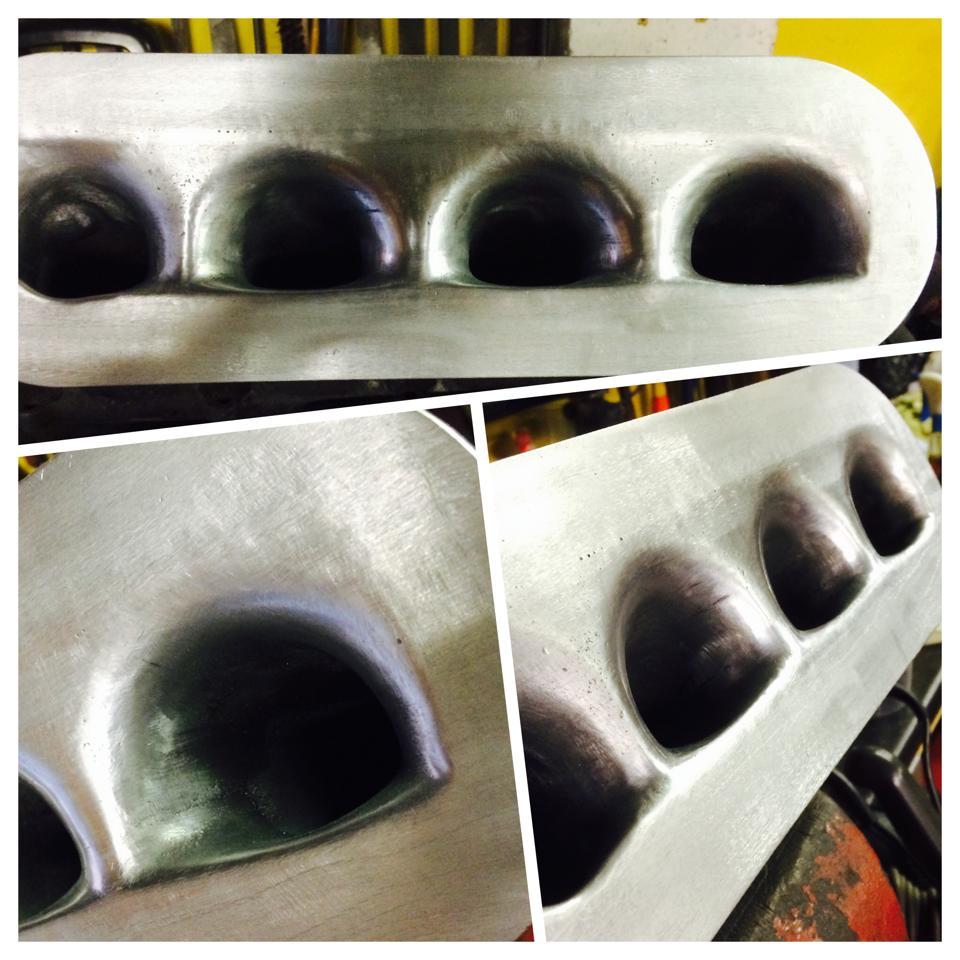
Part 7: The Haldex running gear jig
With the intention of utilising the running gear from an Audi TT I decided the easiest way to transfer the mounting points would be to create a negative jig and use this to locate the mounts under the mk2 chassis. A friend of mine had bought a TT a couple of years previous and had done nothing with it so decided to sell it to me. £1300 lighter I had a complete car! A very tatty TT but all the running gear was spot on and the 02M 6sp gearbox was also there. I managed to sell on almost everything over the next couple of weeks and pretty much made my money back and kept all the running gear, engine (good spare) and gearbox.
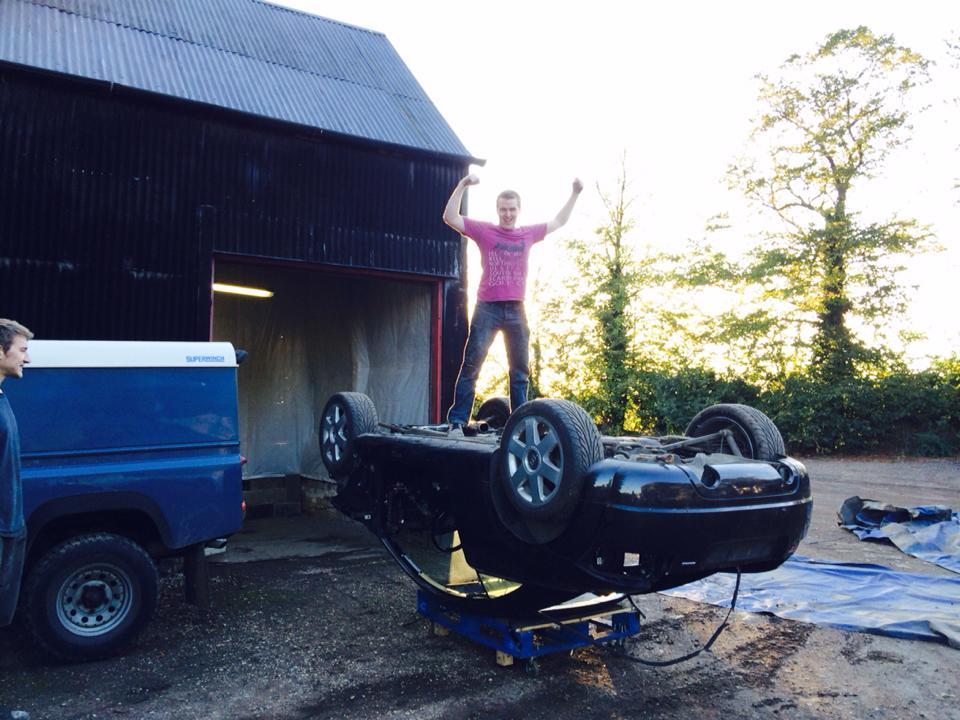
With the TT on its roof I began to start turning and fabricating the necessary parts for the jig
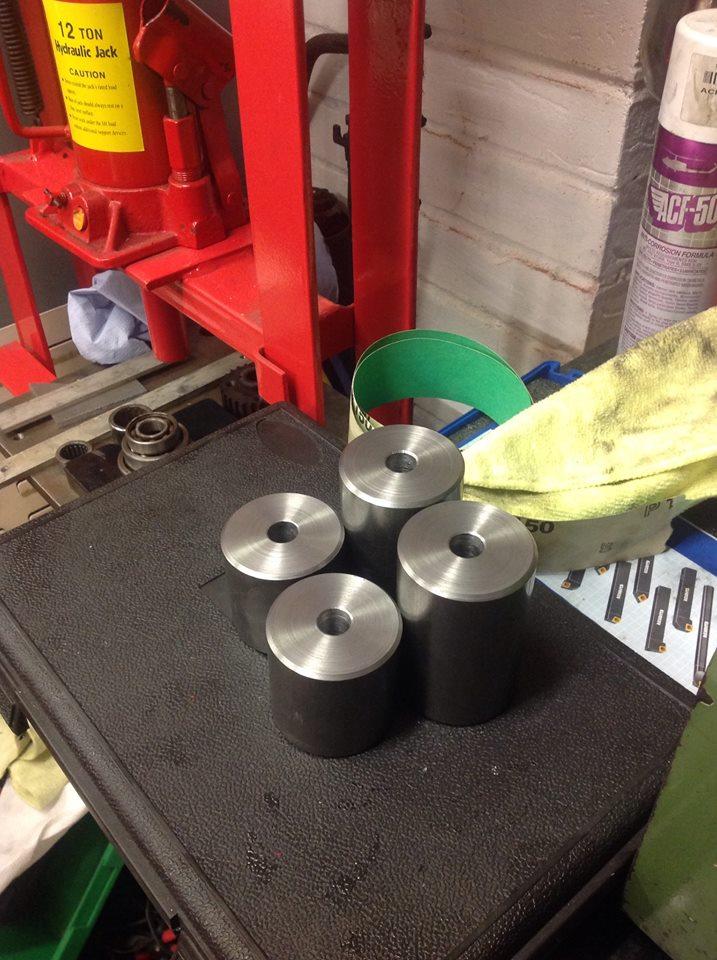
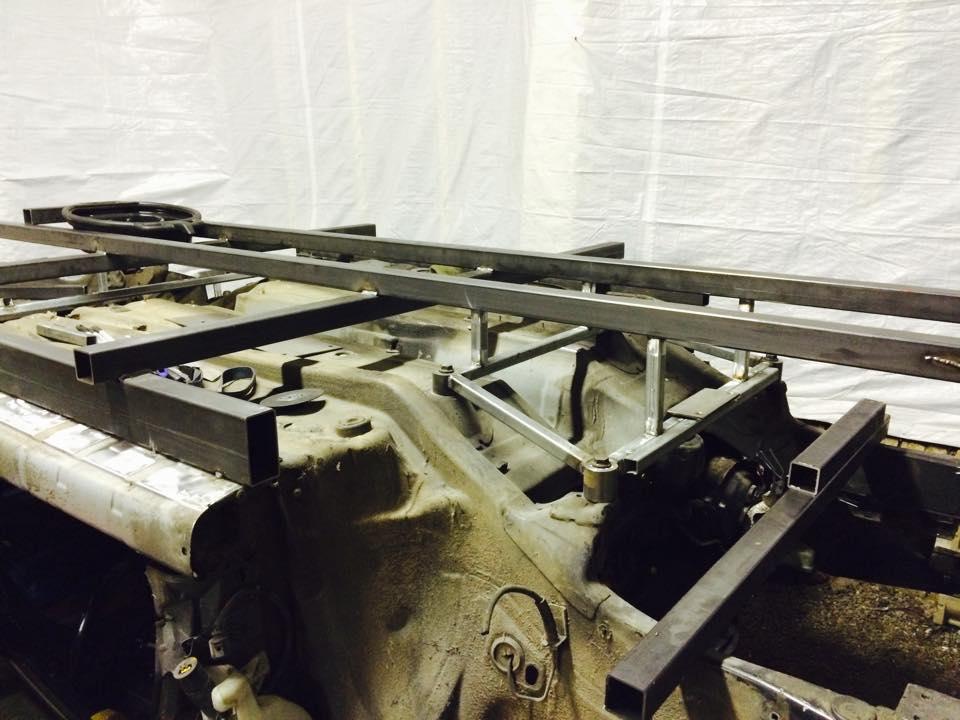
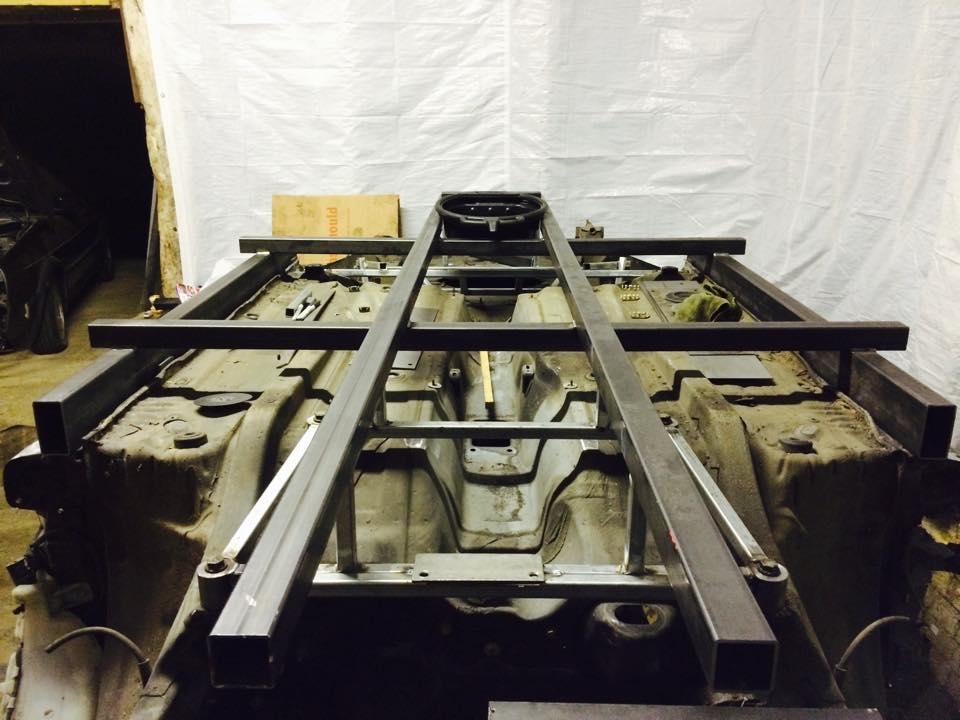
Late night selfie
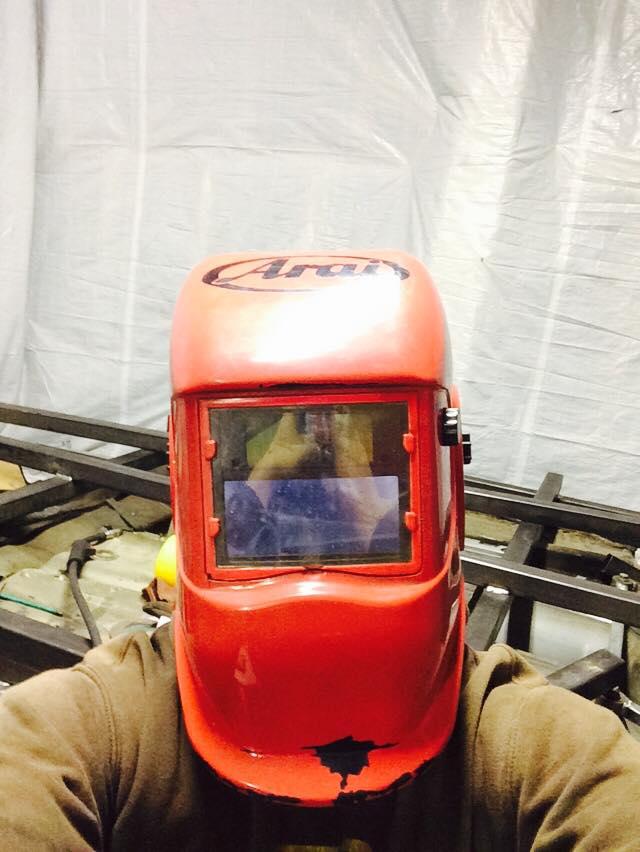
Front turrets position
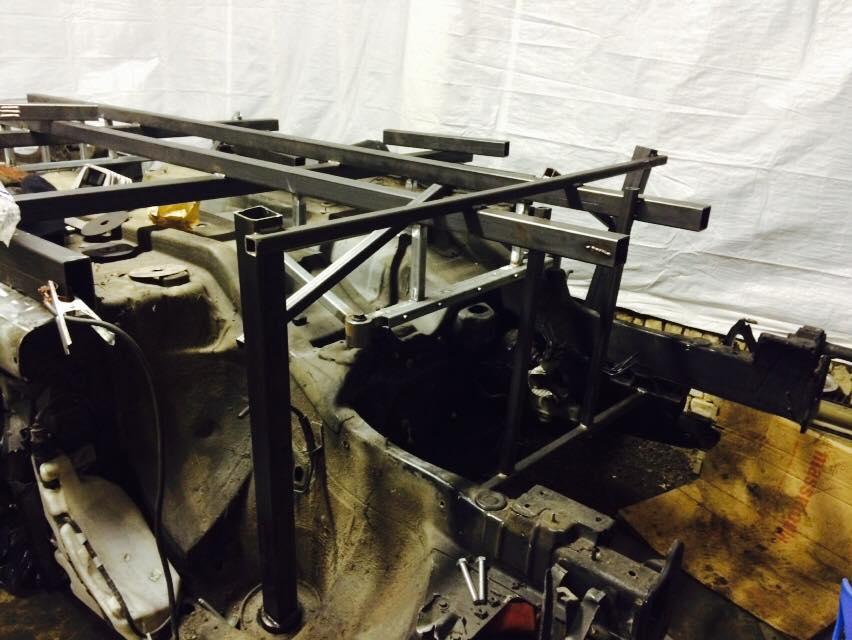
And finished! Ignore what looks like a bit on the piss, that’s a separate jig for the engine mounts.
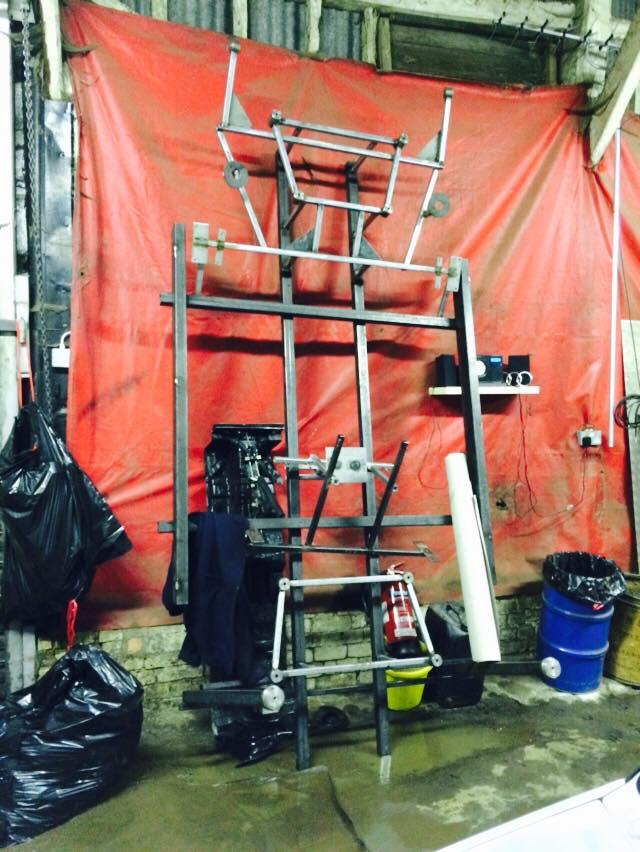
Part 8: The MK2 shell!
With the Haldex jig finished and the TT body shell weighed in for around 50p I searched for a few weeks to find the most solid MK2 shell I could find. This is what I came up with. Apart from the missing doors and wings it really is a good shell. Potentially needs a new scuttle panel if I am being really fussy. I will get some new pics once I’ve steam cleaned it and got it up to my workshop.
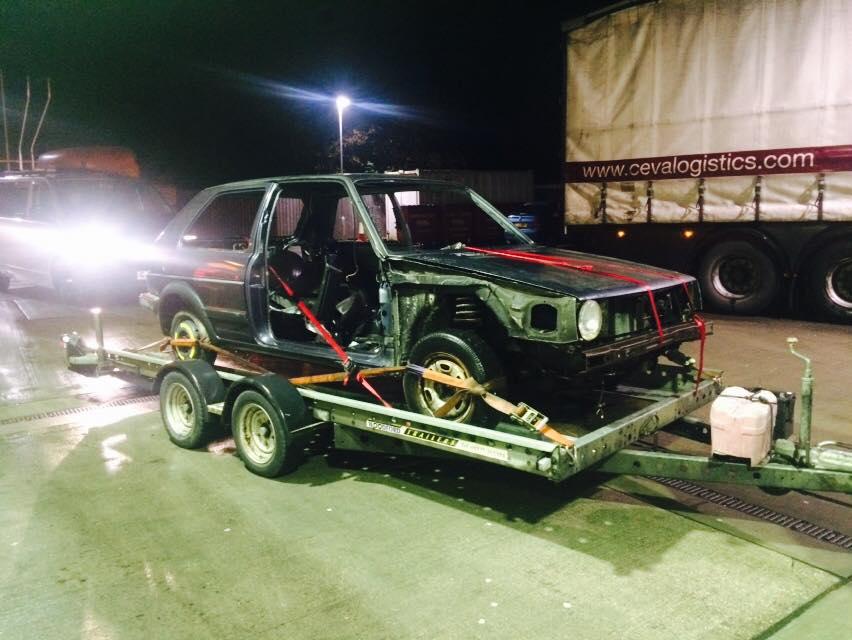
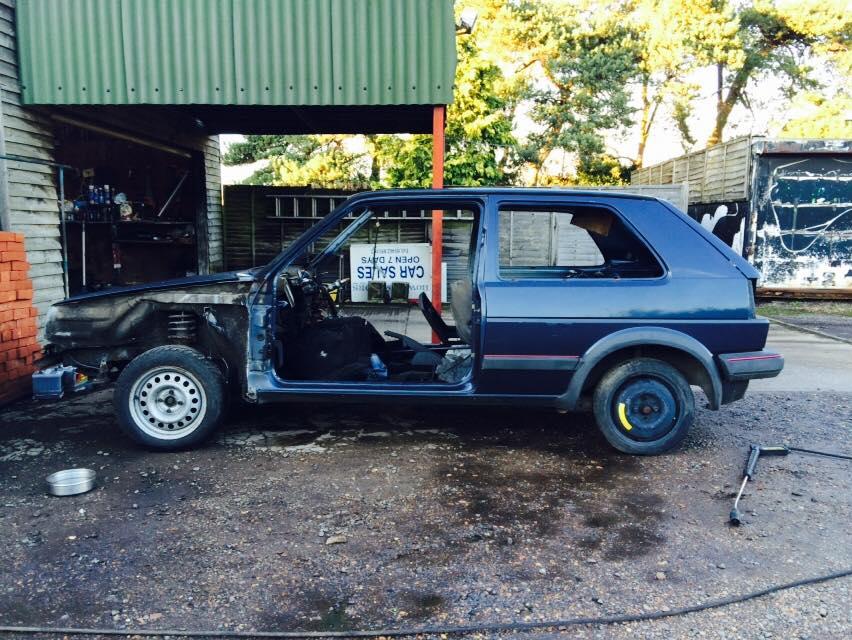
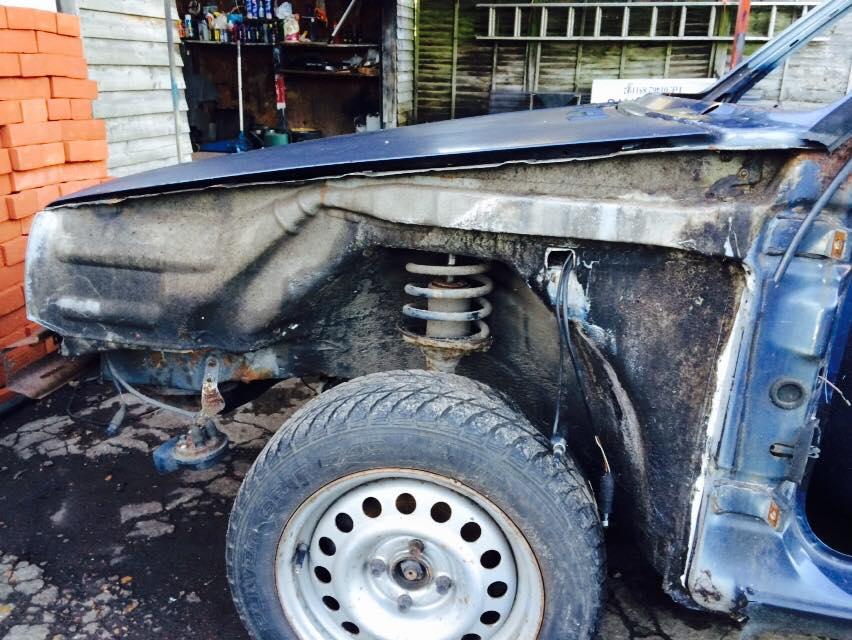
Floors are certainly hole free
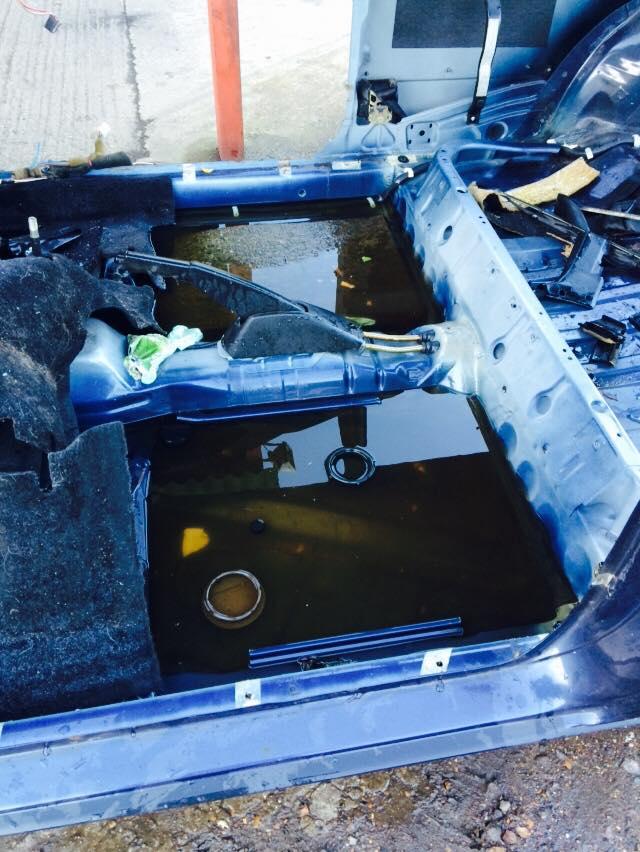
And that is where I am up to! More to come over the next few weeks and months. I’m aiming for ultimate dubs 2016
Update time!
Today I finally got stuck in with stripping what wasn’t already off the shell when I bought it, engine, gearbox, exhaust, heater matrix etc.
Few pics before
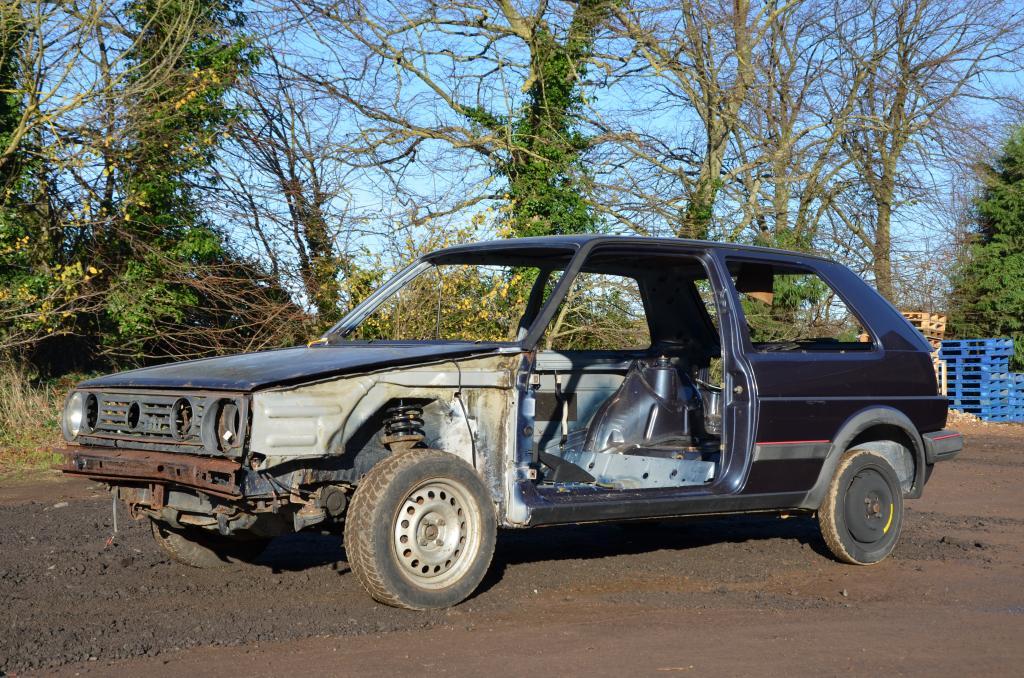
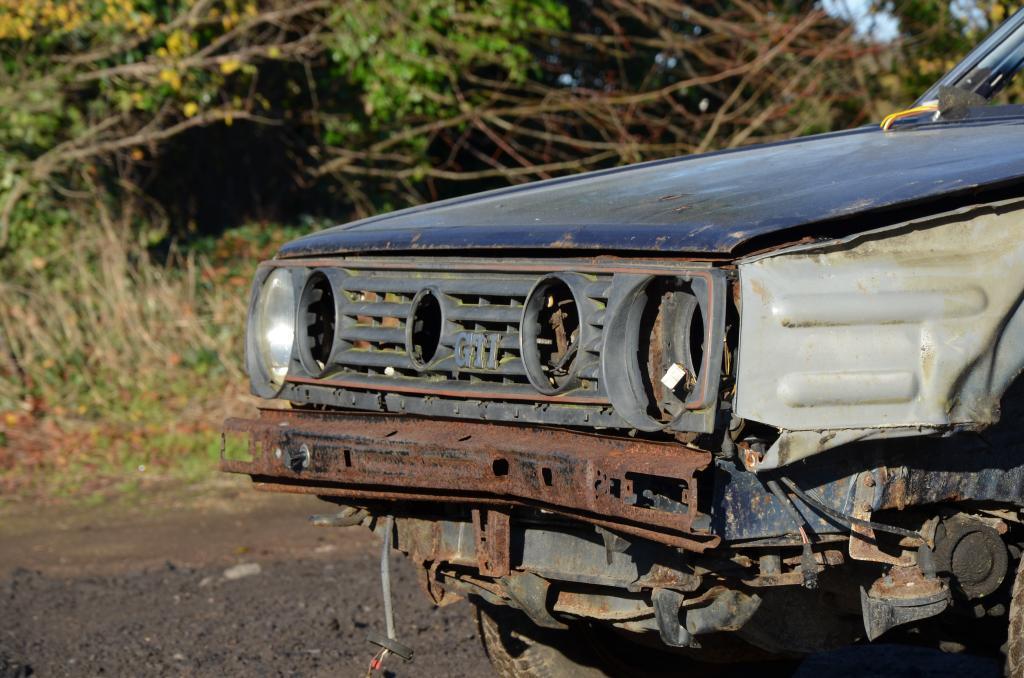
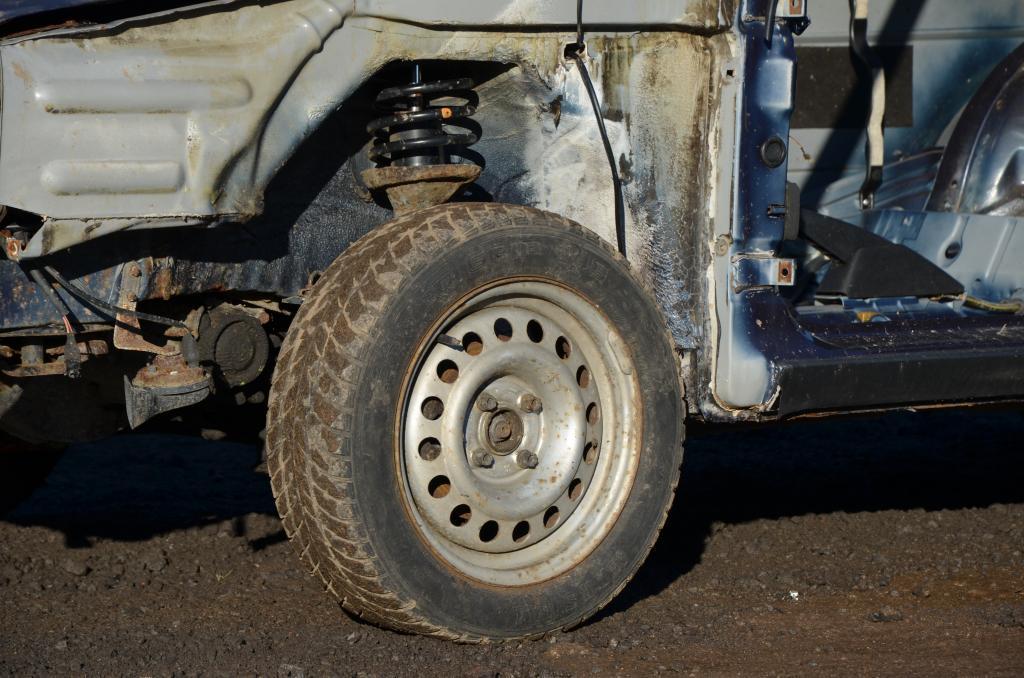
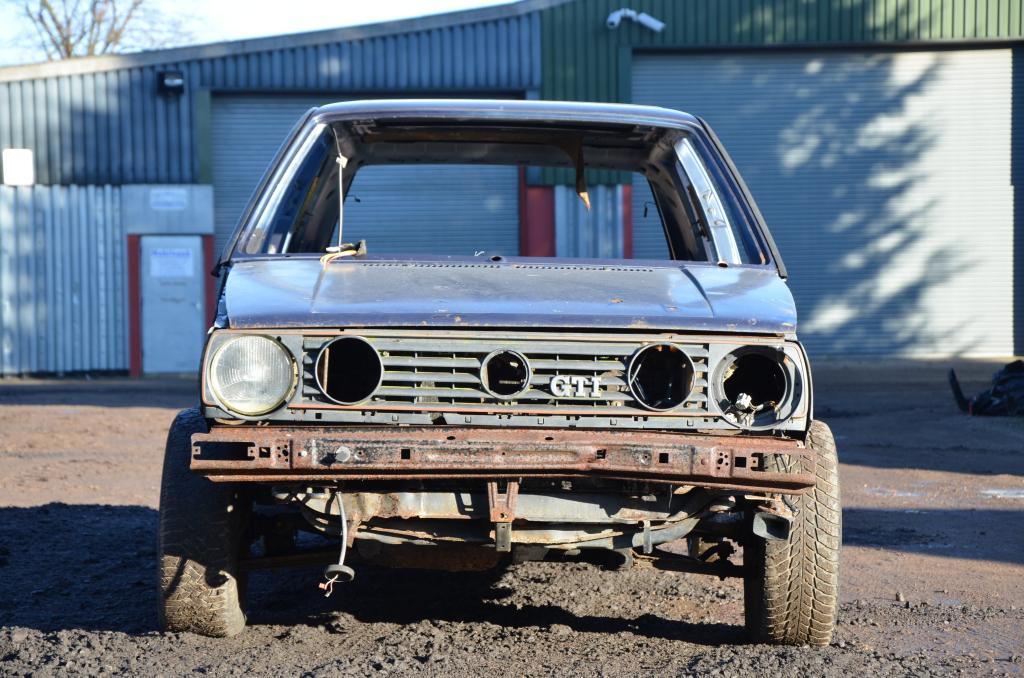
Bonnet has certainly seen better days. Guess it’ll have to be a carbon replacement
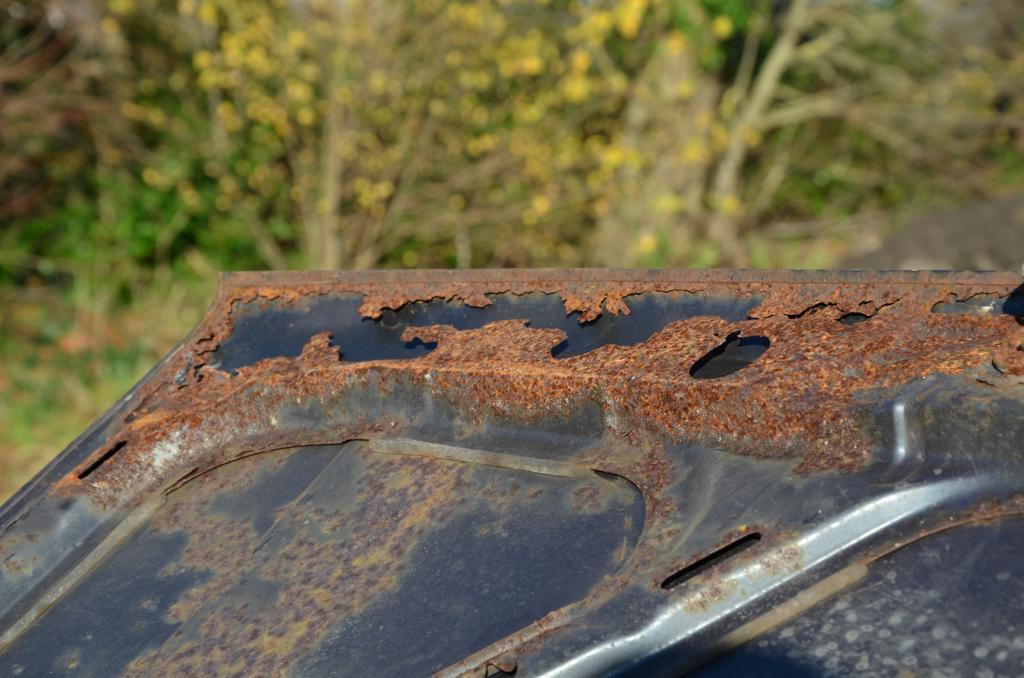
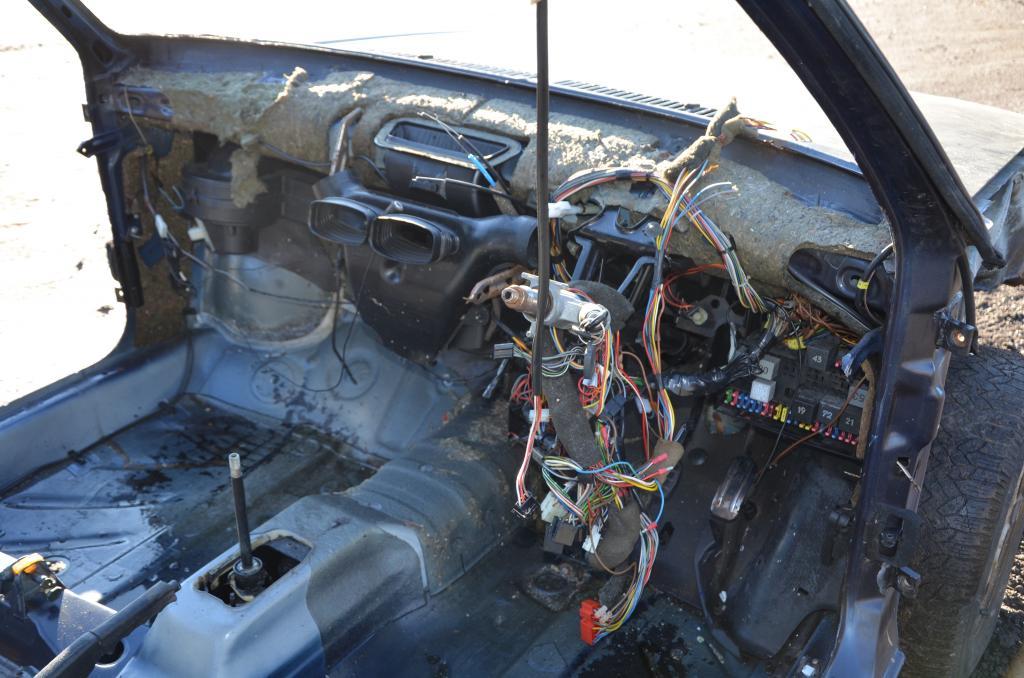
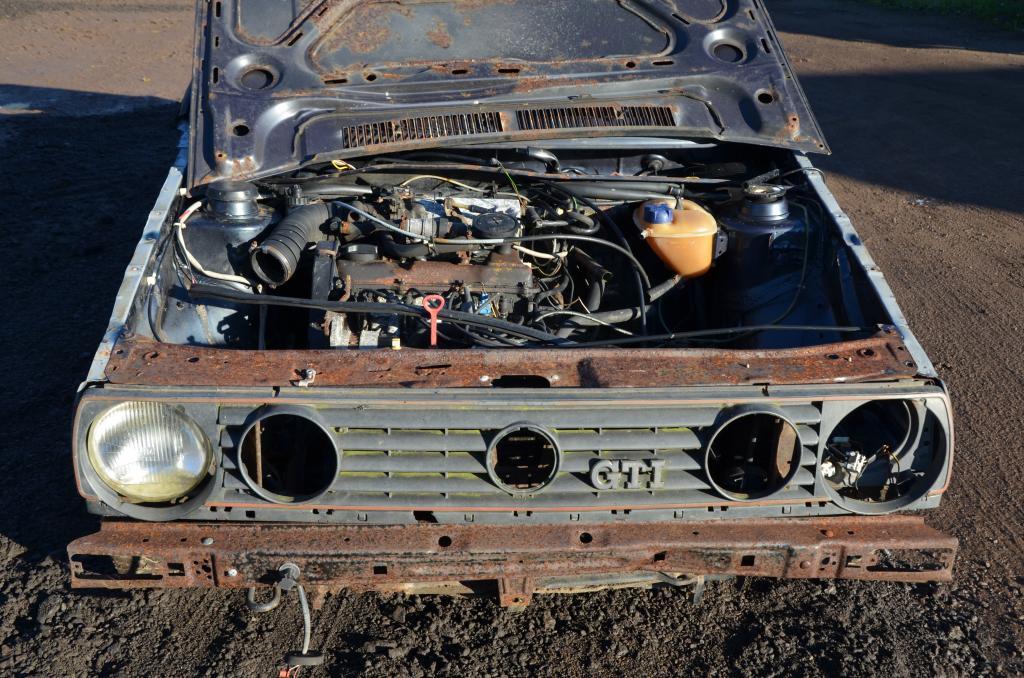
And a few from a couple of hours later. Surprisingly nothing help up a fight
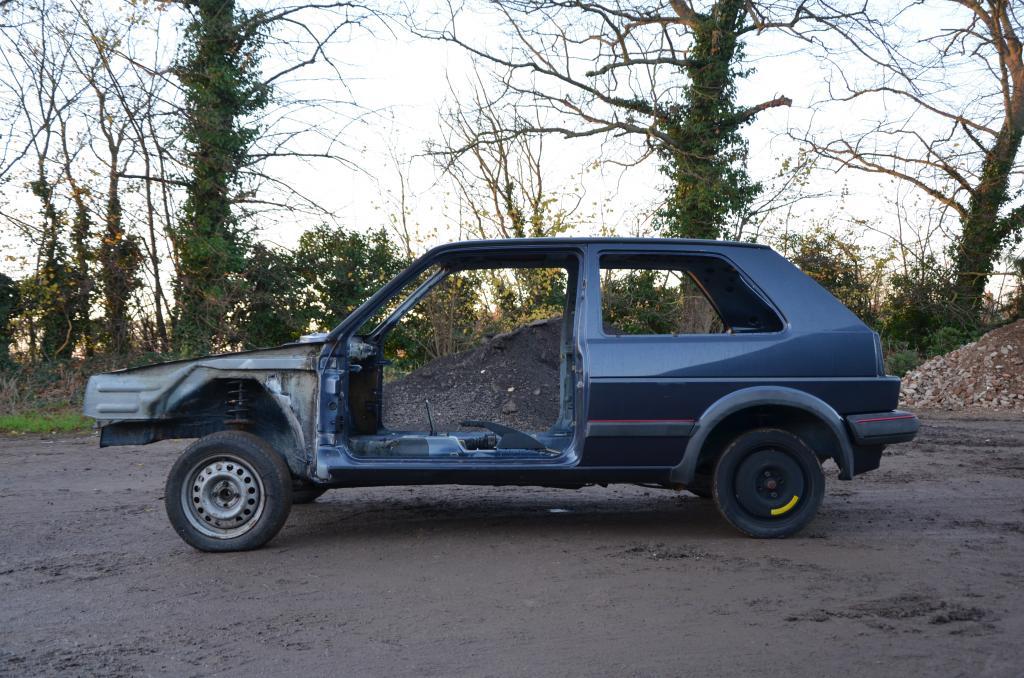
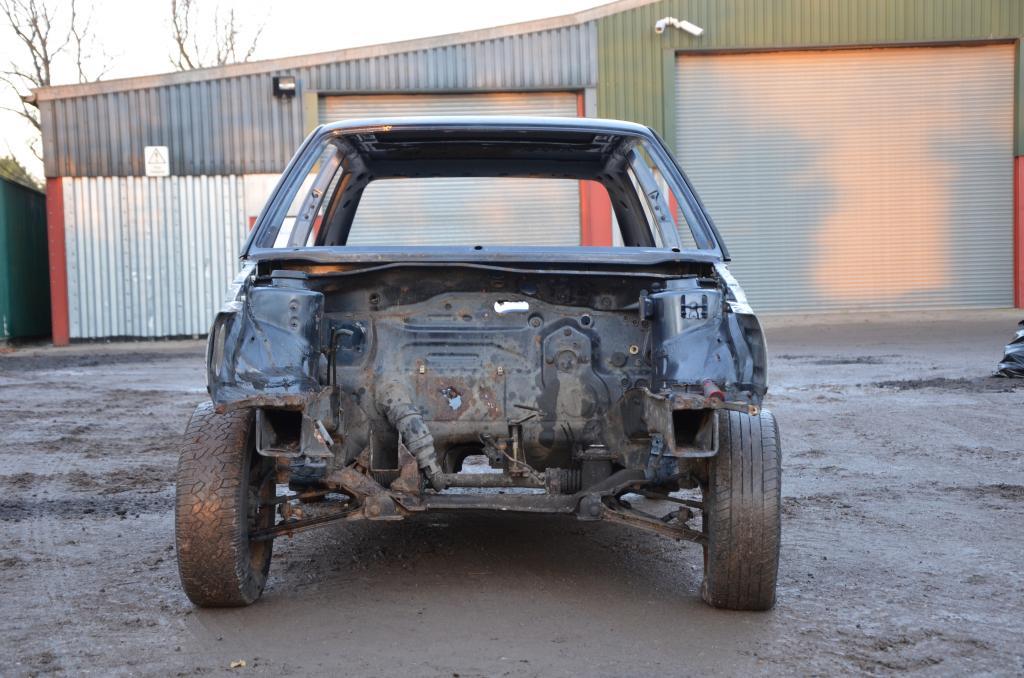
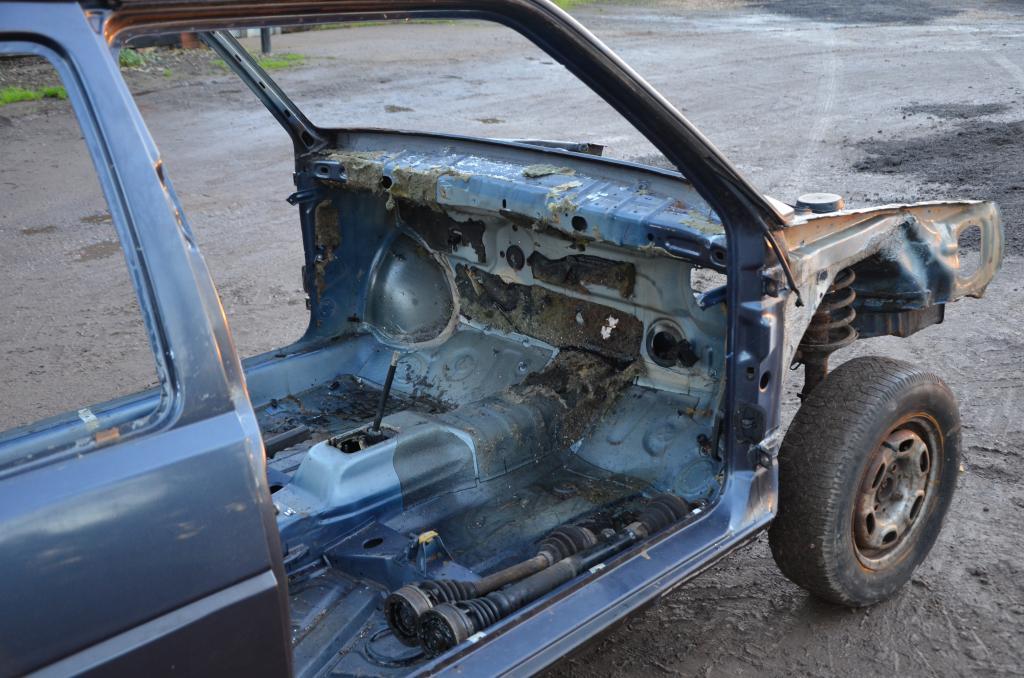
The only 2 pieces of rust/rot that will need to be addressed is the scuttle panel which I was aware of.
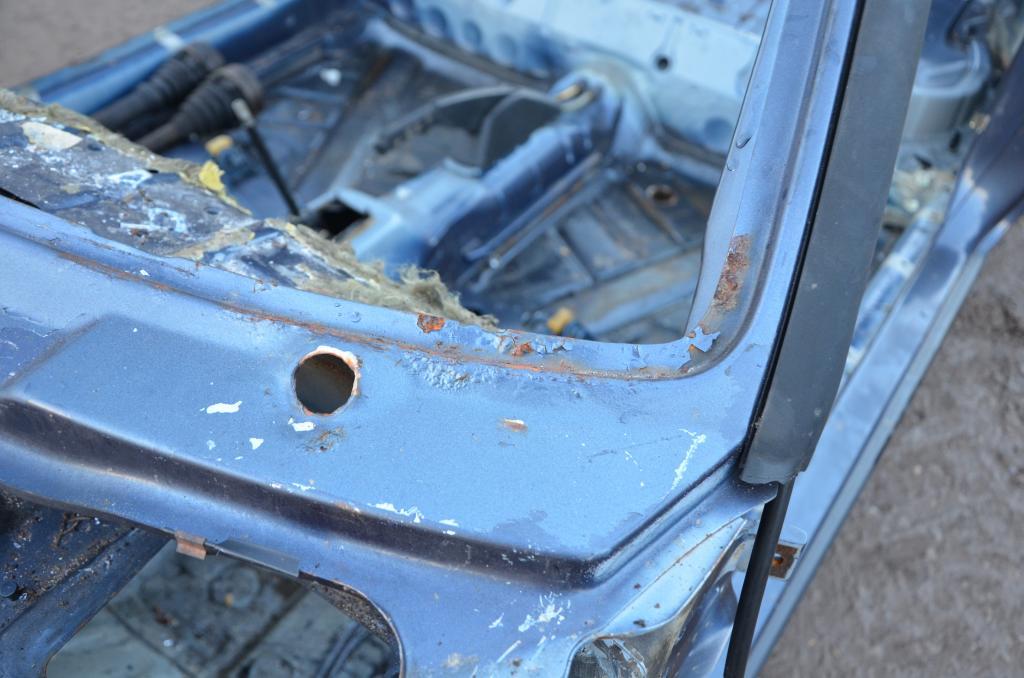
The other being due to a knackered engine mount allowing the downpipe to come into contact with the firewall. Eventually wearing through and then the moisture being trapped in the sound deadening finished it off. Either way it’s a pretty straightforward fix.
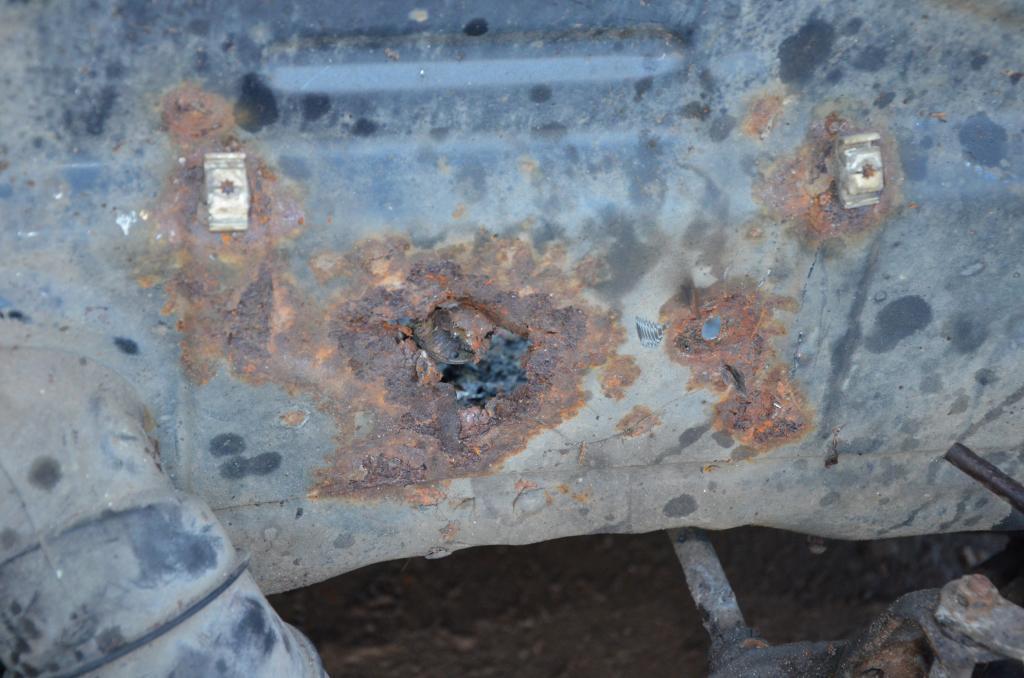
That’s it for now
Some progress at last, have had a few days off work to crack on with a few things on the Golf. A Friend of mines Dad now builds roll over jigs in built and kit form. I opted for the kit/self build option as I wanted to get it before Christmas. Took a couple of hours to weld it all together and get the Golf up in the air!
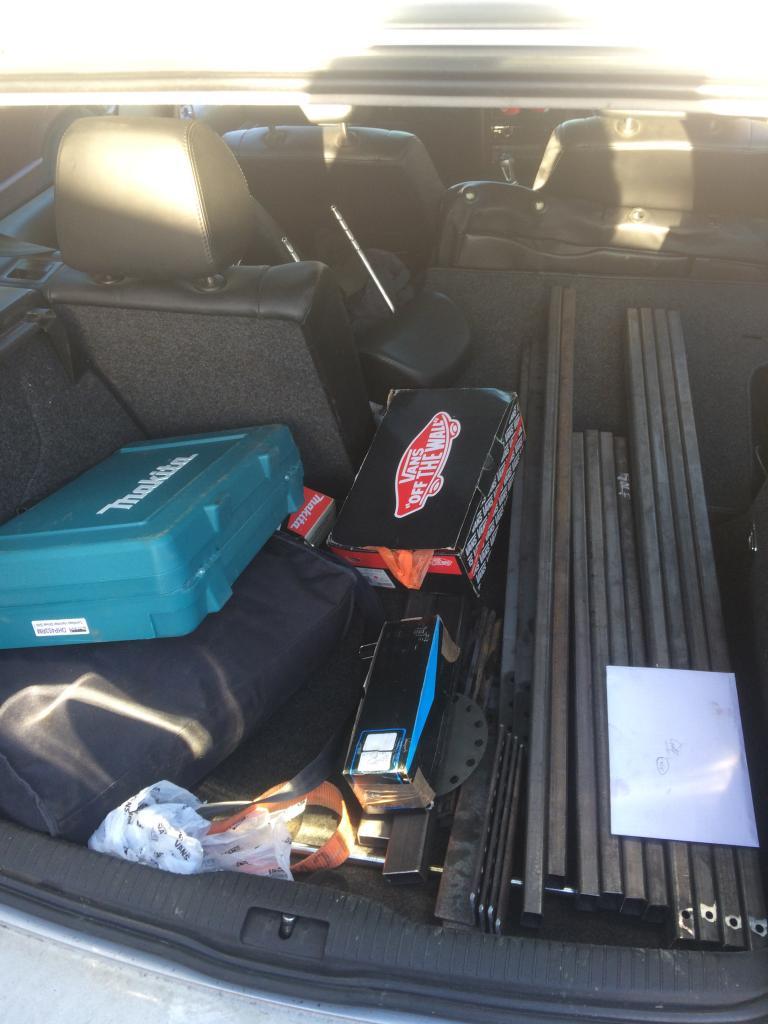
Test fit
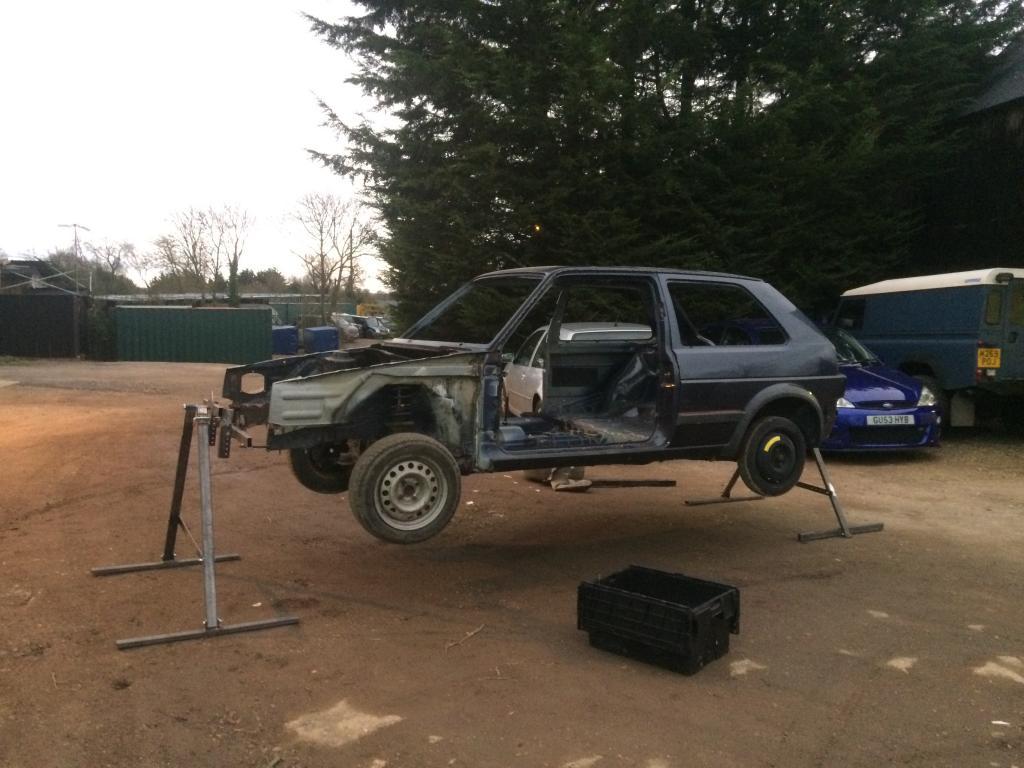
Also treated myself to some new toys, was sick of having to recharge my old drill every 10 minutes. This ones 18v and 4AH. Plenty of torque and lasts an age!
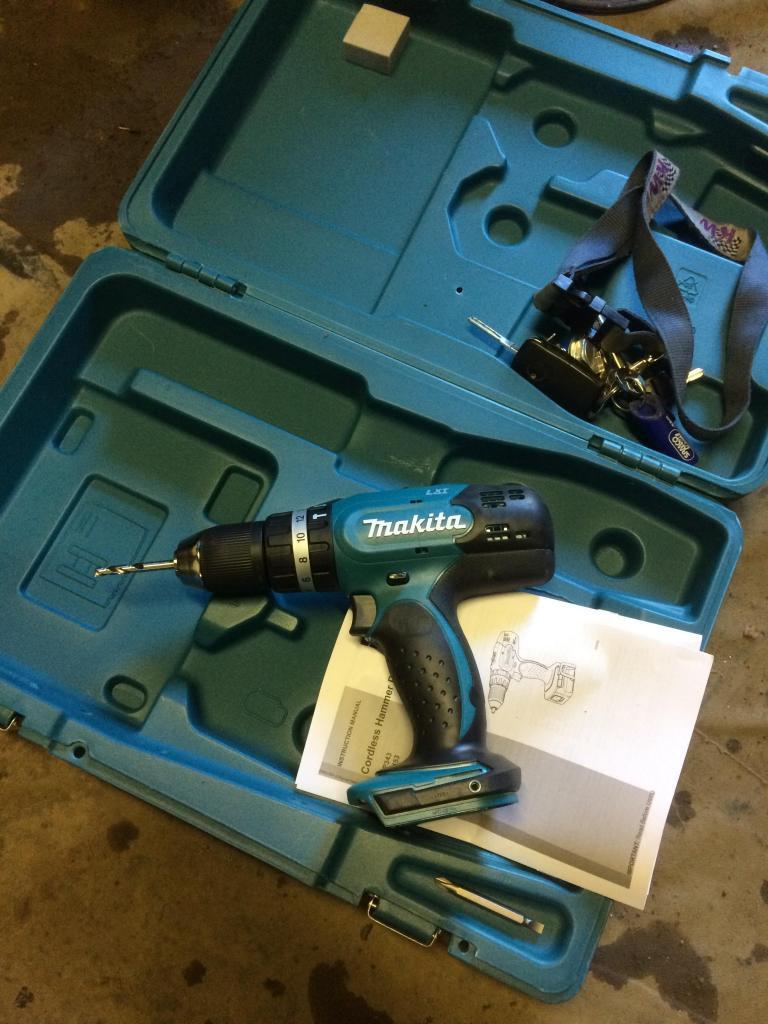
Set to work removing the now redundant bits inside the shell, 64 spot welds later….
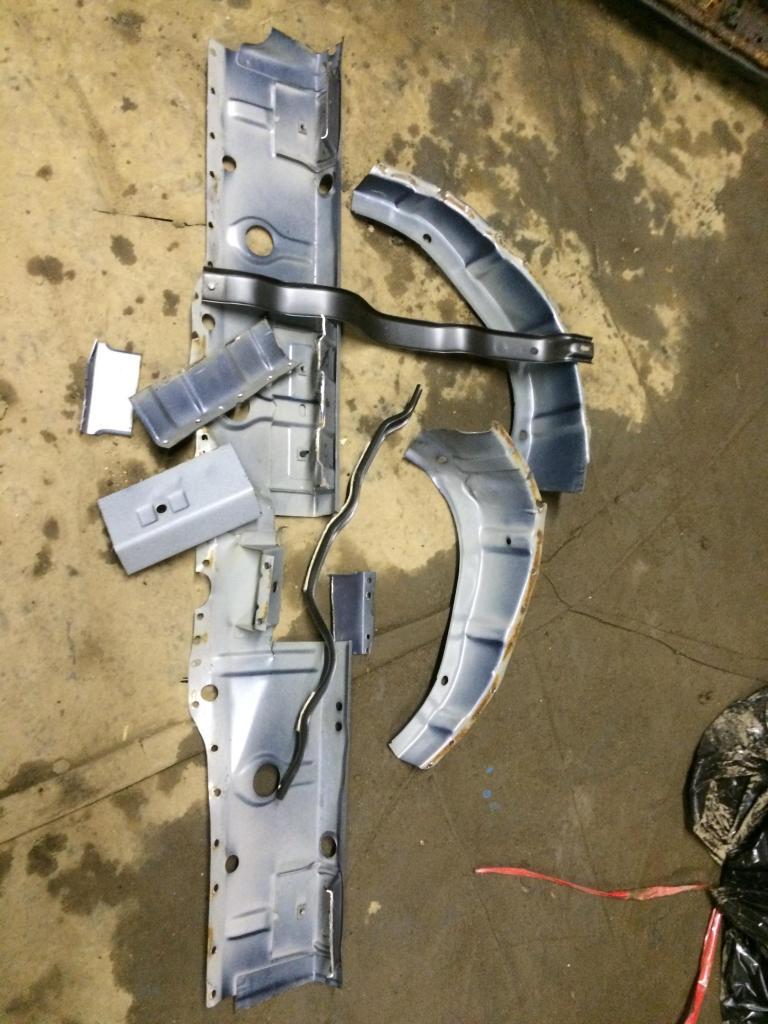
Got the car back inside the workshop late Christmas Eve with the help of 2 friends to lift the bugger on the roll over. James seen here doing his best Aladdin impression in the floating golf.
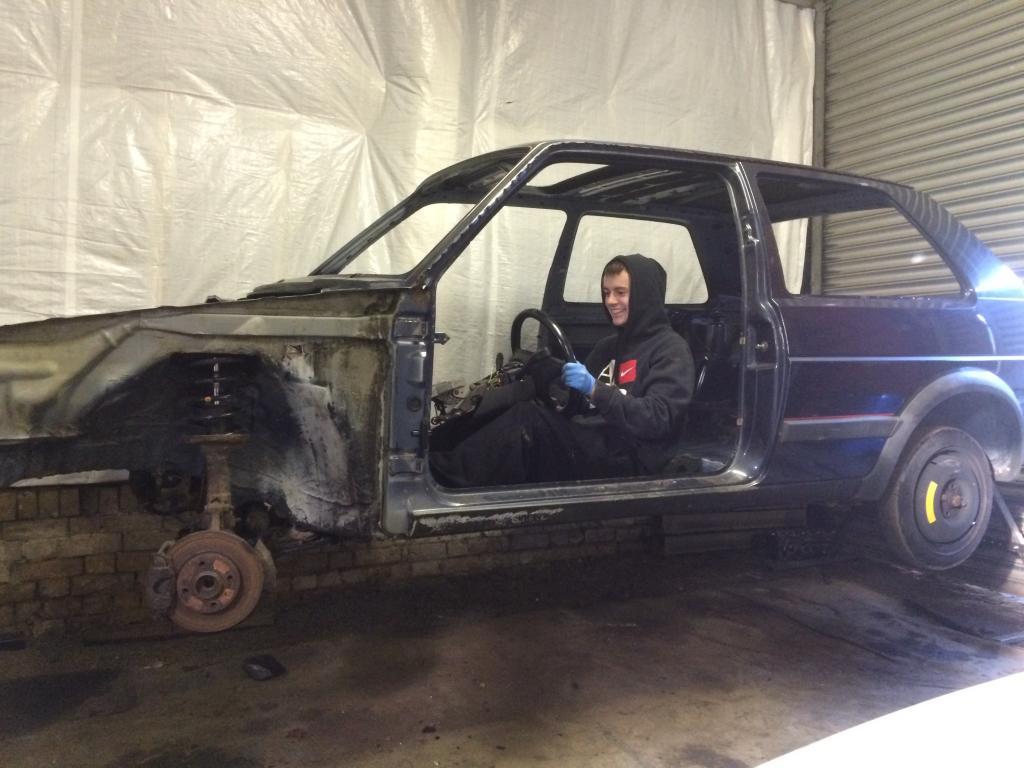
Farther Christmas bought me exactly what I was after! Can you believe that!
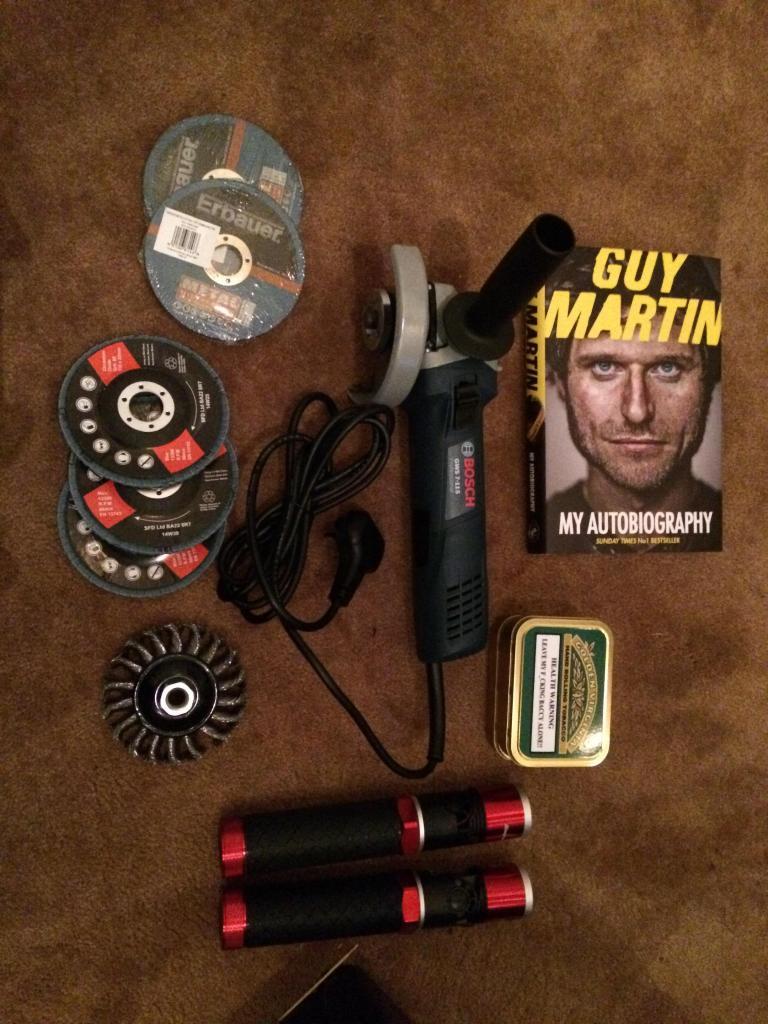
Snuck away this morning to get the final measurements checked and double checked. Simple plumbline and a few datum points. Within 1mm each side and end to end. Car’s straighter than I thought!
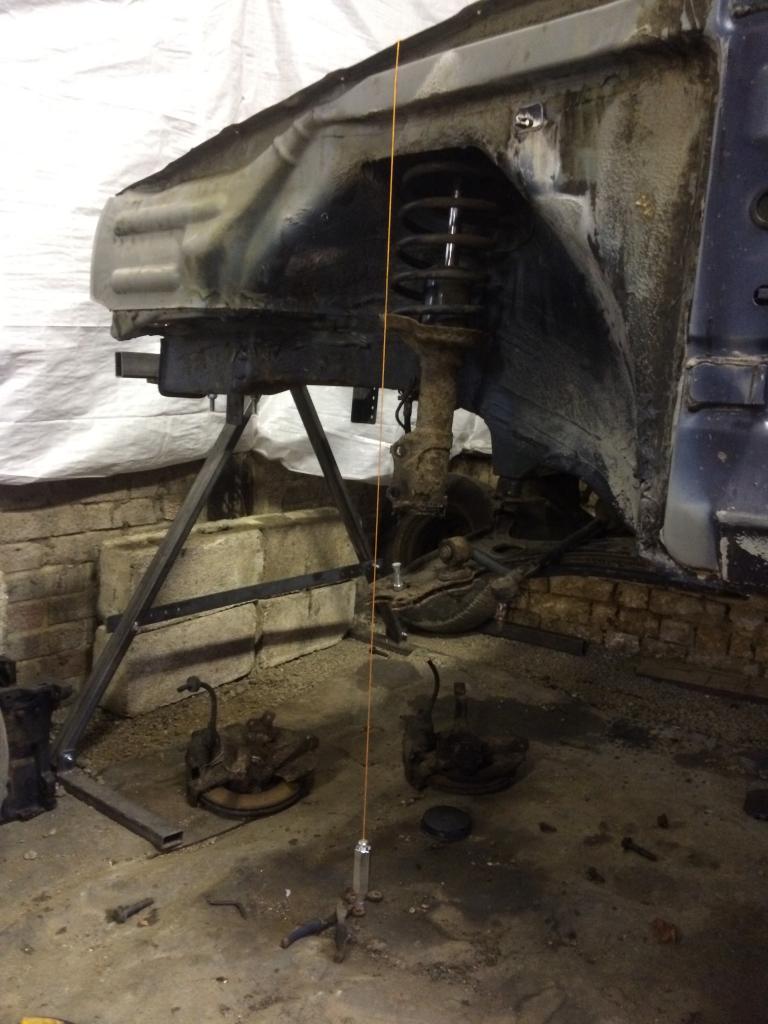
Stripped the front subframe off
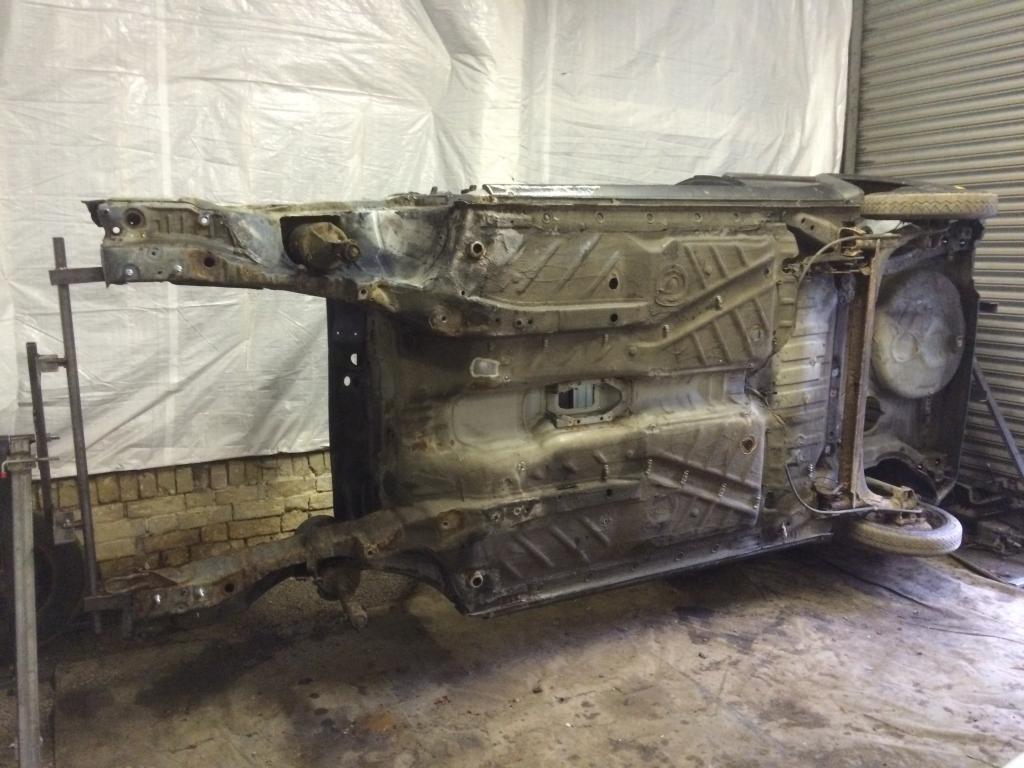
Set to work removing the stone chip and underseal. Possbily the worst job in the world, cars looks really solid though. Couple of small repairs to be done around the drainage holes/bungs but nothing major.
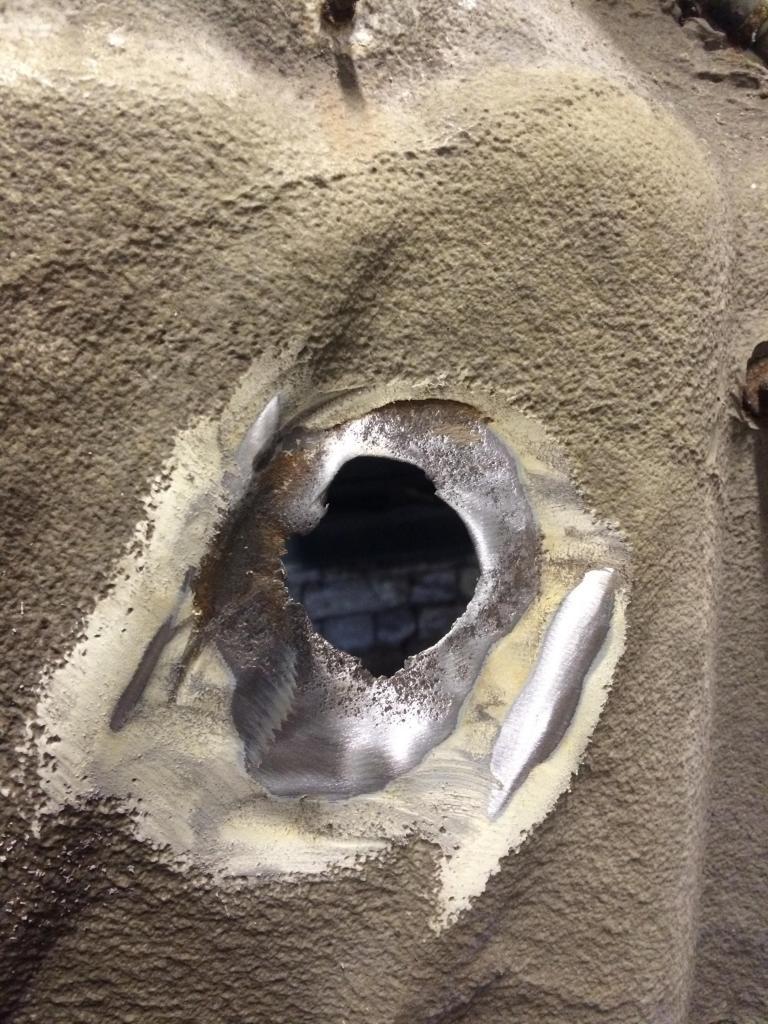
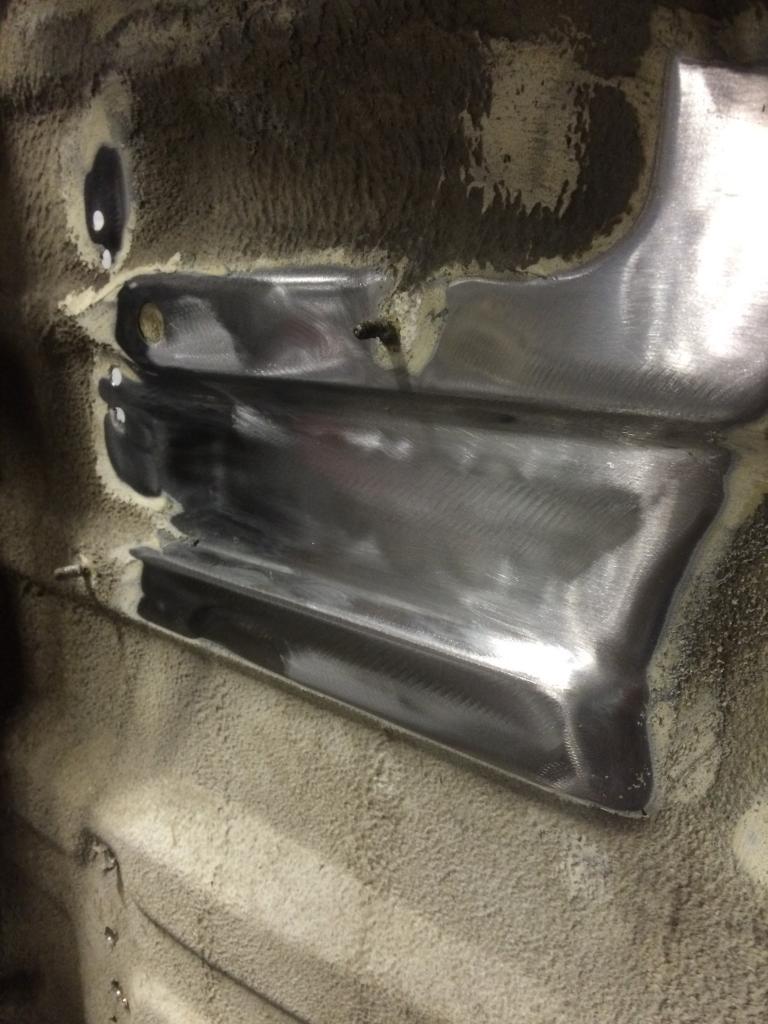
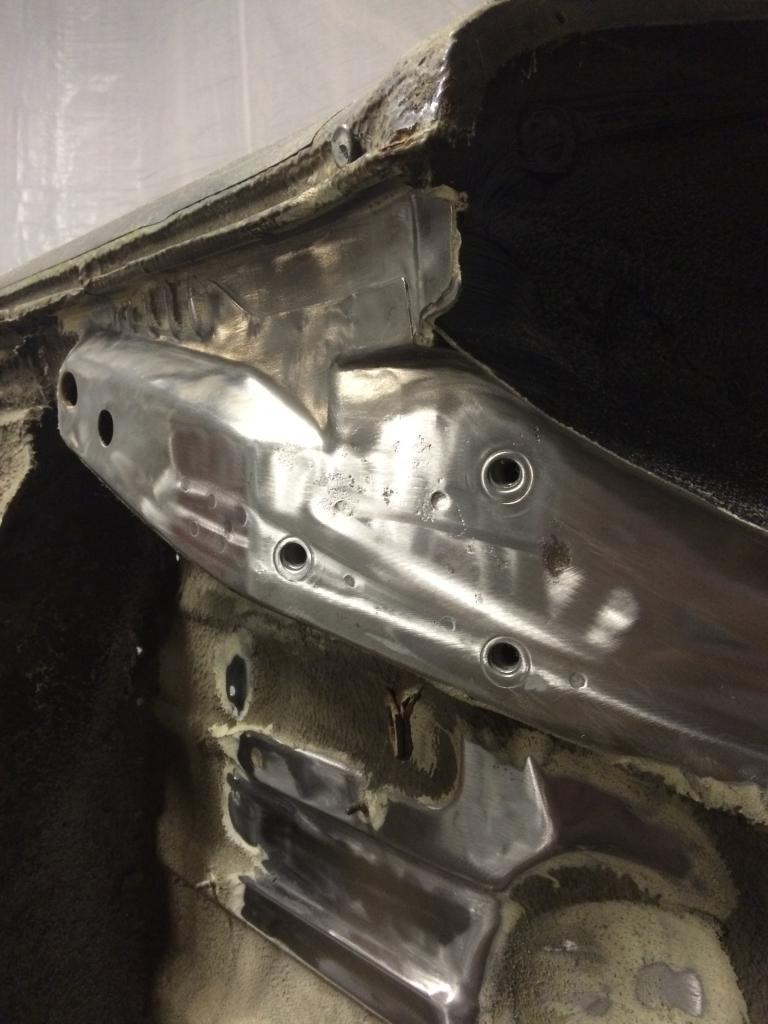
Packed up for tonight and quickly got a temporary coat of primer on to stop it flash rusting overnight. Hopefully can rope a couple of mates in over the coming days to get the rest stripped off. Certainly won’t be easy but I can get on with seam welding the shell before I remove any more panels.
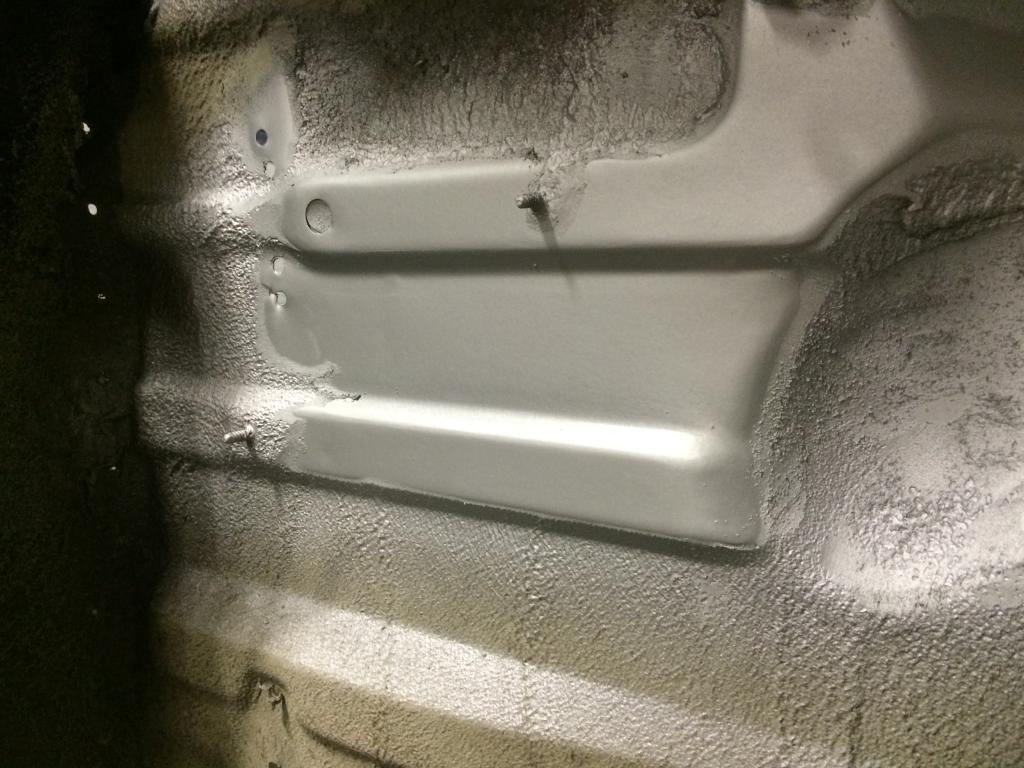
Progress! It’s taken the best part of 4 full days of possibly the most soul destroying task ever to get to this point. Still have the engine bay and interior sound deadening to strip off yet. Looking better now though. Massive thankyou went to a couple of my friends who stupidly volunteered themselves to help with this one.
Let the fun begin. Heat, Scrape, Grind, Repeat.
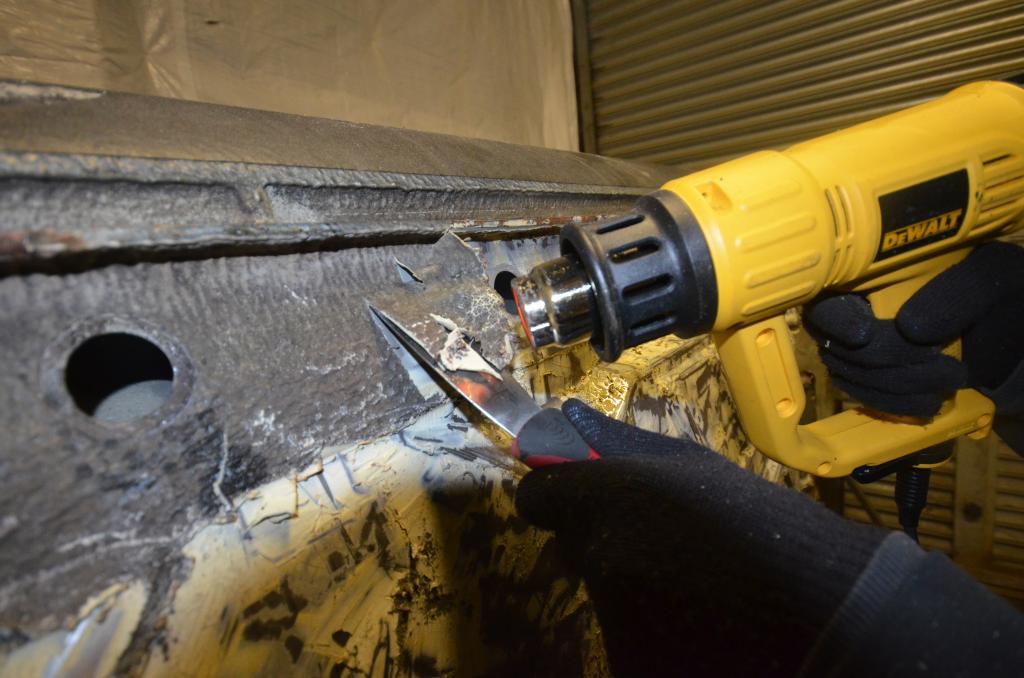
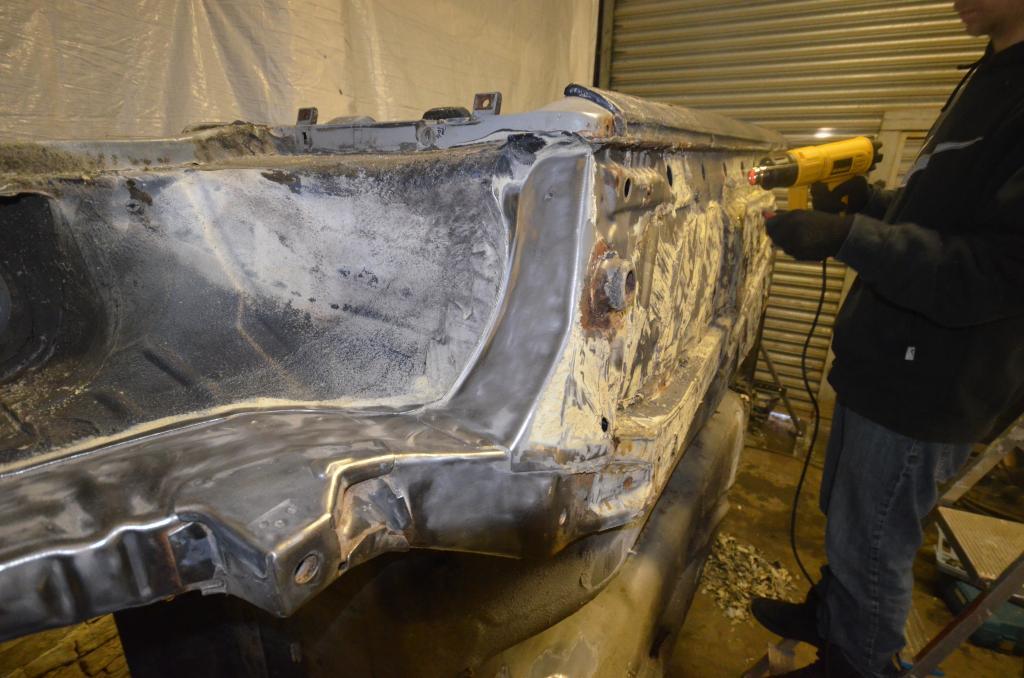
Jacking points are both a bit rough so will replace these once I find a supplier that can do both repair panels.
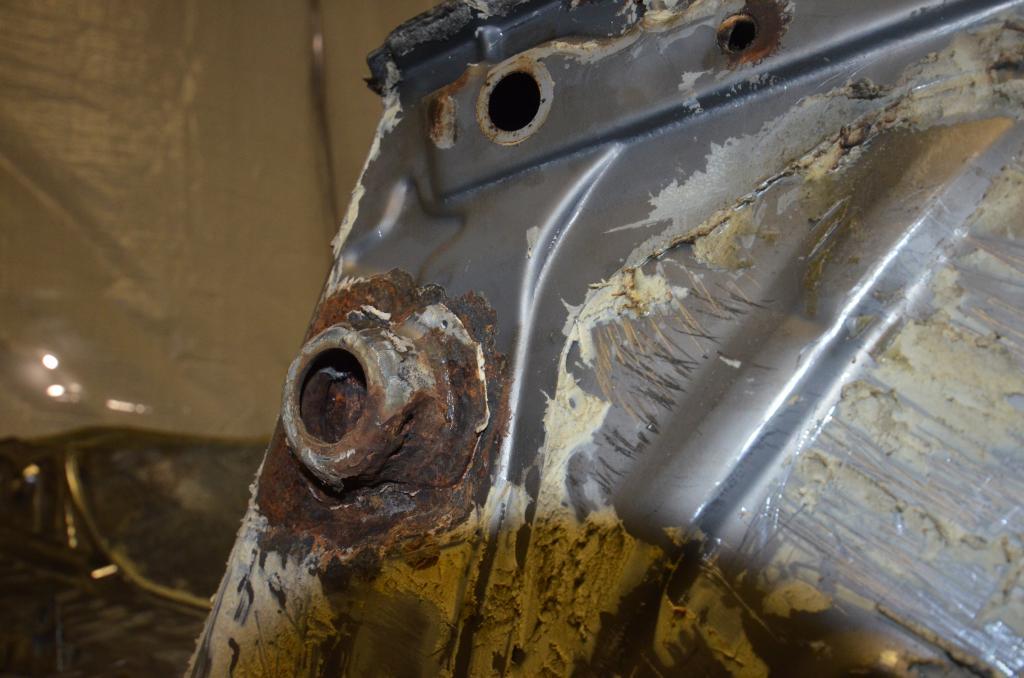
Drivers side is a little worse, again not the end of the world

Finally getting somewhere now
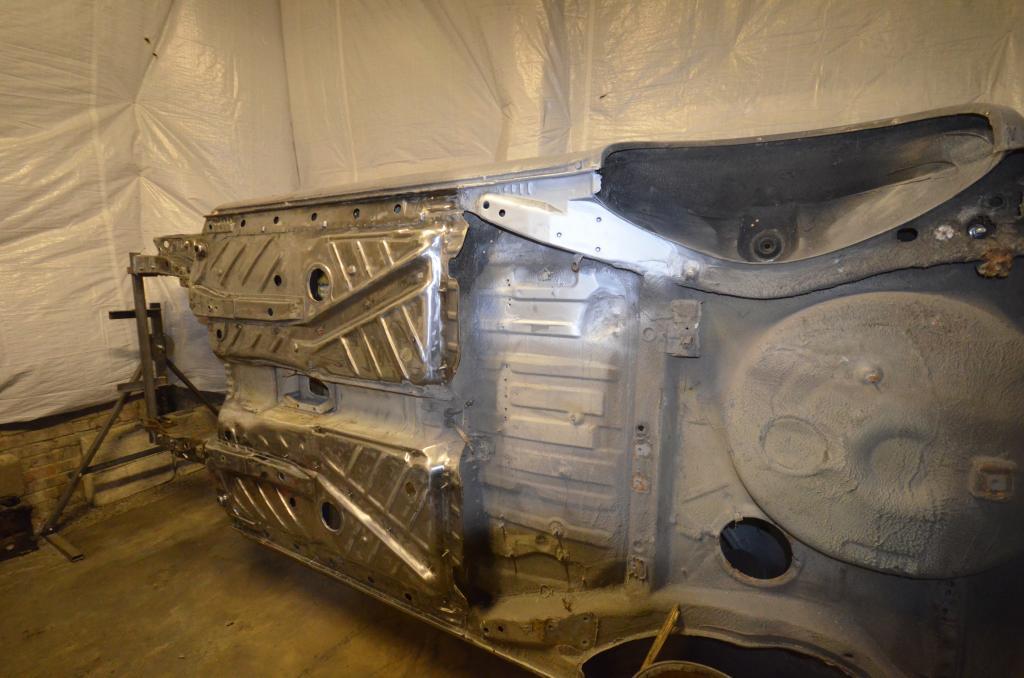
Finally at a stage now where I can get some temporary primer on it and get the jig mounted up ready to start fabricating the new sub frame mounts.
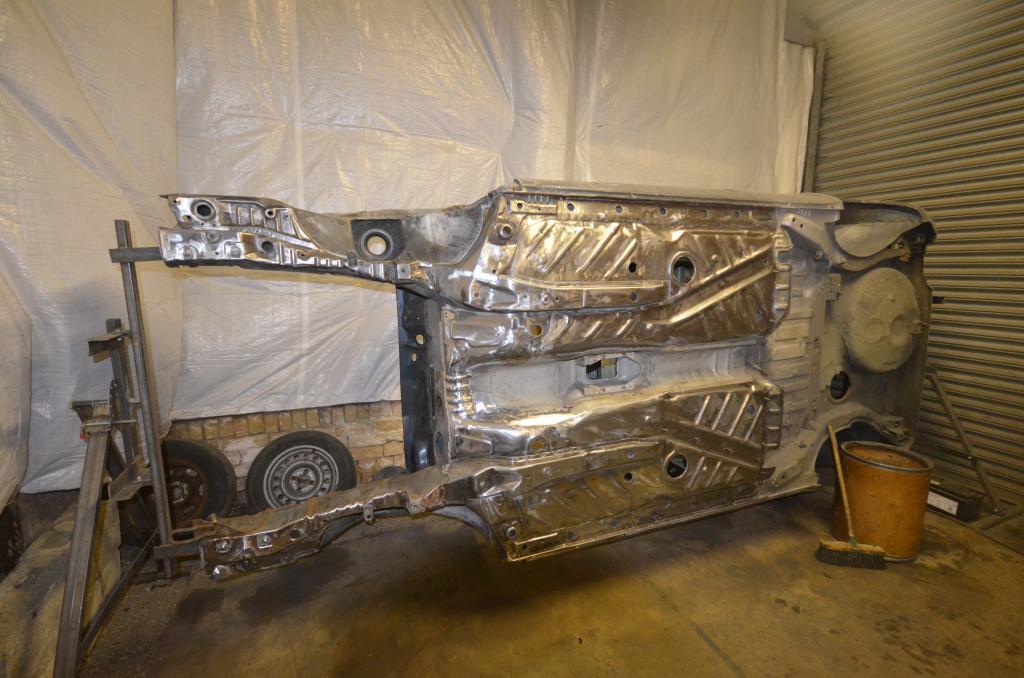
Unfortunately I’ve been real busy with the day job so haven’t managed to get a great deal done on the golf over the last couple of weeks. Without that though there’d be no money to do this…. Anyway on with the update.
Was feeling really brave late one evening so made my way over to the work shop and set to work welding in a couple of bracing bars ready for when I remove the rear boot floor.
You can see them here 30x30x3 box section, overkill really but better be safe than sorry.
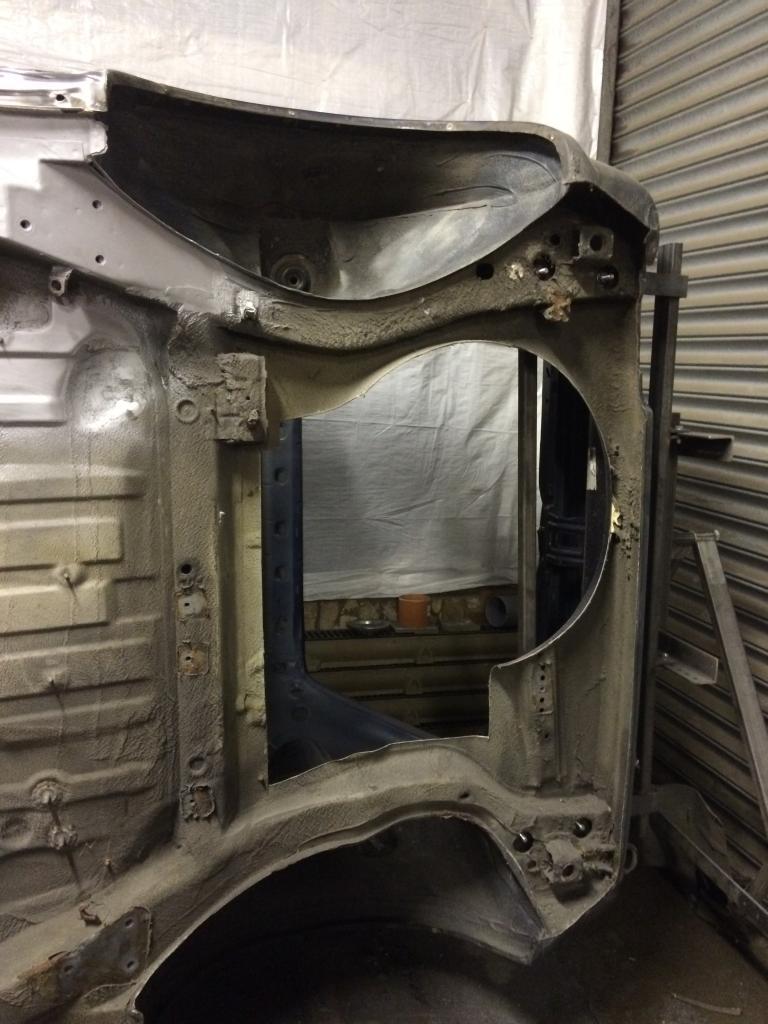
Really scary now….
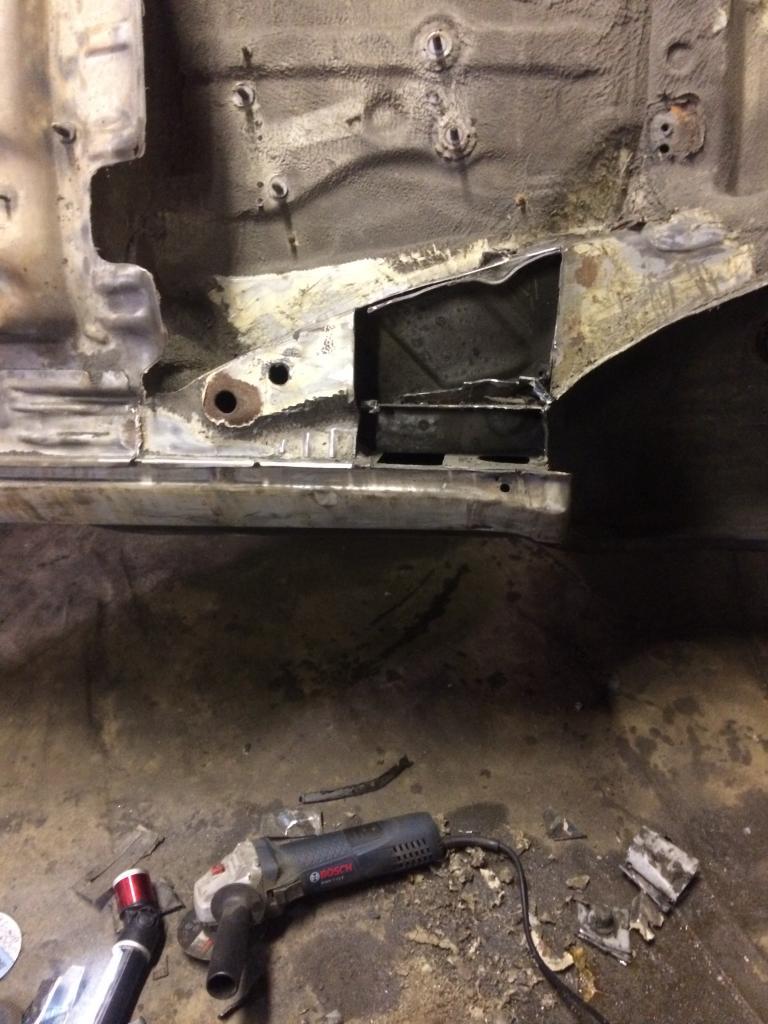
And a bit more gone
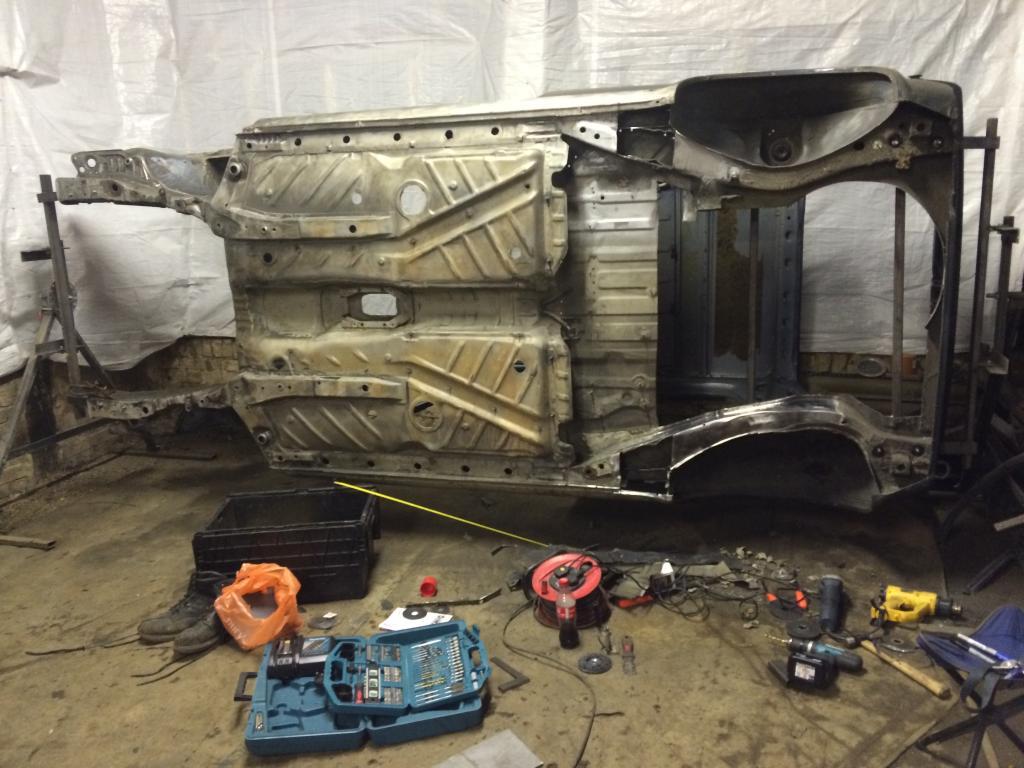
And the jig is in! Needs to be lined up yet and tweaked but a basic first mock up position im very happy.
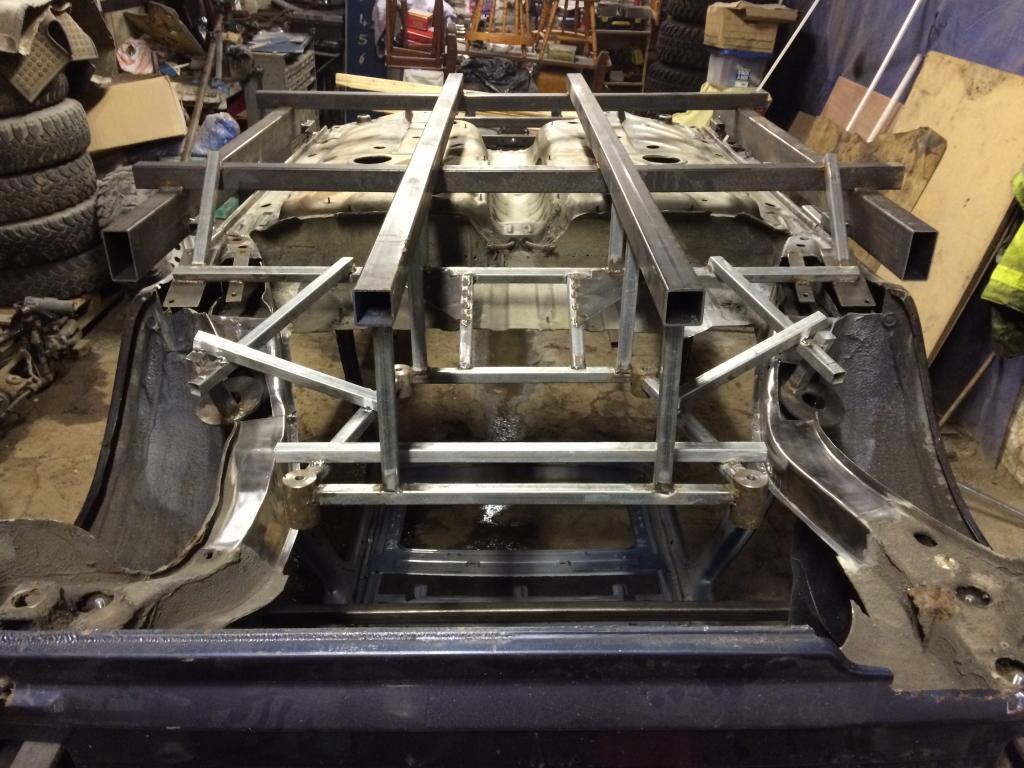
Found this is Hobby Craft!! Had to have it, just need to find a 1:24 scale TT now to pull the engine and subframes from
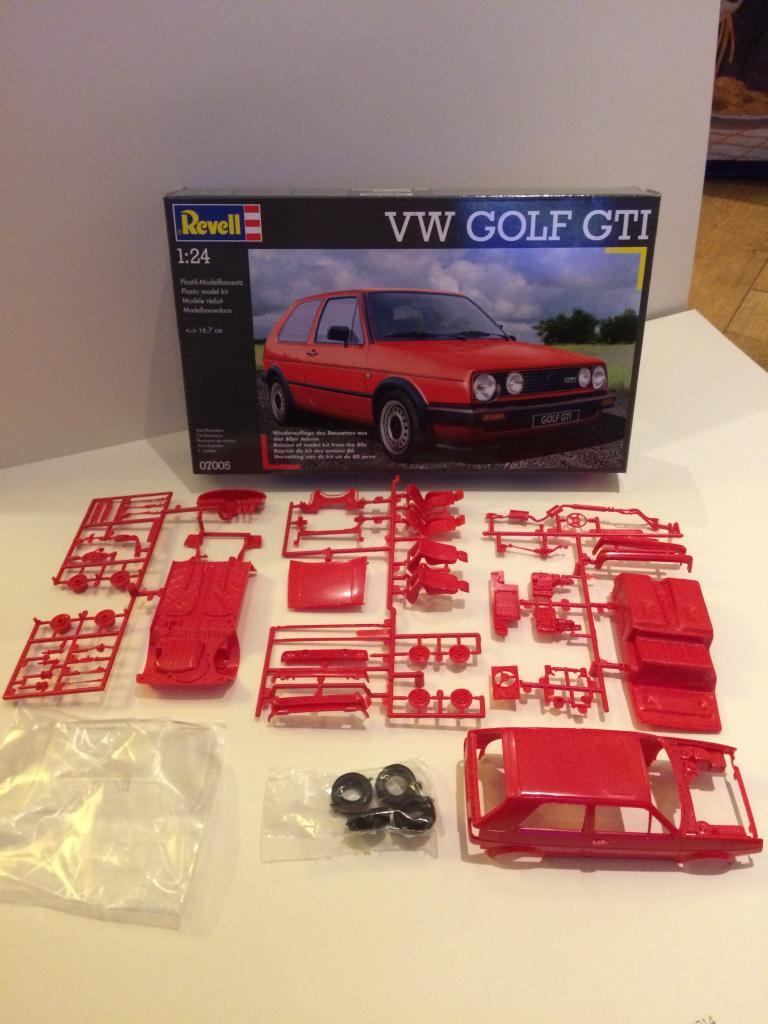
Metal delivery turned up this morning, so can crack on over the weekend getting the rear subframe mounts in position.
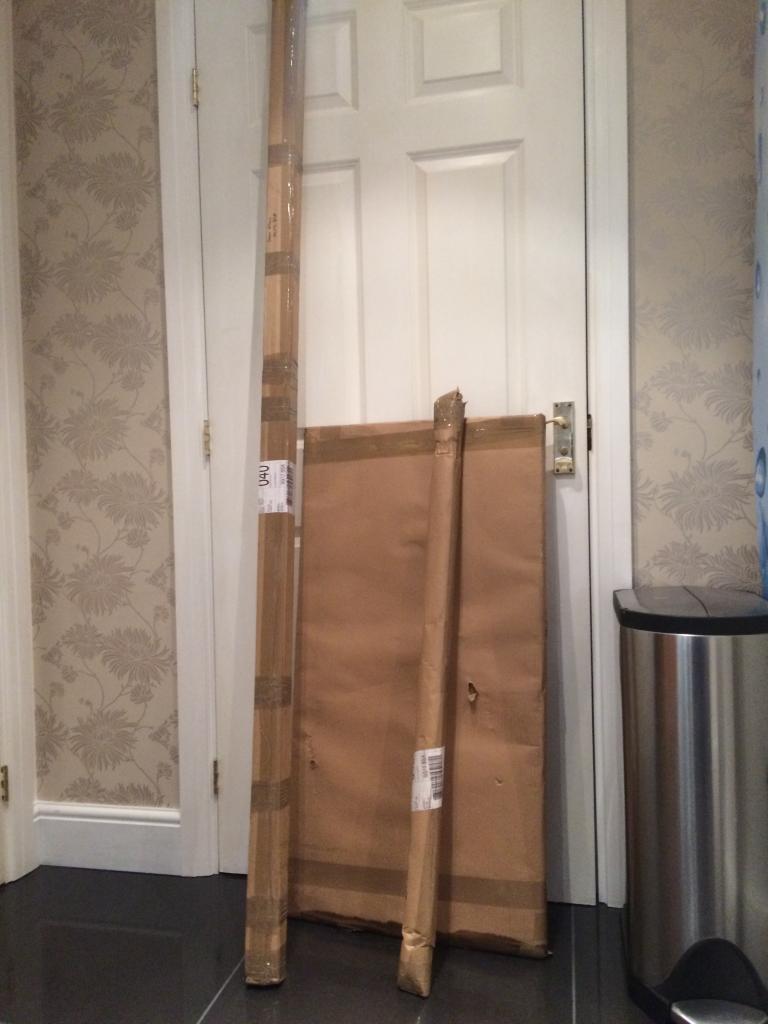
Bit of light reading to do, think this is looking the most likely choice for management now as it seems to do everything I need it to without costing £1,000,000!!
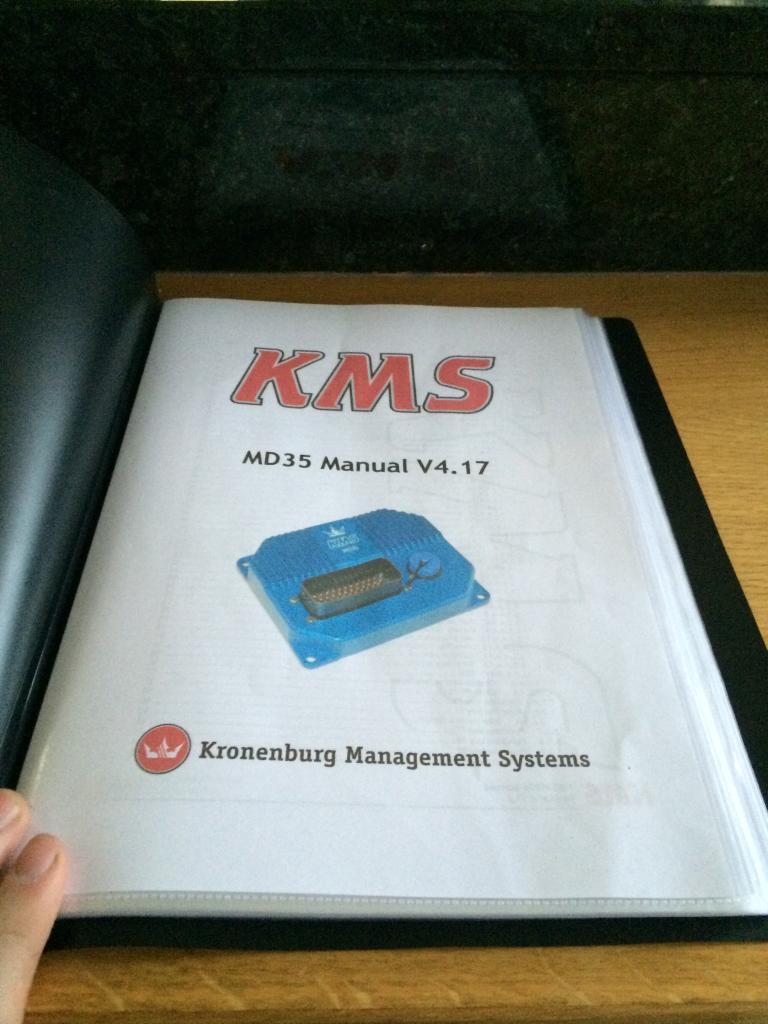
Who pays attention to that???
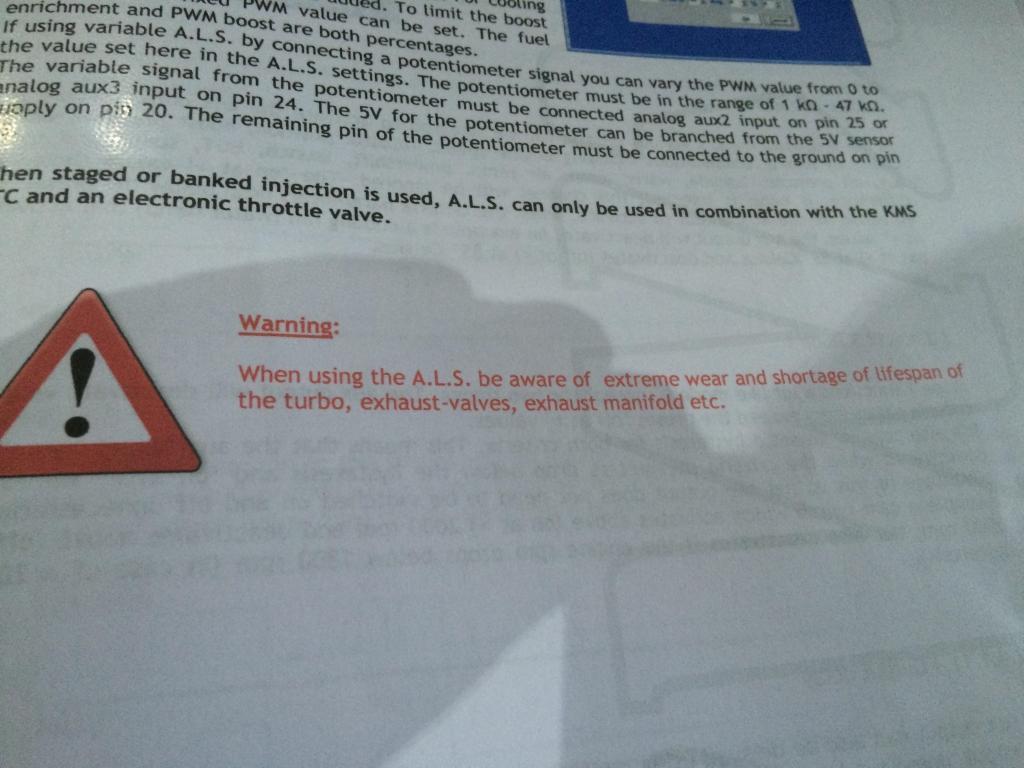
Been very busy with the day job over the last few days so have limited time to get myself up the barn but managed to get a bit done tonight!
I need to start getting the roll cage in place before I cut any more of the shell out. First up is a tube connecting to rear of the chassis rails together. Managed to source for 2inch CDS for this which is ideal. Could have possibly got away with a smaller diameter but this will tie into the cage nicely.
Also removed the small brackets that were used in the factory for transporting the shells.
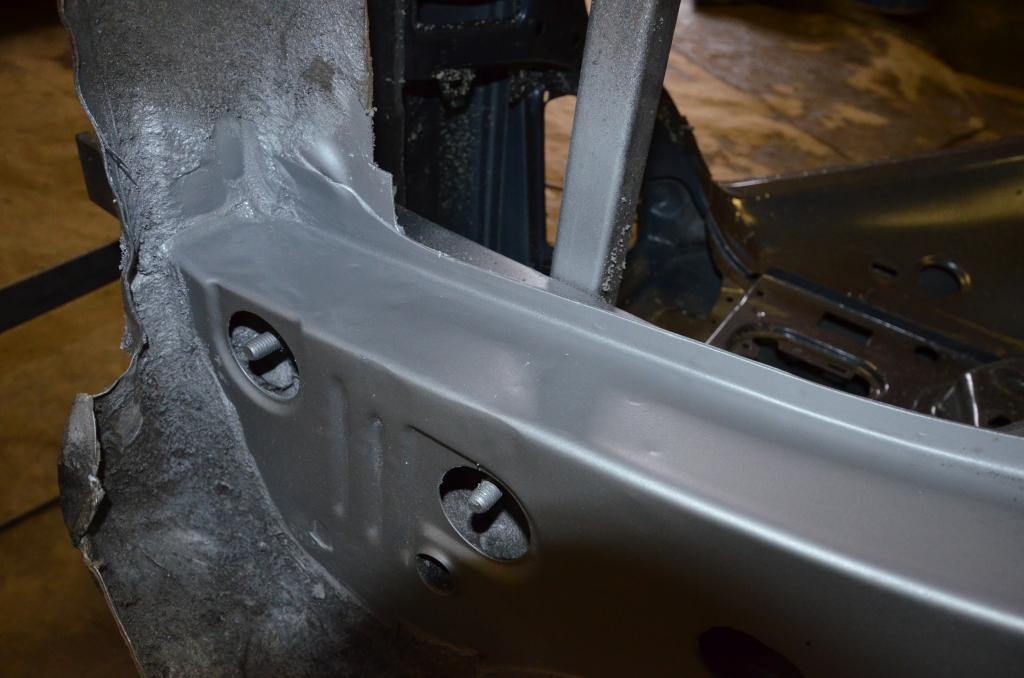
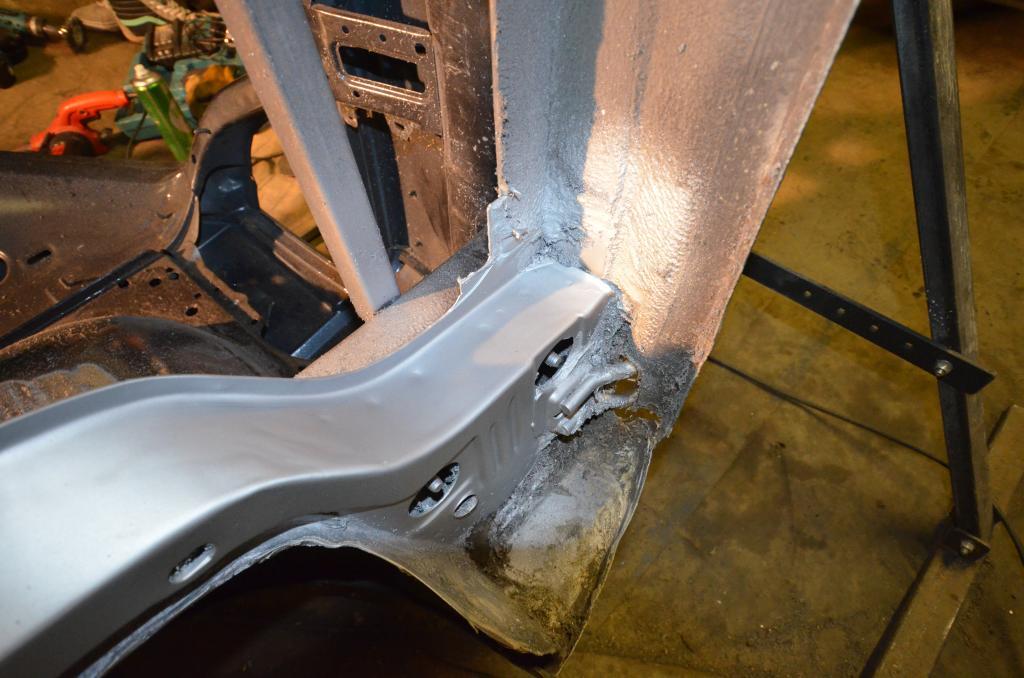
Made some re-enforcement plates out of 3mm sheet. The cage tubing will then weld to this rather than directly to the kit kat wrapper thickness chassis rails
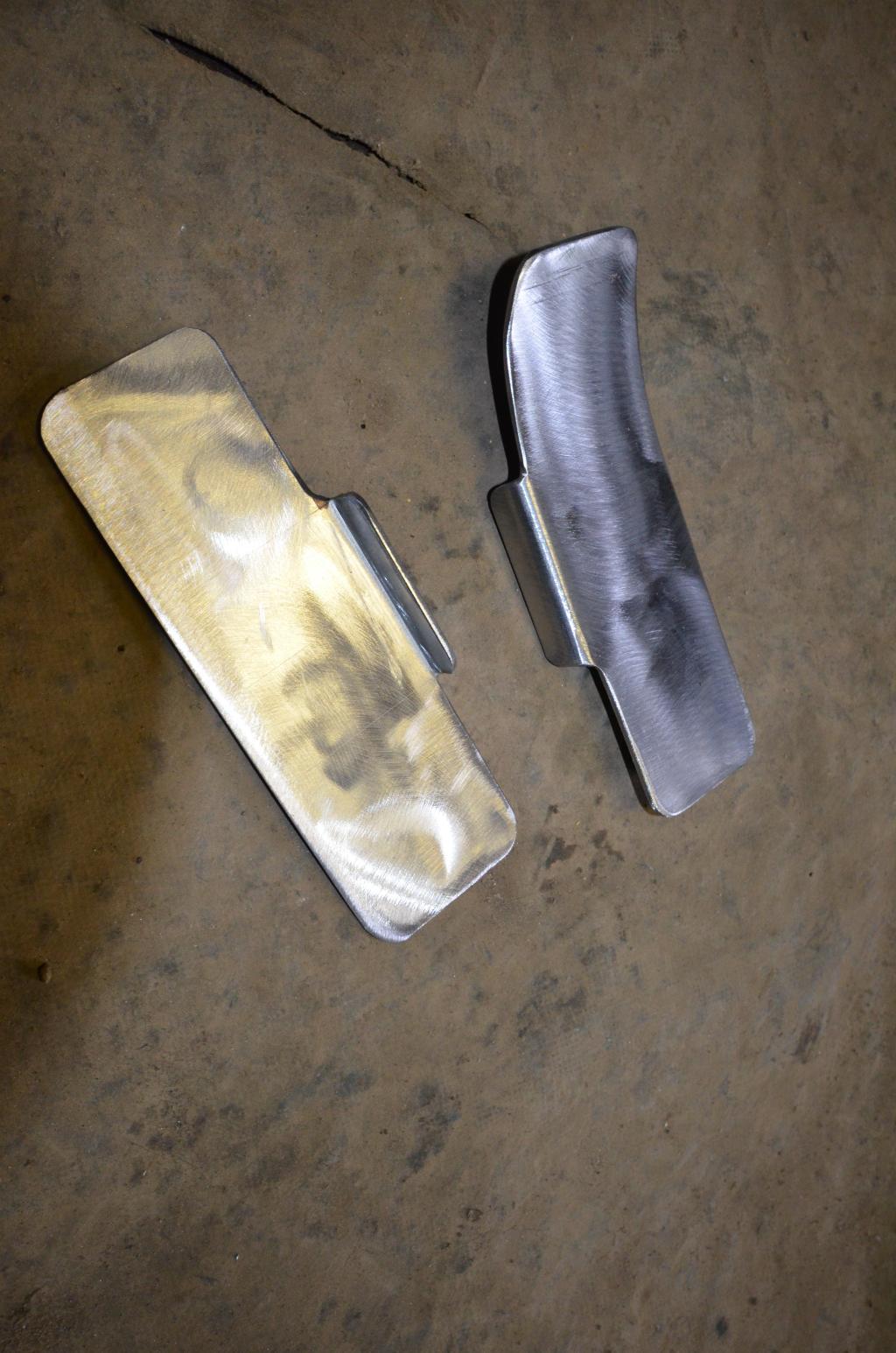
Was a bit tricky to create the curve for the driver’s side chassis leg but we found a way…..oxy acetylene.
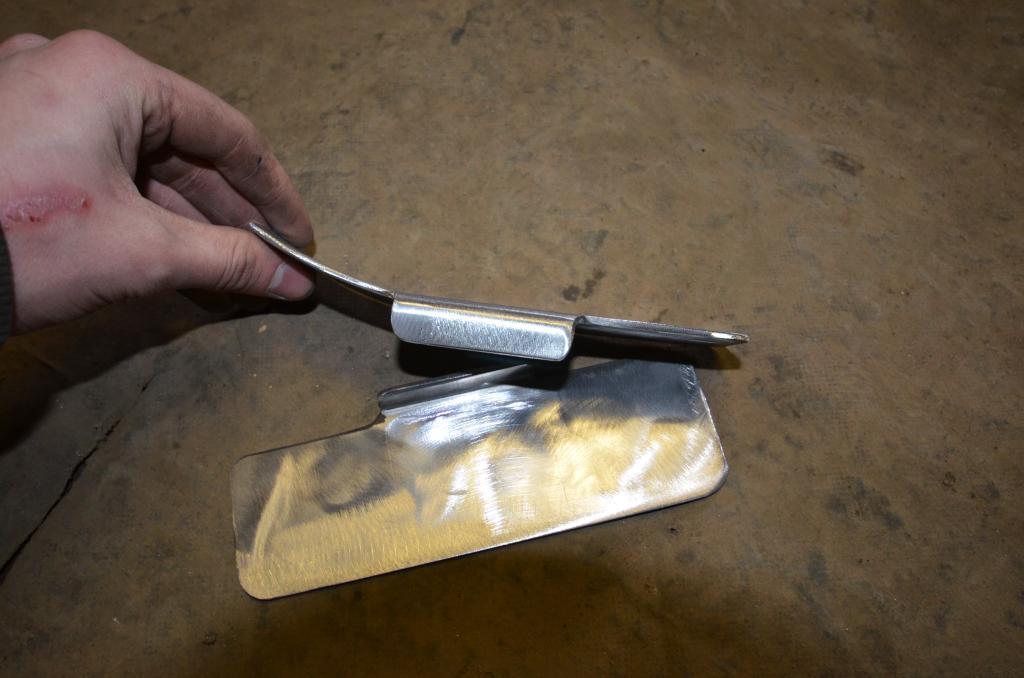
One in place
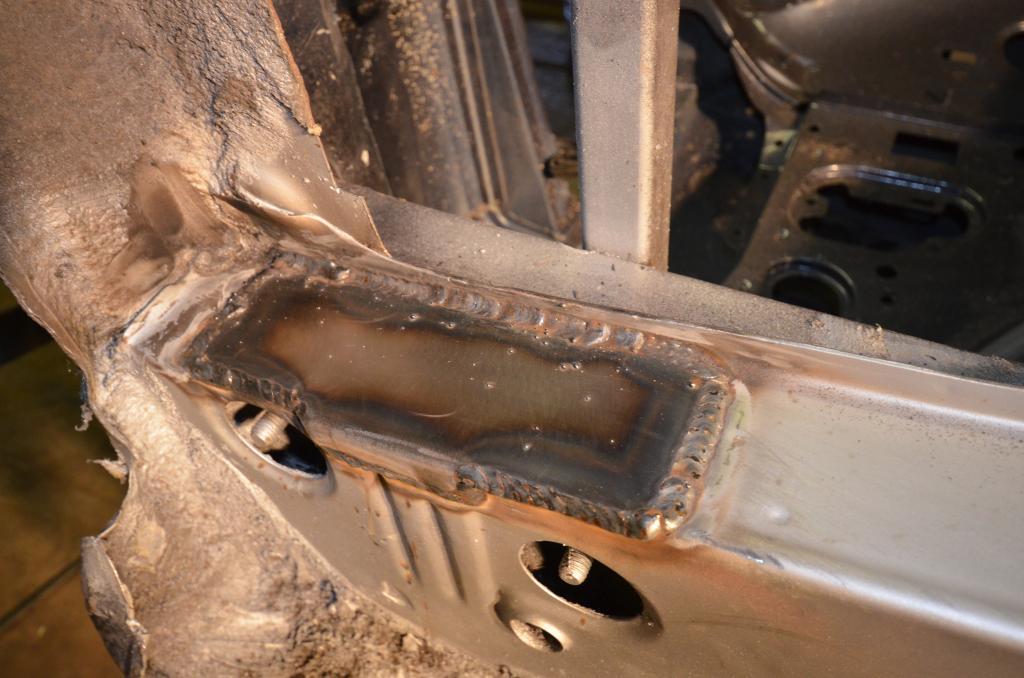
And the other
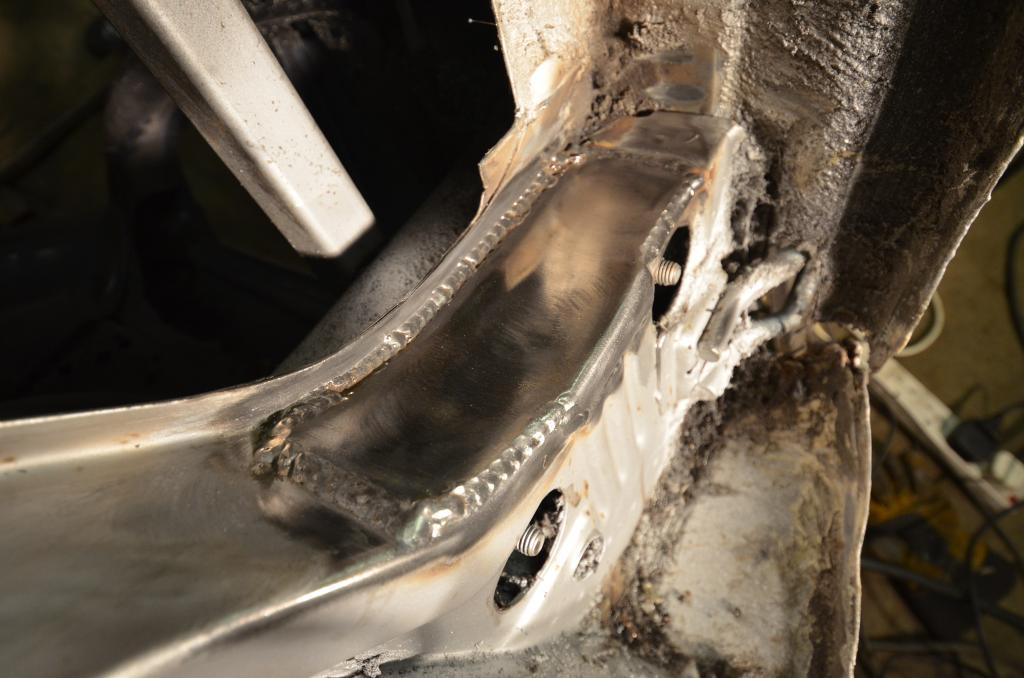
Quick coat of weld through primer to stop it flash rusting. Will tidy the welds up once the shell has been shot blasted.
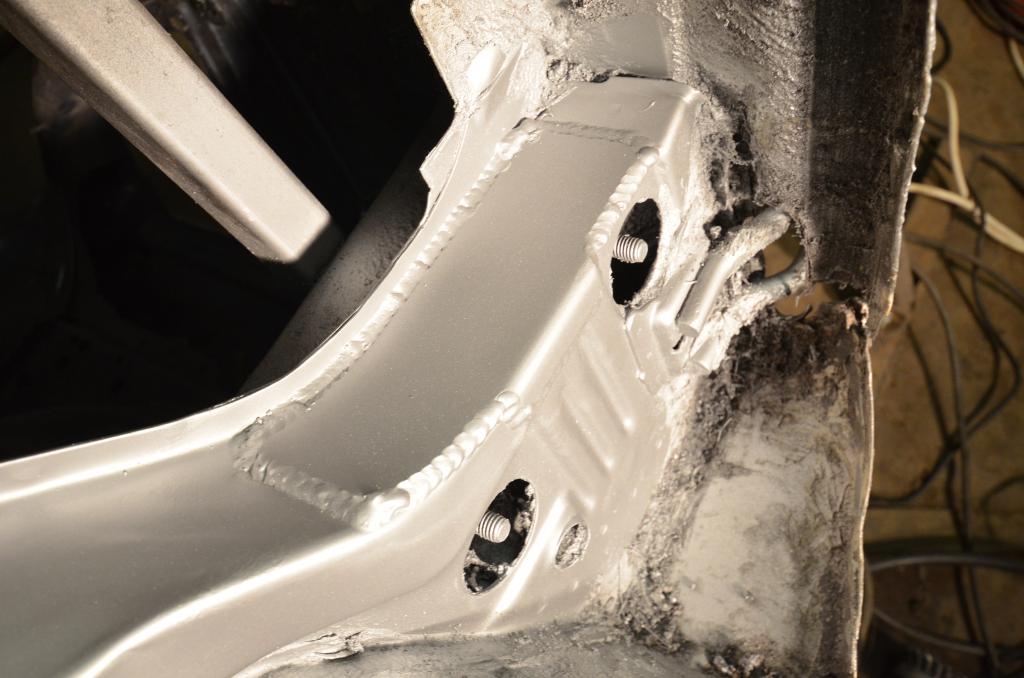