Ok Ok Ok Ok......asked the question and forgot I did....
Start with the disc assemblies then.....its all about the rotor....these 4542 Castings from AP serve a number of motorsport applications and feature in competition kits from AP racing for all sorts of cars from Scoobies, Fords if anybody have ever bothered tp read the Seat Supercopa Race Car parts catalogue then you'll see them in there too...
They're hard, heat treated post machining and the initial treatment involves them being treated in molten salt.
So heres the rotor fresh out of the box we paint the heat temp paint on it to save the guys a job trackside
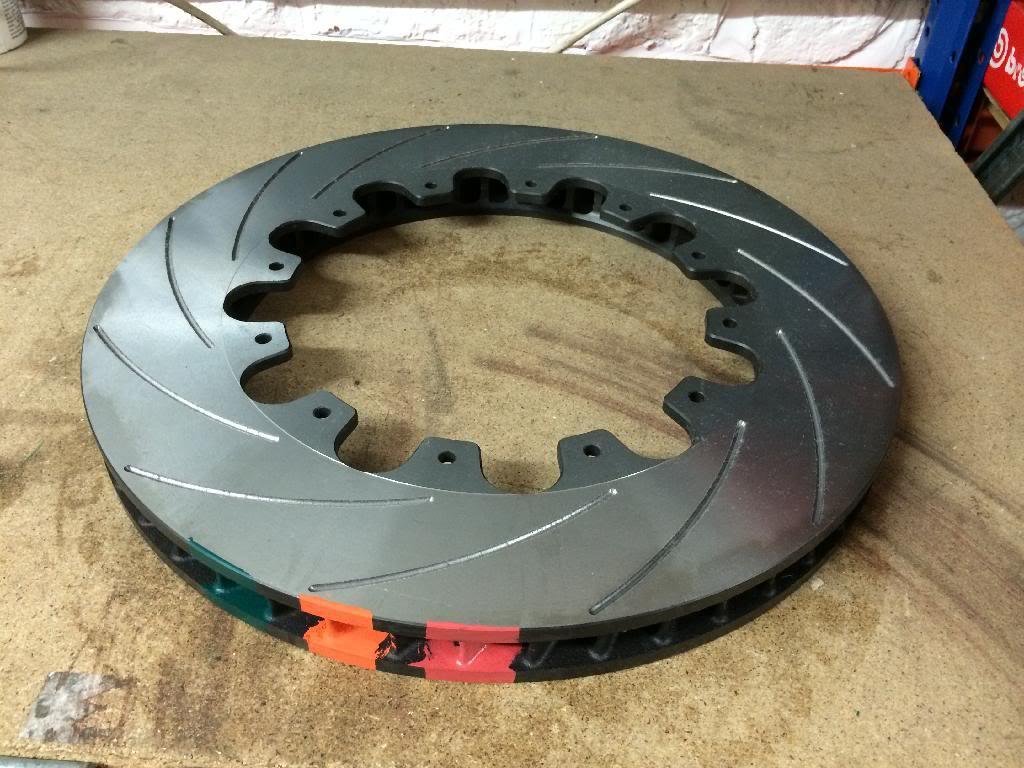
So we add our own design bell, this kit started life as a replacement disc assembly for the Caparo VWR kit, many will probably know Im not a huge fan for no there reason than the fact that when they arrived they were very hyped as being able to cope on track and win races.....they can't....in my very humble opinion they need to be floating at that diameter - theres been some failures which can happen to any supplier but things get hot in races and the forces involved in heat expansion are relentless....you need to manage heat and expansion to have reliability
spot the missing rotor......this is a VWR bell with rotors in numerous pieces in the kitty litter at Snetterton, it took out quite a bit of expensive kit when it exited stage left
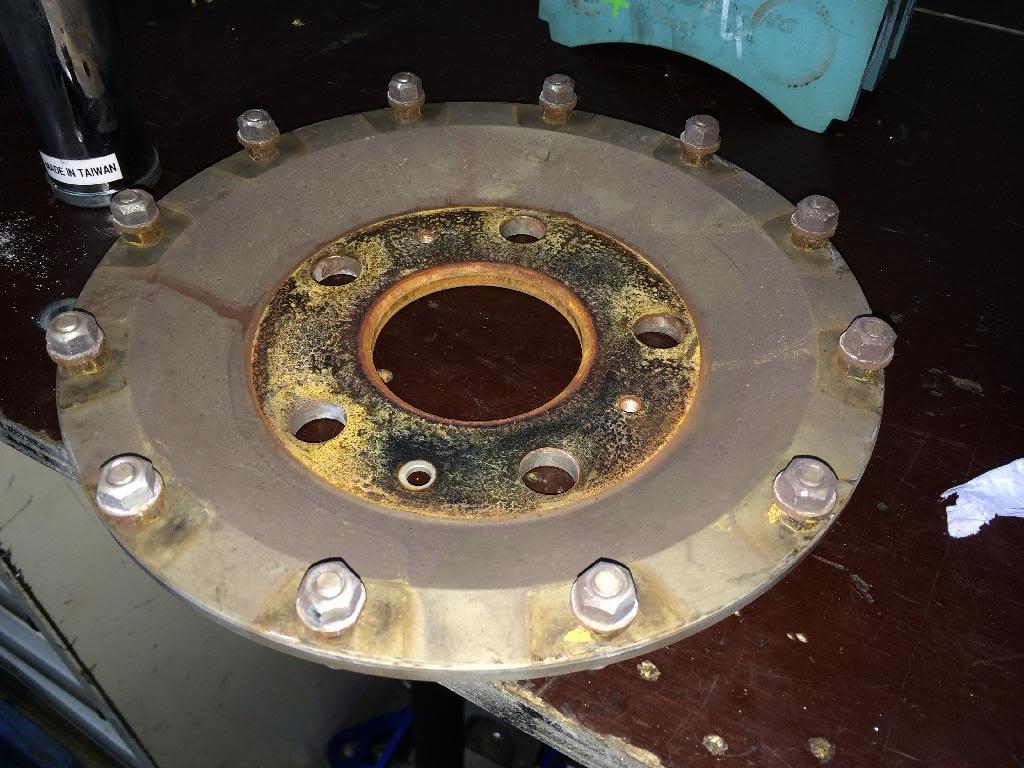
The bell is then added, its lightened on the front face and we also machine the rear of the bell to provide front face cooling, the mounting system is the same as on a GT car and the mods we do to the back of the bell are straight from a LMS car so whilst looking like a normal bell theres quite a bit of thought gone into it.
Without this sounding like an advert these disc assemblies are the same offset as the previous VW Caparo setup....so if you are fed up with warped rotors then I can supply you some road friendly versions of these assemblies in grooved or drilled
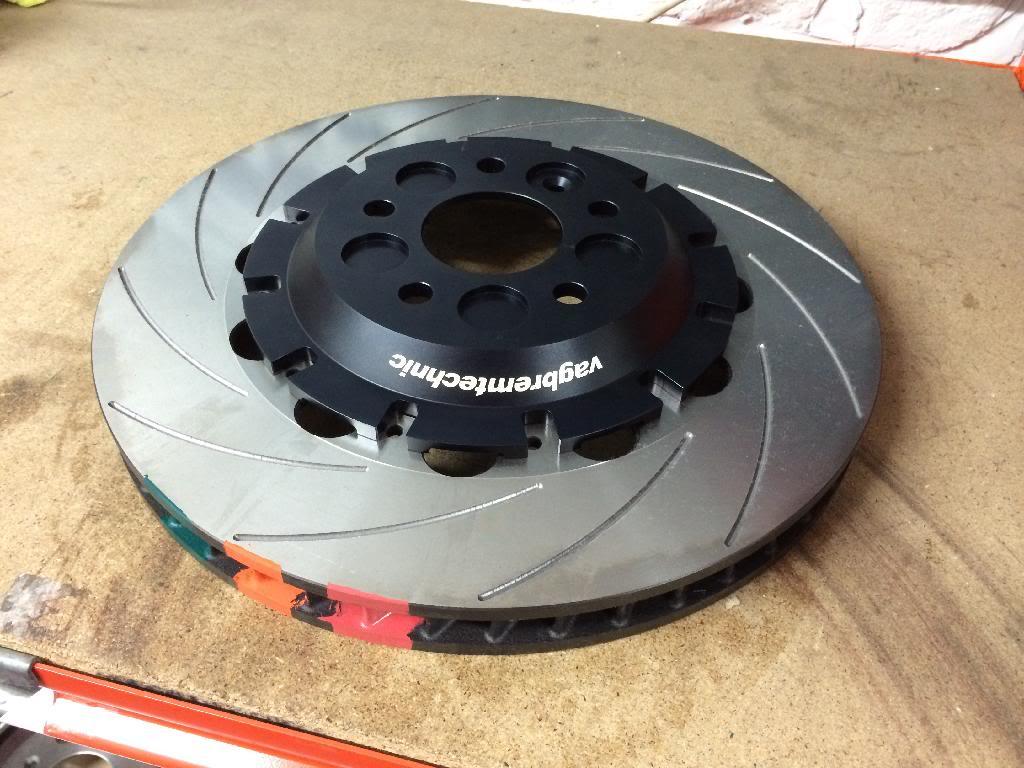
If you've ever wondered what floating or fully floating means then hopefully the pics that follow will help explain, we need to manage heat and expansion we need to mount the rotors to the bell in a manner that allows cooling, radial float and axial float. So we use these Bobbins......
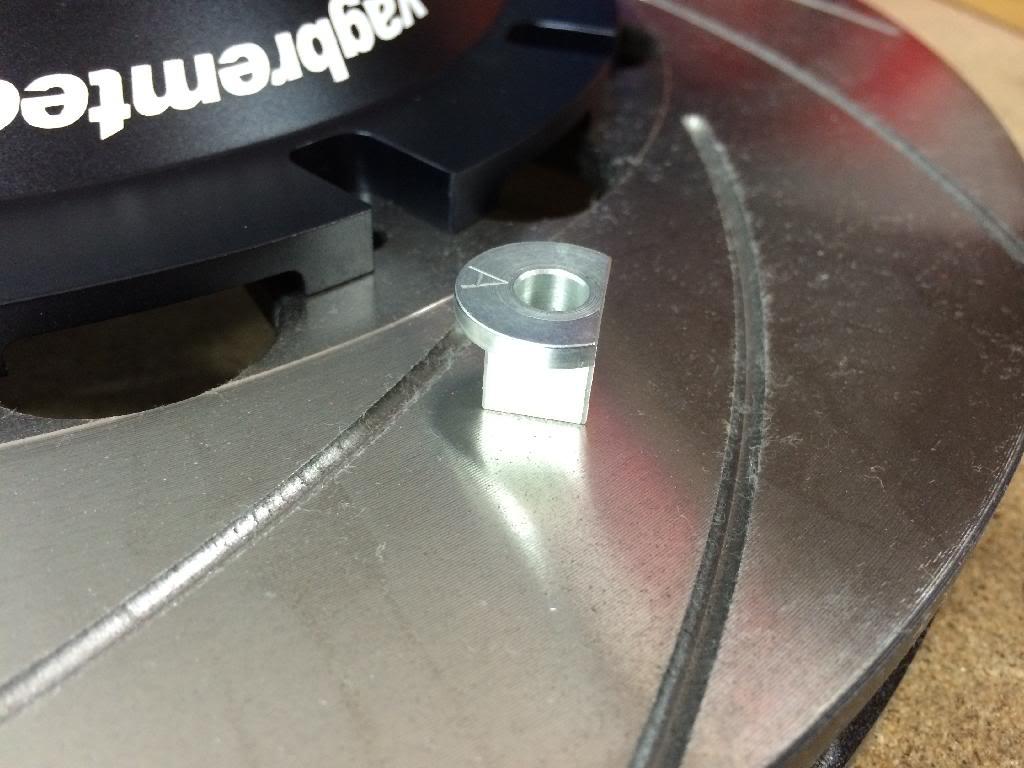
They insert into the slots on the bell, they're clever in that they slide within the slots so are unconstrained radially but are also taller than the thickness of the bell....this means that we can dial in about 0.2mm of axial float so that in the very most arduous of service they can find their own centre in the caliper. The top hat section stops them from falling to pieces
So heres the bobbin in the slot,
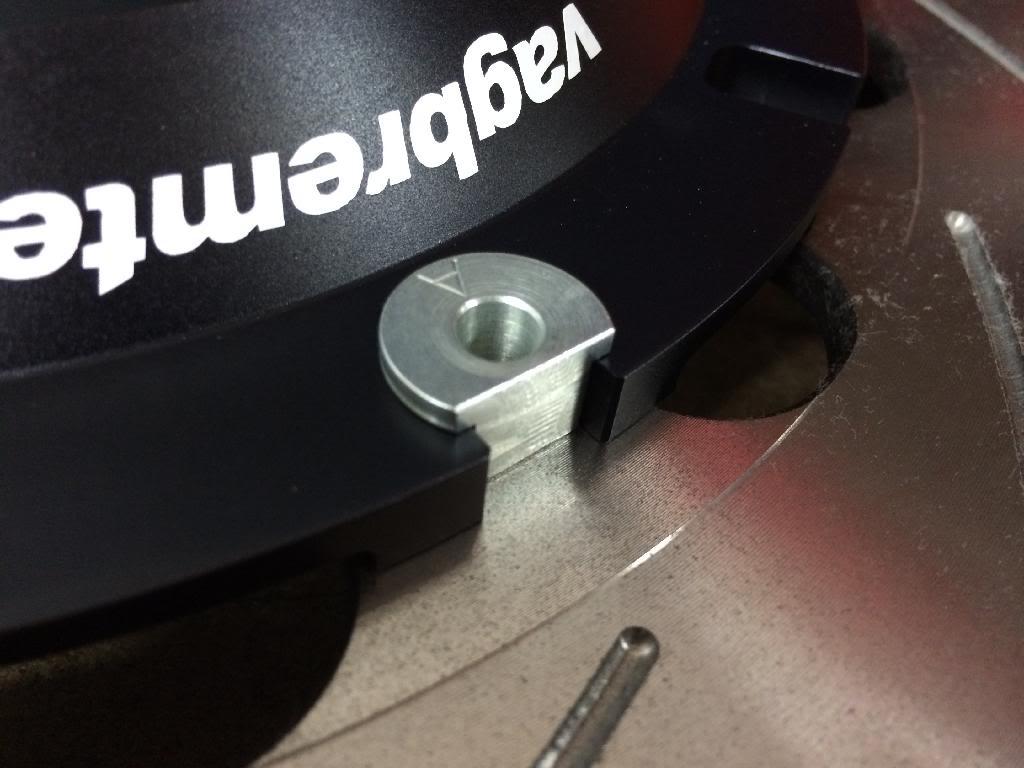
Repeat 12 times bolt it all together in a sensible tightening order and you have an assembly!
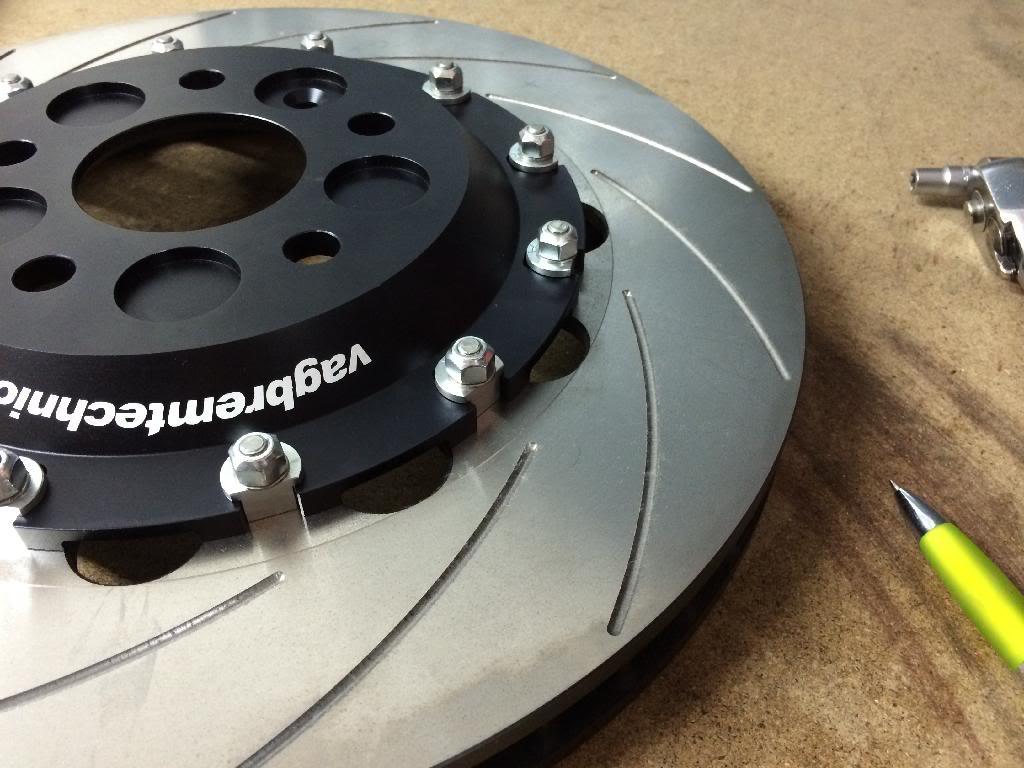
For road use we add some bobbin springs because as they are supplied to the race teams they're fookin noisy and rattle like crazy.....this we like, things rattling means that all is good generally its one of the first checks we do.
The first TTRS kits we did were like this and probably looking back a little too hard core for road use - only one person didn't moan and that was one Mr Jonny Cocker - funny that!
We ended up having our own Bobbin springs made right here in Rochdale, i didn't know it but Rochdale is the spring manufacturing capital of the country I've since found out and and 3000 small springs turned up minimum order!
The bobbin spring put the assembly in tension but allow expansion and thats how all the RS4/TTRS kits are made, a lot of guys on here have the TT kit on the Mk5//6 - its manufactured with all the above principles, the bell machining and fixing mechanism......
So here you go.....too busy to jerk about any more for now but I'll get some pics up of the carriers and the calipers and chat through pads over the next couple of days